Machine Health Monitoring for Improved Maintenance


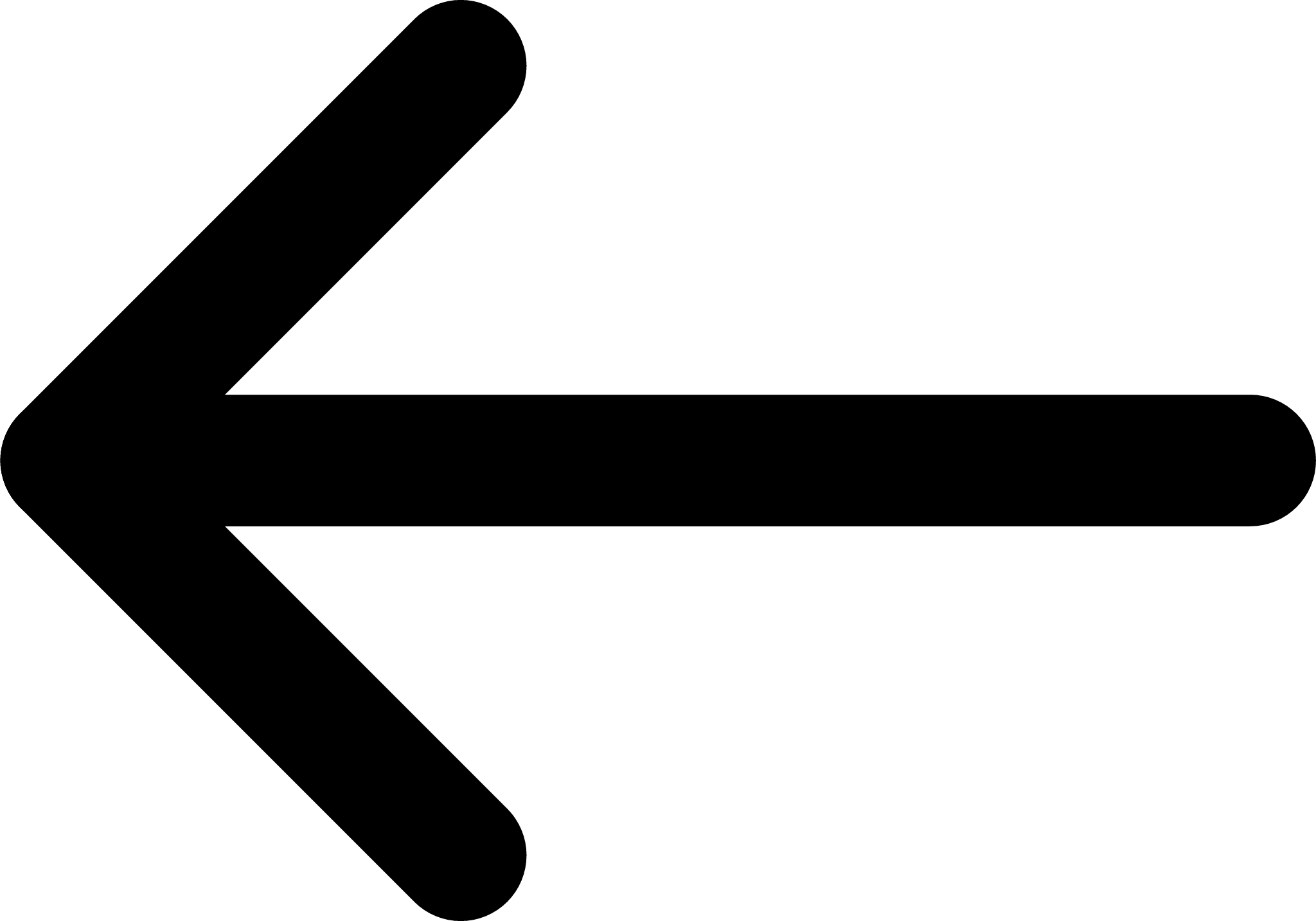
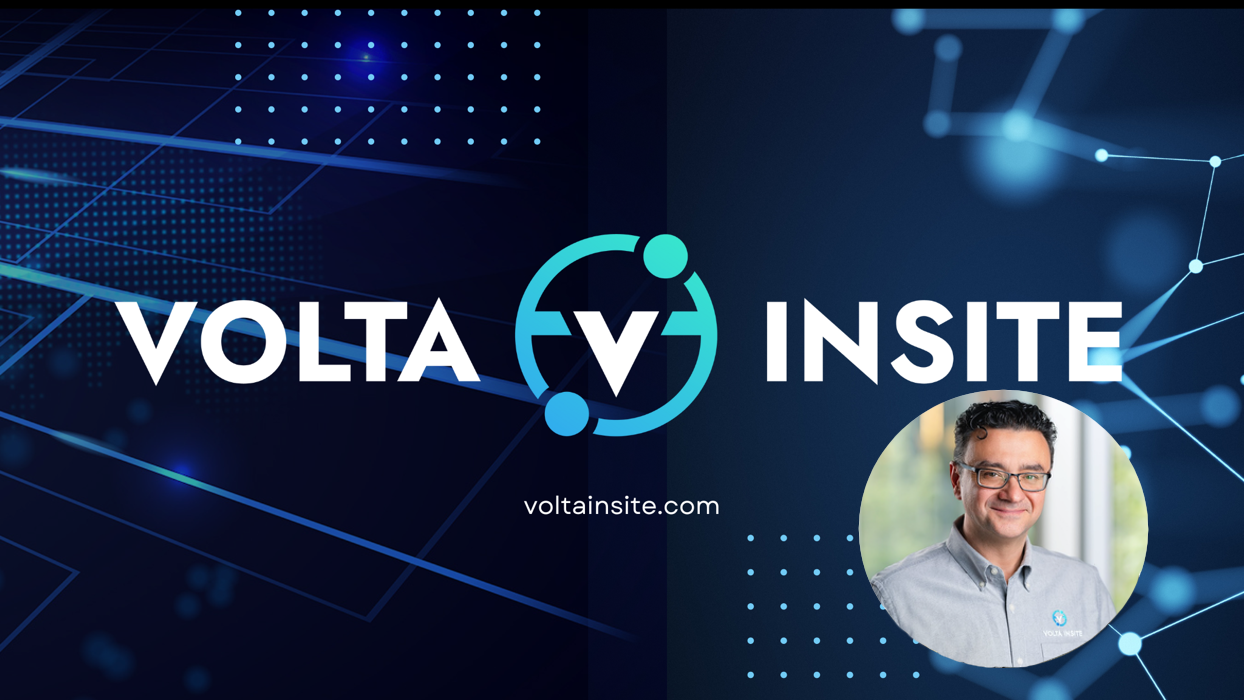
Imagine you're driving a car—dashboard lights flicker on when something needs attention; oil needs changing, or a tire is low. The concept of machine health monitoring is similar but on a much larger and more complex scale. It's a vital part of the industrial world, ensuring huge production machines run smoothly around the clock.
What Is Machine Health Monitoring?
Machine Health Monitoring, a branch of this predictive maintenance, escorts the health of a factory's equipment with finesse. It uses advanced tools like vibration sensors and analytics software that pick up tiny changes in a machine's dance, signs that it's wearing out or in trouble. Imagine having a friend who continuously whispers secrets about your car's health into your ear—that's machine health monitoring for industrial equipment.
Difference Between Condition Monitoring and Machine Monitoring
The key is in focus and scope. Condition Monitoring is the stethoscope listening to a machine's heartbeat, measuring indicators like vibration, noise, temperature, and pressure in real-time. Think of it as the ongoing check-ups that give you continuous snapshots of your machine's health. It targets specific indicators to diagnose existing problems with equipment sets, allowing for necessary fixes before things get worse.
On the other hand, Machine Health Monitoring is the broader health plan that includes regular condition check-ups alongside predicting potential future challenges. It's a blend of real-time condition data and predictive analytics. While condition monitoring tells you what's happening now, machine health monitoring combines this with powerful prediction algorithms—like Recurrent Neural Networks—to tell you what might happen next.
Why Is Machine Health Monitoring Important?
Machine health monitoring is the guardian of the industrial realm. It arms technicians with an understanding of a machine's inner workings through data-driven insights. Here’s why it’s crucial:
-
Prolonged Equipment Life: By detecting early signs of wear and potential failures, machine health monitoring can recommend timely maintenance, thus extending the life of critical assets.
-
Enhanced Safety: Machines in good health pose less of a risk to the wonderful folks who operate them every day, making machine monitoring not just a tool for efficiency, but a guardian of safety.
-
Improved Efficiency and Productivity: Healthy machines don't just hum along—they sing songs of peak performance, churning out products without the hiccups that come with breakdowns and repairs.
-
Cost Savings: When you catch a problem before your machine throws a tantrum, you save on expensive fixes. Prevention is not just better but often cheaper than a cure.
-
Better Decision Making: Armed with data, those in charge can make smarter, facts-based decisions, tweaking operations like a maestro to keep the rhythm of production in blissful harmony.
Monitoring Techniques and Technologies Involved
Diving deeper into the art of machine health monitoring unveils an array of sophisticated techniques and cutting-edge technologies that work in unison to prevent industrial catastrophe. These methods are more than tools; they are the keys to unlocking a future of flawless operation.
Machine Condition Monitoring Techniques
The foundation of machine health monitoring lies in its techniques, honed to catch the faintest whispers of machine distress. Key techniques include:
-
Vibration Analysis: A machine's shake or rattle can speak volumes. Vibration sensors detect anomalies in movement patterns, often indicating wear or misalignment.
-
Thermography: Cameras that see heat can spot trouble areas long before they burn out. Overheating components can be the first sign of friction or electrical issues.
-
Oil Analysis: It's like checking the blood of your machinery. Sampling and analyzing lubricants can reveal contamination or particles that hint at wear and tear within.
-
Ultrasonic Monitoring: High-frequency sounds, undetectable by human ears, can signal leaks or electrical discharges, alerting technicians to take action.
When Technicians Are Needed: Advanced Planning for Repairs
Machine health monitoring gives you the "when" for maintenance, but skilled technicians provide the "how." They plan advanced repairs based on predictive cues and prepare accordingly:
-
During quieter production periods, repairs are scheduled to minimize impact on output.
-
Technicians receive alerts on their devices, prompting reviews of diagnostic analytics to strategize the fix.
-
With adequate notice, the necessary parts and tools are assembled, erasing the need for hasty scrambles when machines go rogue.
Data Analytics in Machine Health Monitoring
The landscape of machinery has been permanently altered by data analytics. This isn't hyperbole—it's a revolution where data is the kingmaker, turning ordinary machinery into self-aware components of industrial success.
Integration of Big Data Analytics and Machine Learning in Machine Health Monitoring
Big data and machine learning are the dynamic duo in the saga of monitoring. Vast streams of sensor data merge into big data frameworks, where algorithms chew through numbers, spotting trends, and forecasting failures. The fusion of big data analytics with machine learning creates self-improving models, refining their prediction prowess as more data is fed. These integrations meld into systems that alert technicians of the minutiae and magnitude of potential problems, all in real-time.
Building upon the integration of machine learning in machine health monitoring, the study by Rui Zhao et al. introduces an innovative approach through the use of Local Feature-Based Gated Recurrent Unit (LFGRU) Networks. This method enhances predictive maintenance by efficiently analyzing raw sensory data for fault detection and prognosis. Their work not only demonstrates the effectiveness of combining handcrafted and automatic feature learning but also highlights the potential for improving tool wear prediction, gearbox fault diagnosis, and bearing fault detection.
Continuous and Run-Up & Coast-Down Monitoring
Machinery, like living beings, has life stories told through data:
-
Continuous monitoring captures these stories in uninterrupted streams, offering a real-time chronicle of machine health.
-
Run-up and coast-down analysis slices through data collected during starts and stops of machines, revealing health insights during critical stress phases.
-
This combo delivers a full lifecycle view, from the steady rhythm of operation to the vulnerabilities seen in transitions, ensuring nothing is overlooked.
At every turn, analytics in machine health monitoring is growing smarter, sharper, and more indispensable. It's a field not just informed by data but powered, driven, and elevated by it. Data analytics doesn't just support the structure of machine health monitoring—it's a load-bearing pillar, holding up future industry aspirations with the might and mystery of numbers turned into narratives.
Challenges and Opportunities in Machine Health Monitoring
With its unwavering eye on the health of industrial beasts, machine health monitoring weaves a complex web of challenges and opportunities. It's a playing field where every hurdle vaulted opens the door to new potential, charting a path through uncharted industrial terrain.
Ensuring Reliability in Prediction Capabilities
The reliability of predictions is the cornerstone of machine health monitoring:
-
The strength of predictions hinges on the quality and quantity of data—garner the best, ensure the rest.
-
Machine learning models require constant nurturing with updated data to avoid the pitfalls of obsolete predictions.
-
Calibration and validation against real-world outcomes are must-do's, not just best practices, to bank on the credibility of machine health foresight.
Navigating Unavailability of Technical Expertise in Remote Locations
The know-how required for machine health monitoring is not evenly spread across the globe:
-
In remote corners, where the machines grind away far from the tech hubs, the scarcity of expertise poses significant challenges.
-
Technology shoulders part of this burden, with remote monitoring and diagnostics bridging the physical distance.
-
The opportunity herein lies in upskilling local teams using digital tools and training, potentially transforming remote site dynamics.
The landscape of machine health monitoring is like an adventure novel, with each page flip revealing trials and triumphs. The resilience of these systems against unpredictability and their ability to spin data into predictive gold are testaments to human ingenuity in the face of industrial behemoths. While the road ahead holds challenges, it's lined with opportunities—shining beacons guiding towards a horizon where machinery ailments are no more than a whisper in the wind, caught and cured before they can ever roar.
Applications and Implementations of Machine Health Monitoring
Machine health monitoring isn't just a concept; it's a robust and versatile practice that has made a leap into real-world applications across various industry segments. It has reshaped how businesses approach machinery maintenance, transforming reactive practices into proactive prowess.
Turbomachinery Applications
In the high-stakes arena of turbomachinery—where jet engines, turbines, and large compressors reign—machine health monitoring takes center stage:
-
Sensors placed on these powerhouses track performance data, revealing the status of high-speed rotating parts.
-
Advanced algorithms assess condition data to prevent faltering performance, which could lead to expensive, if not catastrophic, failures.
-
Predictive diagnostics inform operators of the best times for maintenance, maximizing machine uptime and ensuring the smooth operation of crucial equipment.
Integrating Machine Health Monitoring in Different Industries
Sector by sector, machine health monitoring adapts, showcasing its versatility:
-
Automotive: Automotive manufacturers integrate it to predict bottlenecks, reducing idle times and ensuring a steady flow in production.
-
Aerospace: In aerospace, long-term asset integrity is paramount. Machine health monitoring manages this through vigilant vibration and temperature observations.
-
Food and Beverage: It ensures food safety by catching machinery degradation that could compromise product integrity in the food and beverage industry.
-
Mining: For mining operations, where equipment is pushed to its limits, machine health monitoring transforms the rugged environment by foreseeing the breakdown of crushers and conveyors, crucial to the earth-churning process.
Minimize Unplanned Downtime in Various Industries
Unplanned downtime can be the villain in industries, lurking, ready to leap out and disrupt at the worst moments. Whether on the shop floor of automotive giants, the assembly lines of electronics, or the pumps and compressors of oil and gas facilities, downtime is costly. But machine health monitoring is the superhero here.
-
Manufacturing: No manufacturer wants stilled assembly lines. Machine health monitoring predicts issues, keeping the army of robots and conveyors marching in time.
-
Energy: In energy, whether chasing the wind or drilling deep into the earth, downtime means lost opportunity and revenue. Monitoring health keeps the turbines spinning and rigs pumping smoothly.
-
Healthcare: Hospitals rely on machines just as much as patients rely on doctors. Health monitoring here means life-saving devices are always ready to go.
-
Transportation: From planes to trains, all have one thing in common—reliance on pristine machinery. Monitoring ensures that movement is constant and safe, avoiding delays and mishaps.
By embracing machine health monitoring, industries worldwide are saying goodbye to the headaches of unexpected breaks and shutdowns and hello to smooth, uninterrupted operation. This tool isn't just about avoiding disasters; it's about creating an environment where efficiency thrives, and each piece of equipment can achieve its destined performance.
With each industry peddling its unique challenges, machine health monitoring rises as a tailored sentinel. It is the unseen but ever-present guardian that subtly integrates into systems and processes, weaving a net that catches issues before they freefall into fiascos. These implementations highlight the adaptability of machine health monitoring—molding it to not only meet but surpass the expectations of asset management and protection in today's technology-driven world.
Key Takeaways
As we pull back from the intricate patterns of machine health monitoring, it's time to sew together the fundamental threads of our discussion:
-
Predictive Maintenance: Like meteorologists of machinery, predictive maintenance harnesses the power of data and analytics to forecast and forestall machine failures, ensuring sustained production and efficiency.
-
Technological Convergence: The fusion of vibration sensors, data analytics, deep learning, and cloud platforms has reinvented machine health monitoring, turning it into a keystone of industrial operation and maintenance strategy.
-
Versatility Across Industries: From the constant churn of manufacturing to the peak demands of energy production, machine health monitoring shows remarkable adaptability, proving its worth across a multitude of sectors.
-
Market Expansion: Driven by the relentless quest for optimization and guided by technological advances, the machine health monitoring market is burgeoning, opening new horizons for businesses to operate with unprecedented precision and reliability.
-
Future-Focused: The path forward is lined with challenges, yes, but even more so with opportunities—a testament to the resilience and innovation inherent in the field of machine health monitoring.
Grasping these takeaways arms one with the knowledge to appreciate the sophisticated dance of machine health monitoring—a dance that keeps industries whirling smoothly, machinery humming healthily, and production targets hit with spirited accuracy.
FAQs:
The journey of understanding machine health monitoring spans from the abstract to the concrete, with questions emerging along the way. Below are concise answers to some of the most common queries.
What Faults Can Machine Health Monitoring Detect?
Machine health monitoring is the vigilant sentinel of industrial operations, able to detect a broad array of faults:
-
Mechanical Issues: Such as unbalanced rotors, misaligned shafts, or degrading bearings gearboxes, pulley systems and even unbalanced loads.
-
Electrical Problems: Including power quality issues, voltage imbalances, insulation breakdowns, failing distribution equipment contacts, loose connections and ground faults.
-
Operational Difficulties: Like process imbalances, flow disruptions, and performance inefficiencies.
-
Thermal Anomalies: Overheating components or abnormal temperature patterns that signal potential failures.
How Does Machine Health Monitoring Integrate With Existing Enterprise Software?
Integration is a dance of compatibility and functionality:
-
APIs and Protocols: Standardized data exchange methods allow machine health monitoring systems to communicate with enterprise software, ensuring seamless data flow.
-
Modular Design: Many monitoring systems are designed to be plug-and-play, slotting into existing technology ecosystems without significant upheaval.
-
Customized Solutions: Providers often tailor integrations to fit specific enterprise needs, ensuring a snug fit with existing business processes and workflows.
What Future Developments Are Expected in Machine Health Monitoring Technology?
The horizon glows with the promise of advancements:
-
AI and Automation: Further developments in artificial intelligence will refine predictive analytics, making autonomous machine health interventions a reality.
-
Wireless and IoT Evolution: Enhanced wireless solutions will make monitoring more efficient, with greater coverage and less invasive sensor networks.
-
Big Data Optimization: Refinement in handling and analyzing voluminous data will drive faster, more accurate predictions with less human intervention.
Machine health monitoring remains an ever-evolving field. Each leap in technology or methodology enhances the system’s ability to prevent, predict, and protect, thus ensuring machinery’s longevity and efficiency. The future—even with its undeniable unknowns—holds robust promise for the health of machines worldwide.