Real-time Equipment Condition Monitoring Systems


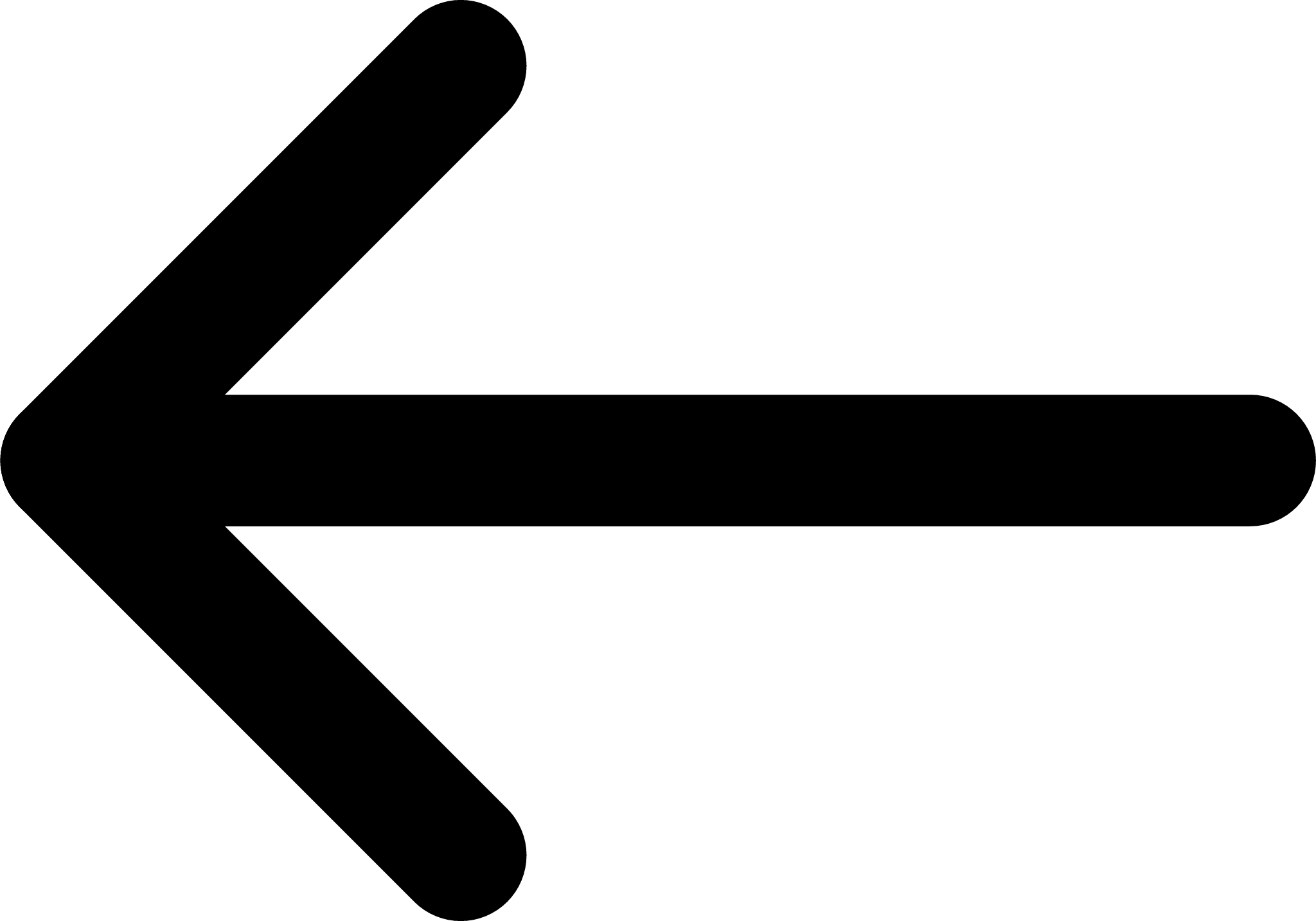
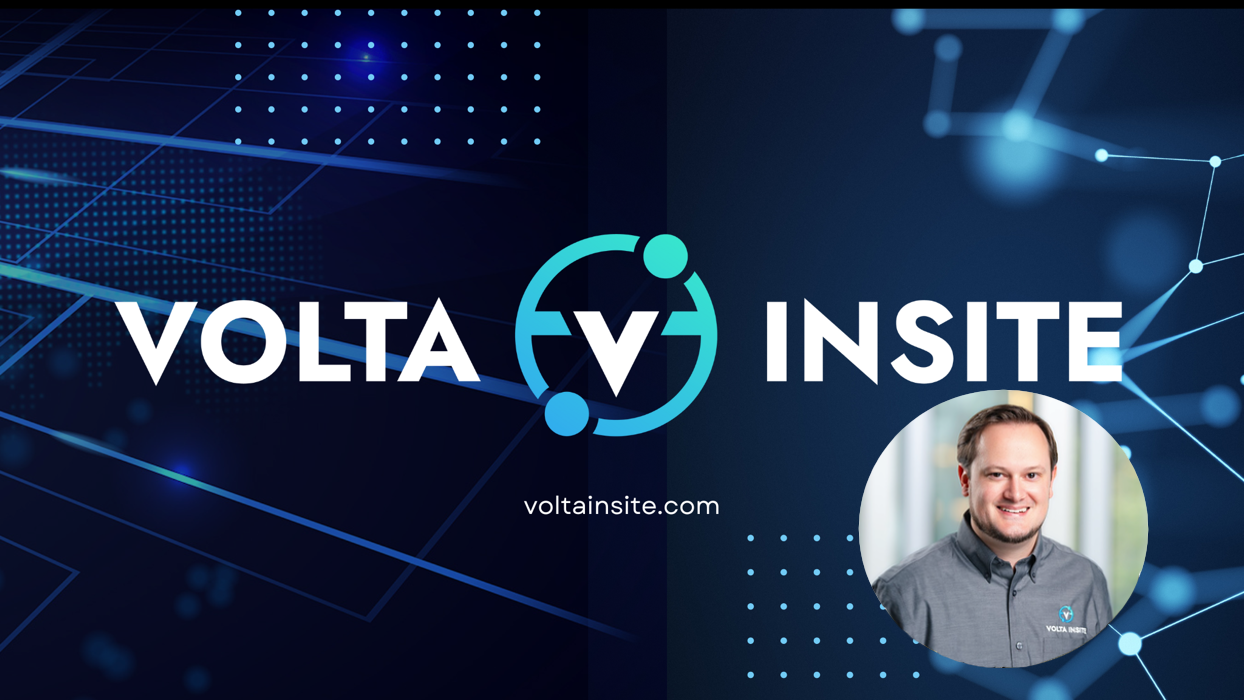
Equipment monitoring is a critical aspect of modern manufacturing and production environments. It's about keeping an eye on your machinery and making sure everything runs as it should, without any nasty surprises.
What Is Equipment Monitoring?
At its core, equipment monitoring involves the use of sensors to collect data on various parameters such as temperature, vibration, and power. This data offers insights into the health of machines and can alert maintenance crews to potential issues before they lead to equipment failure. Remote monitoring solutions extend these capabilities, allowing for the tracking of performance metrics in real-time from anywhere, providing a foundation for action that can significantly reduce downtime and save on maintenance costs.
The elements of an effective equipment monitoring system include sensor-based measuring, automated alerting, real-time tracking, and detailed analysis. These systems often feature ruggedized battery-powered trackers for unpowered equipment and customizable software for machine assets, ensuring that from the shop floor to remote job sites, every piece of equipment is under surveillance for optimal operation and uptime.
Benefits of Equipment Monitoring Systems
Whether it's managing a fleet of construction equipment or ensuring the manufacturing floor runs without interruption, equipment monitoring systems offer a cost-effective solution for maintaining machine health and production quality.
Saves Time and Reduces Downtime
Equipment monitoring systems streamline the identification of potential issues, enabling quick and efficient resolution before downtime occurs. This reduces the time spent on troubleshooting and maintenance tasks, allowing teams to focus their efforts on production rather than repairs. By having constant, automated oversight, predictive alerts can be set up to catch anomalies early, leading to swift, preemptive action, and thus safeguarding against lengthy periods of inactivity.
Ensures Product Quality and Streamlining Processes
A steadfast monitoring system acts as a safeguard for product quality, as machines running at peak condition produce consistent, high-quality outcomes. The system's ability to monitor machine performance and condition in real-time ensures that any deviation from the norm can be addressed immediately, reducing the chance of quality lapses. Furthermore, by systematically capturing data and trends, these solutions can highlight areas for process optimization, enhancing overall workflow efficiency.
Lowers Operating Costs
An investment in equipment monitoring is justified through the substantial reduction in operating costs it brings. By avoiding unscheduled downtime and extending the lifespan of machinery via proactive maintenance, it maximizes asset utilization and performance, reducing the need for frequent replacements or repairs. Over time, the savings from these efficiencies surpass the initial investment, delivering a favorable return on investment.
Key Components of Equipment Monitoring
The key to effective predictive maintenance lies in the proper implementation of various equipment monitoring components. These components work in unison to collect, analyze, and present critical data, paving the way for proactive maintenance that can prevent unexpected equipment failures and reduce downtime.
Sensors and Their Role in Data Acquisition
Sensors are the primary tools in equipment monitoring, serving as the frontline gatherers of data. They measure critical parameters like vibration, temperature, and energy consumption, passing this information onto the system for analysis. Each sensor is tuned to detect specific kinds of network events or machine assets, ensuring that every nuance of equipment performance is captured with precision.
End-to-End System of Wireless Sensors and Gateways
A seamless network of wireless sensors and gateways forms the infrastructure of a modern monitoring system. This configuration allows for scalable and flexible deployment across various equipment types and industries. The gateways transmit sensor data to a central control platform, enabling real-time visibility and analytics across the entire operation, without the constraints of traditional wired systems.
Signal Processing in Equipment Monitoring
Once data is captured by sensors, it undergoes signal processing to filter noise and extract actionable information. This can involve advanced algorithms and analytics, often carried out by cloud-based software. It's through this processing that raw data is transformed into insights, indicating the health and performance of machines, allowing for prompt action when anomalies are detected.
Operation Screens and User Interfaces
For any monitoring system to be effective, it must present its findings clearly and intuitively. This is where operation screens and user interfaces come into play. These elements need to be designed with the end-users—such as plant managers and maintenance workers—in mind, allowing them to access and interpret data easily. A good interface will streamline the workflow, making it simple to navigate menus, interpret diagnostics, and visualize trends.
The Technological Backbone of Equipment Monitoring
Advanced Analytics and Machine Learning in Equipment Monitoring
Advancements in analytics and machine learning serve as the backbone of modern equipment monitoring systems. These technologies process large volumes of data to identify patterns, predict outcomes, and optimize machine performance. By leveraging machine learning, the systems evolve continuously, improving their diagnostic capabilities and becoming more adept at forecasting potential issues, enabling proactive maintenance and further reducing unplanned downtime.
In the context of advancing equipment monitoring through technology, the case study "Equipment Monitoring System with use of Digital Twins and Internet of Things: Algorithms, Architecting and Experiments " by Yaroslav Abarnikov, Vyacheslav Kharchenko, and Olga Morozova offers a compelling illustration. This research demonstrates the practical application of Digital Twins and IoT technologies in creating a real-time, energy-efficient monitoring system. The authors proposed and described innovative algorithms for integrating various gateways, underscoring the importance of cloud-based solutions in addressing the challenges of equipment energy performance monitoring (Abarnikov, Kharchenko, & Morozova).
Real-Time Visibility Through Enterprise Asset Optimization Software
Enterprise Asset Optimization software provides real-time visibility into every aspect of machine and equipment performance. Such platforms aggregate data from various sources, delivering comprehensive insights that enable swift responses to emerging issues. By centralizing this information, stakeholders can view the entire operation's health at a glance, facilitating smart, informed decisions that enhance productivity and reduce costs.
Implementing Equipment Monitoring Systems
Navigating the complexity of modern industrial operations requires a robust equipment monitoring system. This system should not only be technologically advanced, but also customizable, scalable, and flexible to align with the unique requirements and operational goals of an organization. This section will guide you through the critical aspects of implementing such systems.
When to Opt for a Custom Equipment Monitoring System
A custom equipment monitoring system becomes a necessity when standard solutions do not align with the unique requirements of an organization's processes or specific types of machinery. Custom systems offer the benefit of tailored sensor selection, data analytics, and user interfaces, ensuring the capture and utilization of data is precise to the operational needs and goals. They become especially relevant in highly specialized industries where precision and customization can significantly impact performance and outcomes.
Success Factors for an Effective Implementation
Key factors for a successful implementation of an equipment monitoring system include a clear understanding of the desired outcomes, involvement of stakeholders, and ensuring the system's interoperability with existing equipment and networks. Proper training for end-users and a phased deployment strategy can also play a substantial role in easing the transition and maximizing the system's effectiveness. Additionally, ongoing support and system updates are crucial in keeping the system reliable and relevant over time.
Flexible Deployment Options for Varied Organizational Needs
Flexible deployment is another cornerstone for successful equipment monitoring system implementation. Such flexibility accommodates the scale of operation, geographic spread of machinery, and differing technological infrastructures across organizations. Whether it’s on-premise, cloud-based, or a hybrid approach, the deployment method should allow for seamless integration, scalability, and secure data access to meet the varied needs of organizations.
Identifying Critical Assets for Monitoring in Your Facility
Identifying which assets to monitor is pivotal in maximizing the effectiveness of an equipment monitoring system. Critical assets often include those that have a high impact on production continuity, are costly to repair or replace, carry a risk of failure, or have a history of reliability issues. Assets that are essential for safety and compliance are also high on the priority list. By focusing on these key assets, a facility can ensure its monitoring efforts result in the greatest increase in reliability and cost savings. Each facility may determine its critical assets differently, but the goal is consistent: to safeguard the most crucial elements of operations.
Key Takeaways
-
Equipment monitoring systems are vital for maintaining optimal operation, ensuring quality, and preventing downtime through real-time data and predictive analytics.
-
Implementing such systems requires a focus on integration with existing enterprise frameworks, enabling comprehensive visibility and data-driven decision-making.
-
Customizable and scalable solutions are critical for meeting the unique needs of various industries and facilitating the proactive management of machinery.
-
Predictive maintenance and real-time monitoring play crucial roles in prolonging asset lifespan and protecting investments from unexpected failures.
-
Compliance with industry regulations and standards is streamlined with the accurate and timely equipment data provided by monitoring systems, simplifying audits and compliance processes.
FAQs of Equipment Monitoring Systems
What Makes a Machine Monitoring System Important for Operational Efficiency?
A machine monitoring system is key to operational efficiency because it offers real-time data allowing for informed decisions that optimize asset use and reduce waste. For example, data on machine utilization patterns can streamline workflows, resulting in a 20% uptick in production rates and decreasing idle times by 15%. Such systems also aid in predictive maintenance, preventing costly breakdowns and keeping machines running at their most efficient levels.
How Does Equipment Monitoring Contribute to Avoiding Unplanned Downtime?
Equipment monitoring systems directly contribute to avoiding unplanned downtime by providing early warnings via alerts when they detect potential equipment failures. This advance notice enables maintenance crews to address issues before they escalate. Statistics show that implementing such systems can reduce equipment breakdowns by up to 70% and increase machine life by 30% through effective maintenance strategies.
What Are the Key Considerations When Choosing an Equipment Monitoring System?
When choosing an equipment monitoring system, key considerations include compatibility with existing infrastructure, scalability for future requirements, real-time data capabilities, ease of use, and the system's ability to integrate with other enterprise management tools. Another critical aspect is the system's support for predictive maintenance, which data suggests can lead to a 25% reduction in repair costs and a 45% increase in machine availability.