Advanced Machinery Monitoring Solutions


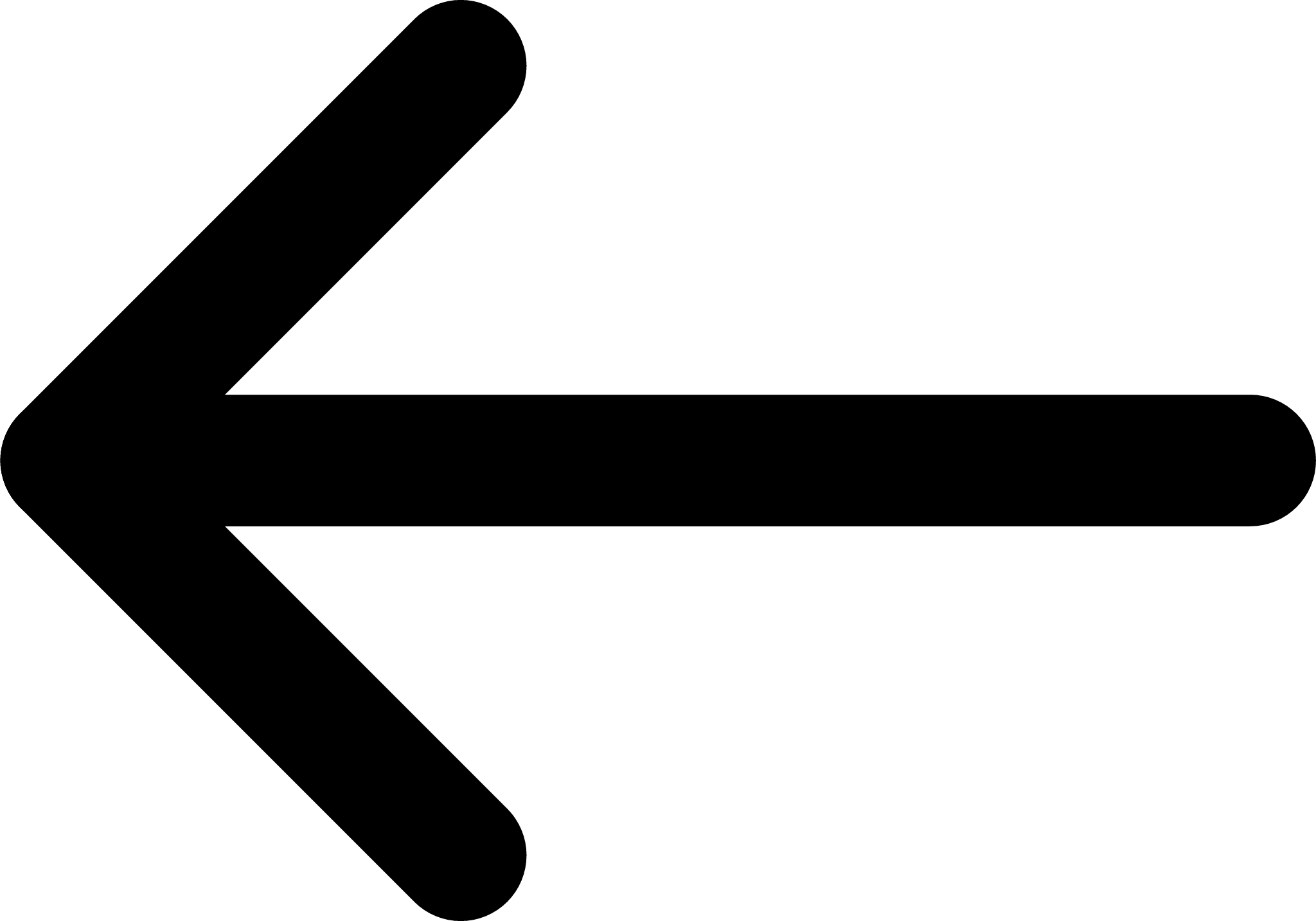
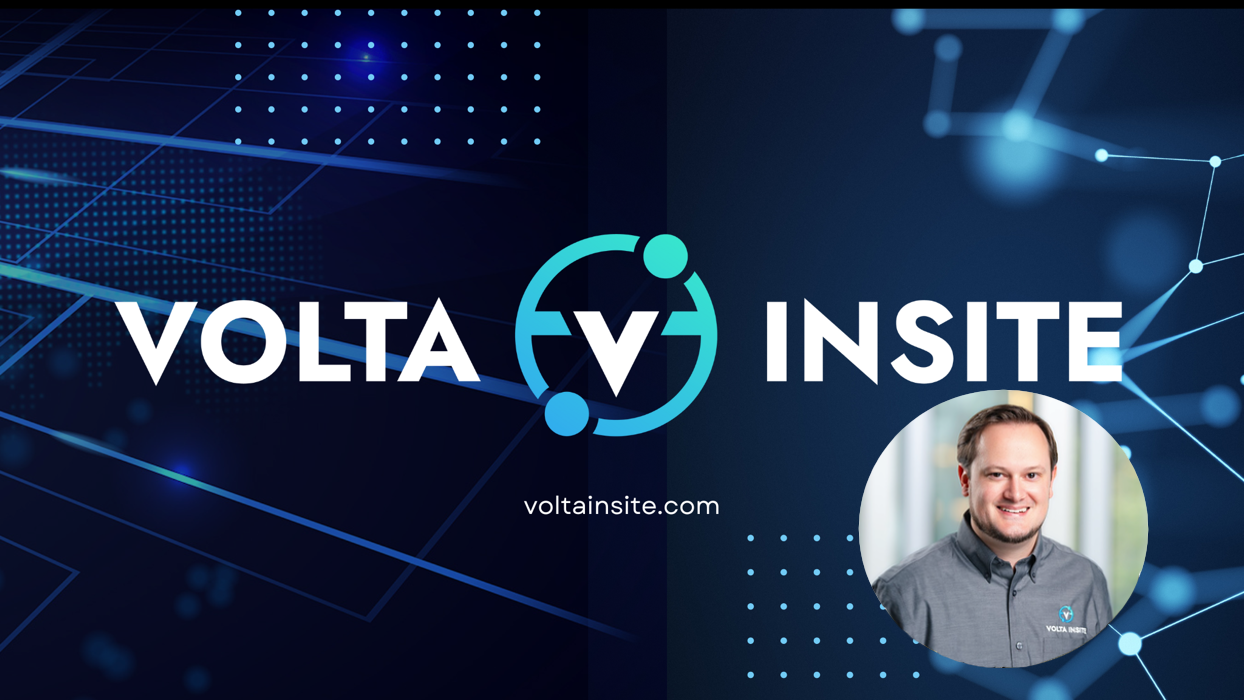
In the industrial world, an unexpected equipment failure can cost more than just repairs; it can mean a halt in production, a 70,000-ton production loss, or even risk to personnel's safety. Machinery monitoring systems and asset protection services act as the nerve center of a facility, guiding a team to make proactive decisions based on real-time process visibility. These systems serve as a cornerstone for condition-based maintenance, aiming to save an organization on maintenance costs and significantly reduce unplanned downtime.
What Is Machinery Monitoring?
Imagine a high-tech guardian watching over your machinery at all times, keeping an eye on every heartbeat of your powered equipment. This guardian is actually a Machinery Monitoring System, a sophisticated blend of software and sensors that listens to the pulse of your industrial machinery. With the precision of a surgeon, it tracks the health of each machine, measuring everything from temperature, vibration, and noise to more intricate parameters like torque and lubrication. Think of machinery monitoring as the constant collection and analysis of data from pieces of equipment, enabling you to catch even the slightest hiccup or sign of wear, before it turns into a full-blown problem.
Advanced analytics dive deep into the data, comparing current states with historical trends to detect early signs of degradation or failure. These systems can gauge centrifugal compressor performance or sense subtle changes in acceleration transducer signals, always with the goal of extending the life of the equipment and ensuring optimal performance.
The Role of Machinery Monitoring in Industrial Operations
The role of the system is multifaceted: protection, prediction, performance. It acts as your in-plant Technology Center, providing real-time data and analytics that turn every alarm level and signal into actionable advice. Continuous improvement is the name of the game, with the system working tirelessly to track status, issue alerts, and facilitate preventive measures. Holistic machine monitoring solutions blend real-time production visibility with asset management insights, granting companies the intelligence and predictive intelligence to stay ahead of the curve. As a result, operational efficiency skyrockets, and an overall 15-20% improvement in asset utilization is not just a goal—it's an achievable reality.
The Importance of Machinery Monitoring
Machine monitoring isn't just about catching problems; it's about gaining insights that lead to efficient operations and longer machine life. Our job is to make sure your machinery is always ready to perform.
Why Do We Monitor Machines?
To put it simply, we monitor machines because they are the lifeblood of any manufacturing or processing plant. Machinery is like an athlete; it needs regular check-ups to perform at its best. By monitoring, we hear the whispers of trouble before they turn into costly shouts. It's the difference between changing a belt during scheduled maintenance and shutting down an entire production line when it snaps unexpectedly.
The Benefits of Real-Time Data for Machinery Health
Real-time data is what turns a good operation into a great one. With instantaneous feedback, machines speak to us, telling us if they're running too hot, too hard, or off-balance. This conversation with your equipment, facilitated by our technology, can lead to vast improvements in efficiency and reliability. Real-time data empowers us to make smart, timely decisions, helping to prevent minor issues from becoming major disruptions. It's the heartbeat monitor for your machinery, giving you a clear view of your operation's health at any moment.
Advanced Monitoring Solutions and Their Impact
Delivering Visibility to Asset Health 24/7
Advanced monitoring solutions are the watchful eyes that never blink. They offer an unprecedented look at the condition of assets, around the clock. By effectively transforming every current and voltage signal into a meaningful narrative, they tell us how each piece of equipment lives and breathes. It's all about visibility—you're no longer checking on machinery at intervals; you're always watching, always aware. This breeds a new caliber of asset management where no unexpected event slips through the cracks.
Adding Predictive Capabilities to Existing Protection Systems
Integrating predictive capabilities into existing protection systems enhances their efficiency by shifting from a reactive to a proactive approach. This advancement equips machinery with the ability to foresee potential failures, akin to providing them with a sixth sense for self-preservation. It allows for preemptive action, such as scheduled maintenance and early problem resolution, effectively preventing minor issues from escalating into significant disruptions. This strategic foresight ensures that equipment operates smoothly, reducing downtime and avoiding unexpected failures.
Expanding on predictive maintenance strategies, the work by Truong Quang Vinh and colleagues introduces a novel approach through the implementation of a decision tree model for machinery monitoring and fault prediction. Their system, leveraging IoT technologies for real-time supervision and predictive analytics, demonstrates significant advancements in reducing downtime and enhancing machinery performance, showcasing a practical application in a factory environment.
Valve Monitoring for Maximizing Operational Efficiency
Valve monitoring is crucial in industrial plants for maximizing operational efficiency, acting much like tuning brass instruments in an orchestra to ensure optimal performance. This process involves not just identifying stuck or leaking valves but also analyzing patterns of wear and performance degradation. By leveraging this data, it's possible to maintain seamless operations and preemptively address efficiency losses, preventing them from escalating into significant operational issues.
Machinery Monitoring Applications and Use Cases
Turbomachinery and Unique Industrial Applications
Turbomachinery, like turbines and compressors, serve as the powerhouses in many industries. They demand eagle-eyed oversight, and that's precisely where advanced machinery monitoring shines. It not only listens to the typical thumps and screeches but also picks up on the whispers of performance issues, like subtle compressor vibration changes or discharge temperature deviations. This high-stakes game requires not just any monitoring, but the most astute, agile, and predictive kind—the kind that can tell if a machine will falter well before it actually does.
Enabling Lights-Out Manufacturing for Enhanced Productivity
Lights-out manufacturing, where operations run autonomously without human presence, boosts productivity by leveraging advanced monitoring systems. These systems oversee production continuously, performing micro-adjustments and signaling when issues arise, ensuring the manufacturing process proceeds efficiently even outside regular working hours. This approach maximizes efficiency and productivity, optimizing the use of machinery and significantly reducing utility and labor costs.
Essential Features of Machine Monitoring Platforms
Between the essential features of machine monitoring platforms and the advent of next-gen monitoring technologies lies a crucial transition. This era marks not just an improvement in technical capabilities, but a redefinition of what it means to monitor and maintain machinery effectively.
From Standard to Next-Gen: Comparing Monitoring Technologies
Machine monitoring technologies have evolved from the standard to the "next-gen," with each jump introducing sharper eyes and quicker reflexes. Older systems are the reliable standard-bearers; they watch and alert. But the new generation? They predict and advise. This shift is huge. We're talking about a leap from simple alarm systems to sophisticated networks that can learn from data, anticipate problems, and even suggest optimizations. This isn't just an upgrade—it's a transformation that arms companies with the foresight to avert costly downtimes.
The Advantages of Machine Connectivity Platforms Over Traditional Systems
Machine connectivity platforms are game-changers, bringing machines into the realm of the Internet of Things (IoT). Traditional systems might give you a snapshot of machine health, but connectivity platforms provide a full, live feed. We're seeing benefits like remote monitoring, updates in real-time, and analytics that offer deeper insights. Think of traditional systems like a toolbox; useful, but limited. Connectivity platforms? They're more like a Swiss Army knife with an infinite number of tools, always expanding, always adapting.
Online Condition Monitoring Products and How They Differ
Online condition monitoring products are diverse, with each bringing something unique to the table. Some are like vigilant sentries, focusing purely on indicating health in real time. Others are more like strategic advisors, delivering detailed analytics that inform maintenance schedules and operations. They differ in complexity, scalability, and intelligence. The one thing they all share? They turn raw data into the kind of actionable insights that keep the modern industrial world spinning confidently on its axis.
How to Get Started With Machine Monitoring
Beginning your journey with machine monitoring may seem daunting, but it’s like starting a new chapter in a book. First, assess your current equipment. Identify the types that would benefit most from monitoring, like those critical assets that, if failed, could shut down operations. Next, select a suitable system—one that not only detects but also predicts problems—ensuring that the technology matches your needs. Finally, plan for integration with your existing processes and train your team to understand and utilize the new data streams. Equip your team with the right knowledge, and you’re on your way to writing a success story in operational resilience.
Integrated Machine Monitoring: Scale and Flexibility
Flexible Deployment and Extending Visibility Across Facilities
Integrated machine monitoring isn't confined to just one corner of a factory. It's designed to flex and stretch, enveloping every aisle of machinery, no matter how vast the space. Think of it as a network that can widen or narrow to suit the whims of your operation. Perhaps you start monitoring just one critical line, then grow to cover the whole plant, and even remote facilities. The key is flexibility—the ability to adapt to various scales, bringing every vital sign of your machinery under vigilant watch, whether it's down the hall or across the country.
Assessing Process Machinery and Automation for Scaling Your Program
Scaling your monitoring program means taking a close look at the process machinery and automation already in place. It’s essential to evaluate each machine’s role and see where monitoring can bring the most impact—like a piece in a puzzle, it has to fit perfectly to complete the picture. Each addition should integrate smoothly with what's already automated, ensuring no piece of equipment is an isolated island and that data flows seamlessly through your production ecosystem. By strategically assessing and integrating, you can ensure your monitoring scales in harmony with your operation, supporting not just maintenance, but making smarter production decisions.
Choosing the Right Machine Monitoring Platform
Factors to Consider Before Selection: A Guided Chapter
Selecting a machine monitoring platform is much like choosing the right tool for a job—it has to be the perfect match for the task at hand. Before committing, consider compatibility with your existing systems, the complexity of the setup, and the kind of data insight you desire. It's crucial to choose a platform that aligns with your company's size and ambition, scales with your growth, and addresses specific pain points. Costs, customer support, and the ability to integrate with other automation systems are also pivotal chapters in this decision-making book.
Addressing the Ease of Use for Operators, Engineers, and Supervisors
Ease of use is more than a convenience; it's a necessity. A monitoring system should be intuitive for everyone interacting with it—from operators on the floor to engineers strategizing over data, up to supervisors overseeing operations. Complicated platforms can lead to resistance to adoption, errors, or overlooked insights. A user-friendly interface makes for smooth interactions and allows for the full strength of a monitoring platform to be harnessed. When even the most sophisticated analyses become accessible, your staff will engage with the technology more effectively, leading to smoother operations.
Create Custom States and Track Specific Machine Parameters
The real power of customization in machine monitoring comes from crafting custom states and diligently tracking specific machine parameters. A machine might operate within acceptable ranges under standard conditions, but when the going gets tough, those ranges may shift. By setting custom states, you can keep tabs on nuanced performance changes, ensuring you're always ahead of the curve. Tailoring the system to monitor parameters specific to your operation means that from a sea of data, you're able to fish out the most relevant information—giving a new level of refined control over your machinery’s operation and health.
Key Takeaways
-
Machinery health is critical: Continuous monitoring catches issues early, allows for swift action, and keeps industrial operations running smoothly.
-
Predictive maintenance transforms operations: It reduces unplanned downtime, saves costs, extends machine life, and maintains product quality and safety standards.
-
Technology evolves: From standard alarm systems to advanced predictive analytics, machine monitoring technologies are getting smarter, facilitating proactive maintenance strategies.
-
Integration and scalability are key: Effective machine monitoring must integrate seamlessly with existing systems and be scalable to cover all necessary assets.
-
Customization is crucial: Machine monitoring platforms should be tailored, allowing for specific parameters to be tracked and ensuring data relevancy.
FAQs about Machinery Monitoring
Can Machine Monitoring Integrate With Other Systems to Automate Data Flow?
Absolutely. Most modern machine monitoring solutions are designed to play well with others, meaning they can integrate smoothly with various systems you may already use. These can range from enterprise software to mobile tracking options. The goal is to automate the flow of data between systems, so you get a seamless stream of information that offers a comprehensive view of your facility’s operations.
How Can Effective Machinery Monitoring Contribute to Safety and Compliance?
Effective machinery monitoring is a cornerstone for safety and compliance in any facility. It alerts engineers to potential hazards before they become dangerous, ensuring that machinery operates within safe parameters. Moreover, regulatory compliance often requires proof of such monitoring. By maintaining detailed logs and detecting anomalies, monitoring systems help ensure that your operation meets the necessary safety and compliance standards.
How Can I Ensure My Machine Monitoring Solutions Stay Current With Industry Advances?
Staying current with industry advances is crucial, and it largely depends on choosing a monitoring solution that prioritizes updates and evolution. When selecting your system, look for providers that offer regular updates, support new sensor technologies, and incorporate advanced analytics. By partnering with a company committed to continuous improvement, your monitoring solutions will evolve alongside industry innovations.