Systematic Approach to Condition Monitoring


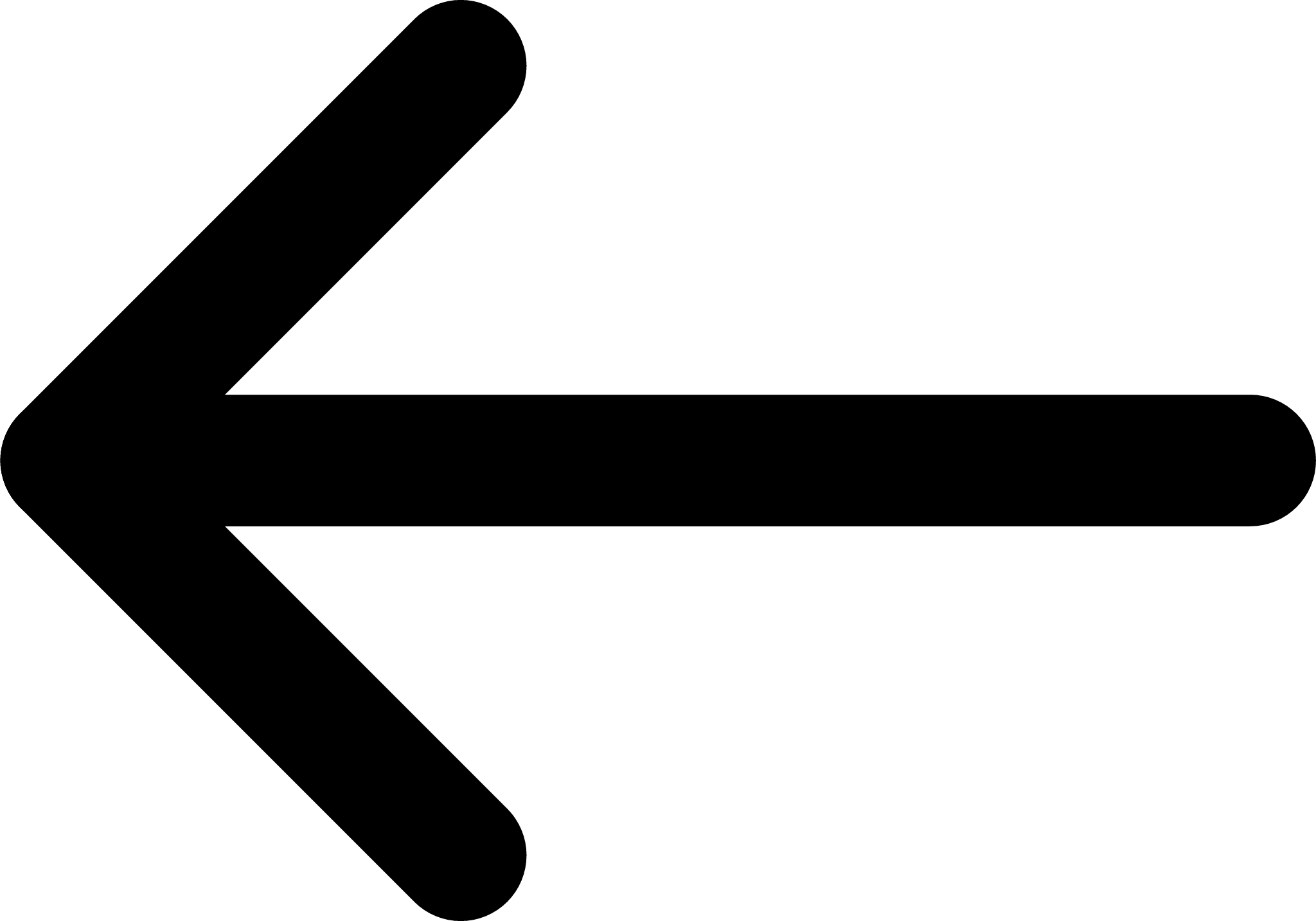
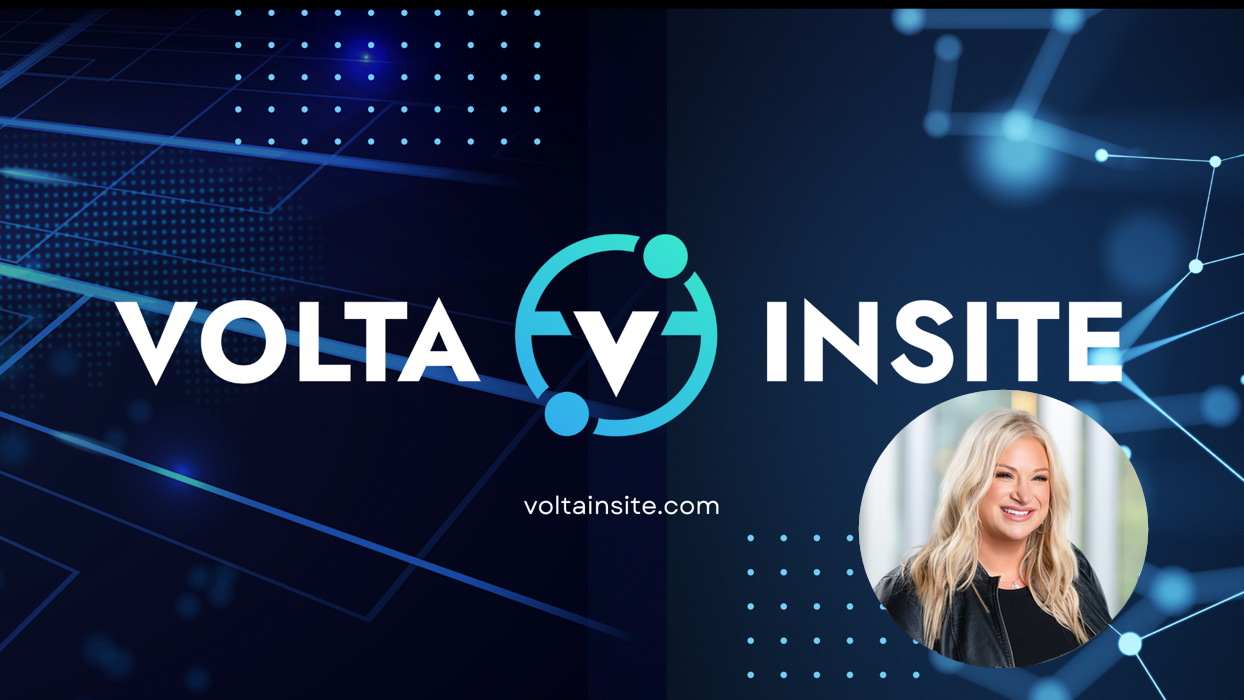
Condition Monitoring is a critical strategy in preventing machinery downtime, crucial for maintaining profit in industries. It monitors equipment health by observing factors such as temperature and vibration, enabling early detection of issues. This proactive maintenance approach is key in improving machine health and operational efficiency, marking a significant advancement for operations dependent on machinery.
What Is Condition Monitoring?
Condition Monitoring is the cornerstone of modern industrial maintenance planning. It's a commitment to continuously checking the vital signs of equipment—like temperature, vibration, and noise levels—to understand their well-being. This proactive approach is the opposite of the reactive approach, which only addresses problems after a breakdown. In essence, Condition Monitoring gives a voice to each machine, allowing it to tell us when something isn't quite right.
The Role of Condition Monitoring in Predictive Maintenance
Condition Monitoring is a key element in the predictive maintenance approach. It detects signs of potential failure long before a breakdown, steering away from unplanned downtime, which can be costly and disruptive. By paying attention to fault frequencies and trend data, maintenance personnel can pinpoint issues with bearings or imbalances that, if ignored, could lead to total machine failure. Through Condition Monitoring, alerts are sent out, and teams are mobilized to tackle issues at the optimum time for both machine health and production efficiency.
Online vs Offline Condition Monitoring
Two primary types of condition monitoring exist: online and offline. Online monitoring systems stay connected to critical machinery continuously, delivering real-time data and alerts to plant managers and maintenance teams. Offline condition monitoring, on the other hand, involves periodic inspections where data is collected manually. Online systems offer a better window into the immediate state of equipment but may require a greater initial investment and infrastructure.
Continuous Monitoring and Its Advantages
Continuous monitoring is a constant, vigilant eye watching over every oscillation in vibration, every glitch in electrical signals, every spike in temperature. Its advantages are clear: it transforms data into actionable insights, keeps maintenance costs down, and minimizes downtime. Continuous monitoring systems know no rest, ensuring that every anomaly is caught, and maintenance downtimes are strategically planned, not panicked responses to catastrophic failures. They are the bedrock upon which dependable, efficient maintenance rests, ensuring that uptime is maximized and the cost of failure is minimized.
The Process Behind Condition Monitoring
The journey of Condition Monitoring is as intriguing as a detective's narrative, filled with clues, analysis, and a meticulous pursuit of truth about the conditions of industrial assets.
How Does Condition Monitoring Work?
At its core, Condition Monitoring works through a robust network of sensors and devices, each acting as a vigilant sentinel. They gather a symphony of signals—vibrations, acoustics, temperature, pressure, and more—from machinery. This information, channeled through cutting-edge telemetry, feeds into sophisticated algorithms. These algorithms are the sleuths, sifting through mountains of data to detect the faintest whisper of equipment anomalies.
Baseline Data Measurement and Analysis
Building a case for machine health begins with baseline data—a documented profile of normal operating parameters. This is the 'fingerprint' of an asset's performance. Establishing this benchmark involves measuring the usual vibration levels, temperature signatures, and other critical indicators during regular operation. It's a process as much about understanding what is normal as it is about detecting what is not.
Ongoing Monitoring for Consistent Performance
Ongoing monitoring is like an unwavering pulse check on your assets. By continuously comparing real-time data against the baseline, maintenance teams can recognize deviations that signal wear, misalignment, or other potential faults. This persistent vigilance helps in diagnosing issues well in advance, ensuring that maintenance action is taken before those issues escalate into equipment failures.
Types of Condition Monitoring
Venturing deeper into the world of Condition Monitoring, we discover an arsenal of techniques, each tailored to uncover specific types of issues within the industrial panorama.
Vibration Analysis and Dynamic Monitoring
Vibration Analysis serves as the pulse-check of machines. It senses the oscillations and disruptions that channel the tales of imbalance, misalignment, or even structural compromises. Dynamic Monitoring takes this further, scrutinizing the machine's performance across various operation scenarios, ensuring that any potential for disturbance is monitored under the full spectrum of working conditions.
Electrical Monitoring and Motor Circuit Analysis
Electrical Monitoring fixes its gaze on the lifeblood of machines: their electric currents and voltages. It listens for inconsistencies, recognizing the faintest signs of electrical anomalies that hint at issues like insulation faults or imbalanced power supply. Motor Circuit Analysis zooms in on motors, dissecting their electrical signatures to catch the early sounds of motor trouble.
In the discussion on fault diagnosis techniques, the work by S. Nandi and H.A. Toliyat offers crucial insights. Their review addresses the evolution of fault diagnosis in electrical machines, highlighting the shift towards automated detection through advanced signal processing and Motor Current Signature Analysis (MCSA). This study underlines the complexity of diagnosing multiple faults and suggests a multi-pronged approach for future research.
Thermography and Temperature Measurements
Thermography acts as the unseen eye, visualizing the heat map of operation. It detects changes in temperature that suggest overheating, poor lubrication, or friction issues. Through precise temperature measurements, equipment health is assessed, guarding against the silent threats that heat can impose on the stability of machinery.
Oil Analysis and Tribology
Oil Analysis dives into the very lifeblood of machinery, inspecting the chemical composition and contamination levels of lubricants. This process, part of the wider field known as Tribology, investigates wear particles in fluids to detect internal degradation of machine components, ensuring that the smooth operation is aided by clean and fit-for-purpose oil.
Ultrasonic Monitoring and Acoustic Analysis
Ultrasonic Monitoring harnesses high-frequency sounds, beyond human hearing, to glimpse into the mechanical integrity of assets. It picks up the telltale signs of leaks or discharges. Acoustic Analysis pinpoints noise patterns that deviate from the norm, thereby flagging issues like bearing failures or gas escapes long before they escalate into operational hazards.
Benefits of Condition Monitoring
Condition Monitoring transcends mere machinery oversight; it fortifies operations, instills confidence among stakeholders, and ushers in an era where every second of production counts and safety is an unwavering priority.
Preventing Unplanned Downtime and Its Cost Implications
Preventing unplanned downtime is perhaps the most immediate benefit of Condition Monitoring. The ability to foresee and forestall issues allows for repairs on your terms, not in response to a crisis. Anticipating failure saves not just on the direct costs of repairs, but also on the supplemental costs associated with downtime—lost production, expedited shipping for parts, overtime labor, or worst of all financial performance penalties for missing deadlines.
Protecting Your Other Assets
Condition Monitoring is a guardian, not just of the targeted machines but of your entire operation. For instance, when an undetected fault in one component can lead to systemic overloads, Condition Monitoring serves as an early warning system. It protects adjoining assets from the ripple effects of a failure, safeguarding the health of your full inventory of equipment.
Improving Asset Efficiencies and Overall Maintenance
By harnessing Condition Monitoring, facilities experience enhanced maintenance scheduling based on actual need rather than routine checks. This pushes the performance envelope of assets, optimizing their efficiency and lifespan. Maintenance teams become more strategic, allocating resources wisely and bolstering overall machinery performance.
Enhanced Safety through Early Anomaly Detection
Safety, the non-negotiable tenet of industry, is significantly reinforced by early detection of equipment anomalies. Condition Monitoring mitigates the risk of accidents due to equipment failures, ensuring that all operations stay within the bounds of safety regulations. This proactive approach benefits not just machinery and production but, vitally, the human elements of your facility.
Considerations in Condition Monitoring
Adopting Condition Monitoring is not without its hurdles. Recognizing these challenges is as crucial as appreciating the benefits, ensuring that the implementation is realistic, sustainable, and aligned with the company's operational philosophy.
Weighing the Installation and Operational Costs
Initial installation costs for Condition Monitoring systems systems are an investment. Facilities should evaluate the initial cost against the long-term savings and increased uptime to ensure that it makes economic sense. Additionally, operational costs such as software licenses, data storage, and ongoing system maintenance must be factored into the financial planning.
Handling Unpredictable Maintenance Scheduling
One of the paradoxes of Condition Monitoring is that while it aims to predict and schedule maintenance, the resulting data can sometimes suggest immediate, unscheduled interventions. This unpredictability requires flexibility in staffing, with maintenance teams ready to respond to urgent maintenance needs that Condition Monitoring systems might reveal.
Implementing Condition Monitoring in Your Facility
Welcoming Condition Monitoring into a facility is a transformative process that marries technology with strategic foresight, ultimately leading to a finely-tuned operation.
How to Set Up Condition Monitoring
To integrate Condition Monitoring, it’s essential to start with a clear picture of your facility's operations and identify which assets are critical. Select appropriate monitoring systems tailored to those assets and establish baseline measurements. Equip maintenance teams with training on sensor data interpretation, and ensure compatibility with existing industrial systems for seamless data transfer and analysis.
Monitoring the Data from Your Machines With Smart Sensors
Smart sensors are your machines' translators, converting vibrations, temperatures, and acoustics into data. Position them strategically on key components to capture comprehensive health indicators. These sensors communicate with maintenance teams, signaling when equipment is straying from its normal, healthy rhythm. It's a system that hinges on attentive listening across a network of interconnected devices.
Ensuring the Health of Your Equipment With Expert Services
Expert service providers bring a wealth of experience. They offer not just tools, but a Health Management Service, where a dedicated team interprets data, offers diagnostics, and advises on maintenance strategies. This partnership benefits facilities by aligning Condition Monitoring practices with industry best standards, all while enhancing equipment reliability and uptime.
Machine Learning for Enhanced Equipment Analysis
Machine Learning is changing the game, shifting Condition Monitoring from a binary alert system to an intelligent prognosticator. By feeding machine learning algorithms with historic and real-time data, they become adept at predicting issues before they even arise. These systems learn the unique acoustic signatures of each asset, continuously fine-tuning their sensitivity to deviations and improving the accuracy of their diagnostics over time.
Applications Beyond Manufacturing
The ingenuity of Condition Monitoring isn't confined to the manufacturing industry. It stretches its reach into numerous fields, ensuring that its benefits can be harnessed in diverse applications to maintain asset health and operational efficiency.
Condition Monitoring for Non-Manufacturing Industries
In the world of heavy process industries, power generation, and even hospitality, Condition Monitoring plays a critical role. It ensures the smooth operation of HVAC systems, power plants, and other equipment that require stringent oversight. In fields like healthcare, it guarantees the reliability of life-saving medical equipment. It even extends into transportation, monitoring the condition of fleet vehicles to preemptively address mechanical issues and ensure safety.
How Manufacturers Benefit From Condition Monitoring
Manufacturers gain significantly from Condition Monitoring's capacity to predict equipment malfunctions before they result in production stoppages. It equips them with tools to avoid costly downtime and maintain production at optimal levels. Additionally, it provides valuable data for continuous improvement initiatives—driving efficiency gains and competitive advantage not only in output quality but also in maintenance resource allocation and energy consumption.
Key Takeaways
-
Predictive Power: Condition Monitoring underlines the shift from reactive to predictive maintenance, saving industries from the unpredictability and high costs of equipment failure.
-
Technological Integration: The integration of IoT, AMS, smart sensors, and Machine Learning presents a formidable force, modernizing Condition Monitoring capabilities and predictive insight accuracy.
-
Economic and Operational Advantage: Both manufacturing and non-manufacturing industries benefit from Condition Monitoring's potential to improve asset efficiency, optimize maintenance resource use, and enhance safety protocols.
-
Strategic Implementation: How Condition Monitoring is integrated—considering the balance between cost, complexity, and capability—can make or break its effectiveness in improving equipment uptime and longevity.
FAQs
How Does Condition-Based Maintenance Work?
Condition-Based Maintenance (CBM) relies on the actual condition of machinery rather than predetermined schedules. Using data from monitors and sensors, CBM identifies potential problems before they become actual faults. Maintenance is thus performed based on evidence of need, which optimizes maintenance work and prevents unnecessary procedures on machinery that’s still in good condition.
What Conditions Can You Monitor On A Machine?
On any given machine, a variety of conditions can be monitored, including:
-
Vibration: Identifies imbalances, misalignment, or wear in moving parts.
-
Temperature: Indicates overheating or friction issues.
-
Acoustic Emissions: Can detect leaks or changes in mechanical movement.
-
Electrical Signals: Reveals issues with power supply, wiring, or insulation.
-
Oil Quality: Shows contamination, metal particles, or chemical changes signaling wear or corrosion.
What Are the Advantages of Integrating IoT With Condition Monitoring?
The integration of IoT with Condition Monitoring offers several advantages:
-
Enhanced Data Collection: Allows for the gathering of vast amounts of real-time operational data from machinery.
-
Improved Maintenance Responses: Enables quicker and informed decisions with immediate data analysis.
-
Predictive Maintenance: Facilitates predictive maintenance operations by learning patterns from the data and alerting to potential future failures.
-
Remote Monitoring: Offers the capacity to monitor equipment from any location, improving the flexibility and responsiveness of maintenance teams.