Advanced Condition Monitoring Solutions


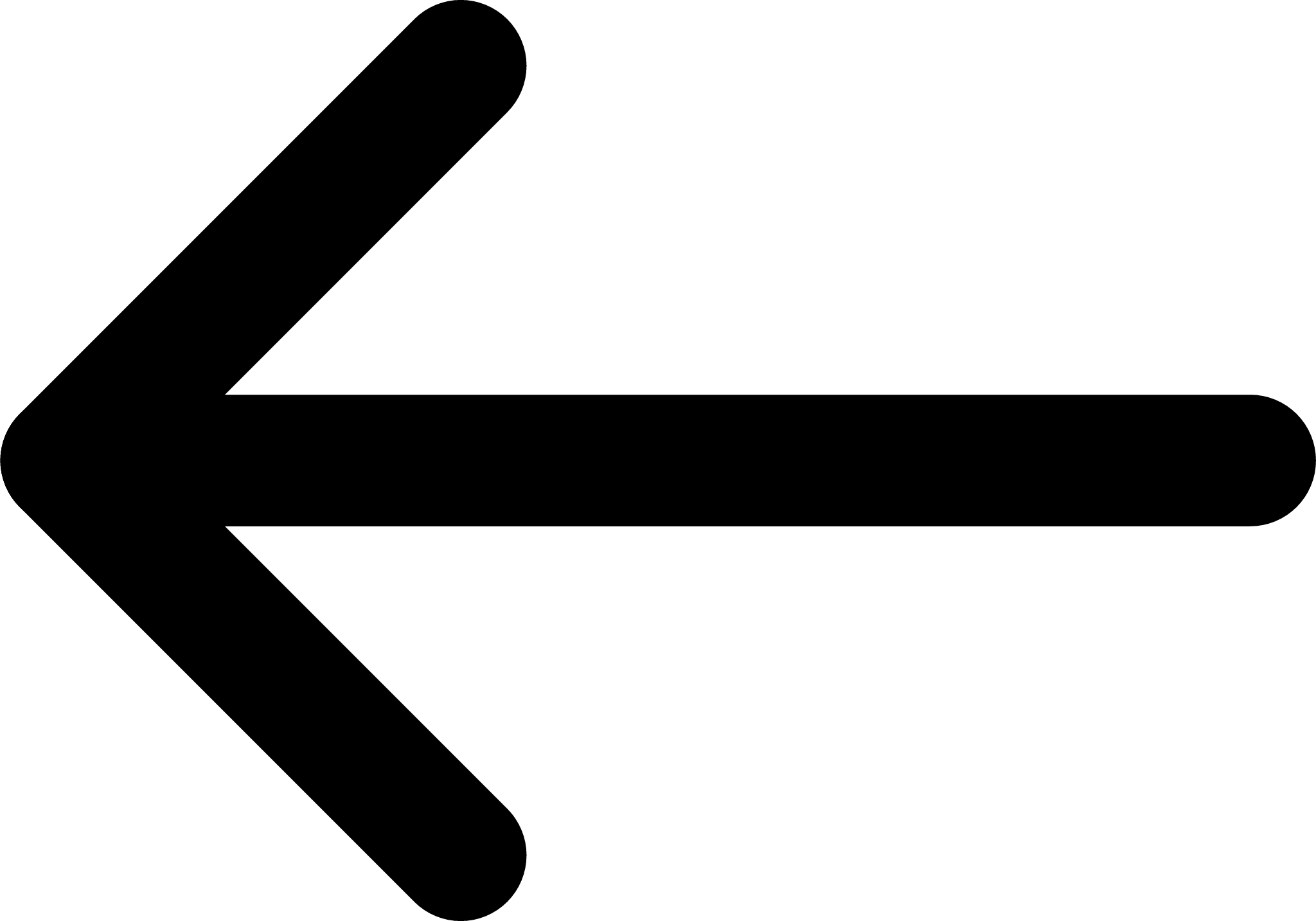
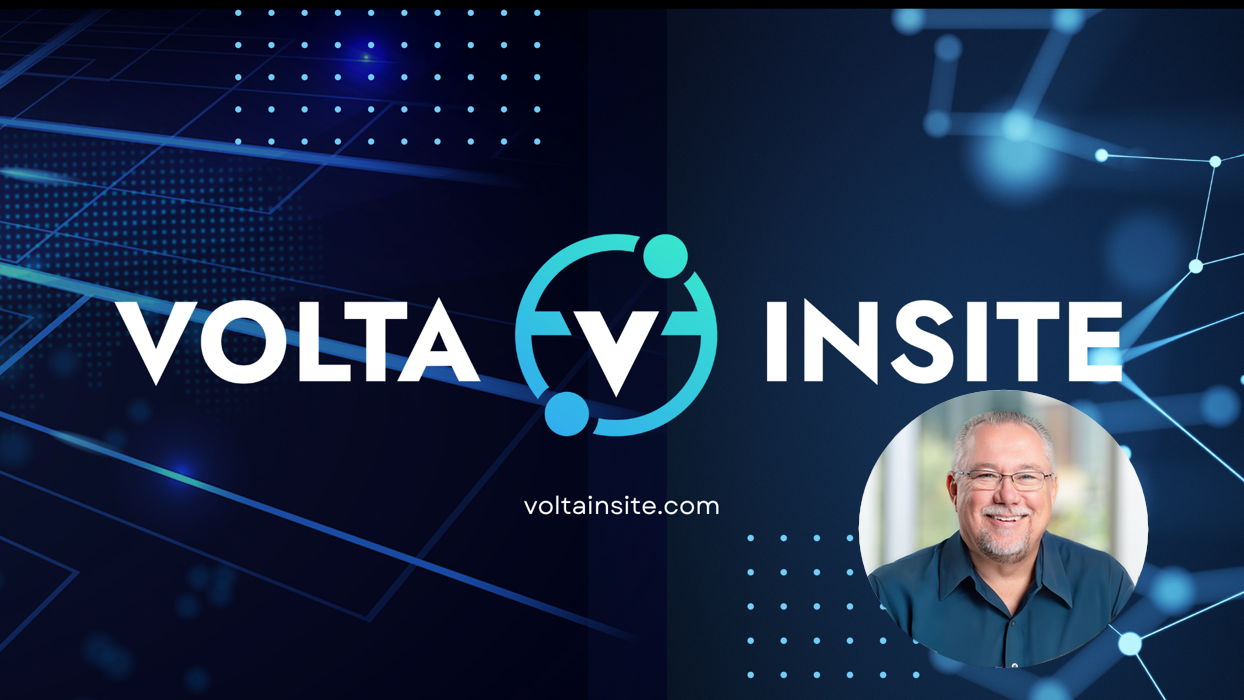
What Are Condition Monitoring Solutions?
Condition monitoring solutions are pivotal for maintenance planning. This approach involves continuously scrutinizing the state of equipment during operation. By harnessing technology like smart systems and various sensors, condition monitoring identifies impending failures before they can cause unplanned downtime.
At the heart of these solutions is a suite of technologies. Sensors such as temperature sensors, vibration detectors, and pressure measurement devices feed data into sophisticated software solutions. This software performs in-depth analysis, identifies historical trends, and flags anomalies. Frequent companions to these technologies are Distributed Control Systems (DCS), which help to maintain optimal machinery operation.
Key Components in a Condition Monitoring System
Integrating the right components into a condition monitoring system ensures precise and timely insights. This leads to a robust predictive maintenance program capable of detecting even the slightest abnormalities.
Sensors and Data Acquisition Devices: At the heart of any condition monitoring system are the sensors and data acquisition devices. These components are responsible for collecting data on various parameters, such as vibration, temperature, pressure, and more. High-fidelity sensors capture a wide spectrum of data from equipment, enabling detailed analysis of machine health.
Data Processing and Analytics: Once data is collected, it needs to be processed and analyzed to extract meaningful insights. This is where advanced analytics come into play. Algorithms and machine learning models analyze the data to identify patterns, trends, and anomalies that may indicate equipment issues. This component is crucial for transforming raw data into actionable intelligence.
Diagnostic and Predictive Algorithms: Core to a condition monitoring system are the diagnostic and predictive algorithms that analyze sensor data to detect anomalies and predict potential failures. These algorithms use historical and real-time data to provide maintenance teams with alerts and recommendations for preemptive actions.
Communication Systems and Integration Capabilities: For a condition monitoring system to be effective, it must seamlessly integrate with existing infrastructure and communicate efficiently with other systems. This includes the ability to quickly configure and link with Enterprise Asset Management (EAM) systems, maintenance management systems, and other operational technology. Effective communication systems ensure that data and insights are readily available to decision-makers.
User Interface and Reporting Tools: The user interface and reporting tools are critical for interpreting the data and making informed decisions. A well-designed interface provides easy access to key metrics, trends, and alerts, while comprehensive reporting tools offer detailed insights into equipment health, performance, and maintenance needs. These components help maintenance teams plan routine maintenance, avoid unexpected downtime, and optimize operational efficiency.
Scalability and Flexibility: A condition monitoring system must be scalable and flexible to adapt to changing needs and environments. It should support a range of sensors and devices, offer customizable analytics, and allow for expansion to monitor additional machinery or parameters as required.
By focusing on these key components, a condition monitoring system can provide a strategic advantage in managing the health and performance of machinery and equipment. It enables proactive maintenance practices, reduces the risk of unplanned downtime, and supports operational efficiency across various industrial settings.
Advantages of Implementing Condition Based Monitoring Solutions
Embracing Condition-Based Monitoring (CBM) translates into a multitude of advantages for industrial operations. This smart approach to maintenance sharpens the focus on living equipment data, leading to more deliberate and effective management.
More Efficient Maintenance: CBM transforms maintenance from a calendar-dictated guessing game to maintenance based on actual needs, guided by clear indicators of equipment health. Schedules are optimized, leading to fewer interruptions in production and better allocation of human resources. Data-directed maintenance actions can prevent small issues from turning into costly, large-scale repairs.
Improved Safety: Proactive fault detection reduces the risk of hazardous incidents in the workplace. Safety compliance improves as equipment operates within safer parameters, ensuring fewer breaches in protocols. Maintenance work can be planned for and carried out under controlled conditions, rather than in response to a failure.
Improved Asset Efficiencies: The health and performance of assets are tracked over time, giving a clear picture of their efficiency and the impact of maintenance interventions. Asset life cycles are prolonged through timely maintenance, ensuring a better return on investment. Performance data allows for fine-tuning operations, increasing the overall efficiency of assets. Unanticipated downtime diminishes, keeping productivity levels consistent and predictable.
Strategies for Optimizing Condition Monitoring
Discovering the most effective way to utilize condition monitoring involves a strategic and structured approach. Staying ahead involves both, setting up a solid foundation and employing advanced techniques to leverage the collected data for the best outcomes.
5 Steps to Condition Monitoring
Optimizing condition monitoring can be simplified into five pivotal steps. Each step aims to further refine the process, ensuring that every action taken is targeted and efficient:
-
Establish a clear baseline of equipment performance for comparison.
-
Set up sensors and data acquisition correctly to capture relevant and accurate data.
-
Integrate analytics software capable of deciphering data into practical insights.
-
Create an alert system that notifies the appropriate personnel of identified anomalies.
-
Schedule regular reviews of the system and add the alerts to ensure adaptability with changing conditions.
Condition Monitoring Solutions Across Industries
While condition monitoring finds its roots in manufacturing, its application stretches across a variety of industries. Each sector can tailor this technology to suit unique operating environments and craft safeguards against their specific failure modes.
Condition Monitoring for Manufacturing
Manufacturing thrives on uptime, making condition monitoring a key player in this space. With an intricate orchestration of machinery, detecting the early signs of wear and mechanical stress keeps production lines running.
-
Automated systems can track the performance of critical production machines in real-time.
-
Smart sensors can provide data for predictive maintenance, foreseeing issues before they halt operations.
-
Maintaining consistency in product quality is another essential benefit, as equipment deviations can immediately signal potential quality faults.
Condition Monitoring for Non-Manufacturing
Beyond the factory floors, condition monitoring penetrates into realms like healthcare, where equipment reliability is paramount. Power plants, transport systems, and smart buildings also rely on this technology.
-
In healthcare, for instance, patient safety hinges on the proper function of life-sustaining machines, making condition monitoring crucial.
-
Power plants use condition monitoring to predict and prevent outages, ensuring a steady supply of energy.
-
Integrating condition monitoring into smart building operations enhances energy efficiency and sustainability.
Deployment Challenges in Different Environments
Implementing condition monitoring in varying industries isn't always straightforward. The challenges often lie in the complexity of systems and finding the right balance between technology, cost, and utility.
-
Harsh industrial settings may require sturdier sensors and customized solutions to withstand extreme conditions.
-
Cost considerations can impede widespread sensor deployment, especially in industries with low profit margins.
-
Diverse environments necessitate varied approaches making one-size-fits-all solutions ineffective.
Leveraging Modern Technologies for Enhanced Condition Monitoring
As industries evolve, modern technologies seamlessly blend into condition monitoring systems. Machine learning algorithms and Internet of Things (IoT) devices are reshaping the landscape, offering deeper insights and more expansive data collection capabilities.
Machine Learning for Equipment Health
Machine learning algorithms are adept at pattern recognition, sifting through large datasets to predict potential failures. This intelligence becomes critical in anticipating maintenance needs and extending the lifespan of machinery.
-
Learning from historical data, these algorithms improve over time, increasing their predictive accuracy.
-
They can manage and interpret data from multiple sources to give a holistic view of equipment health.
-
Adoption of machine learning enhances decision-making, allowing for more nuanced and timely interventions.
Efficient and Scalable IoT Condition Monitoring
IoT devices are revolutionizing condition monitoring by expanding data collection points and enhancing real-time communication capabilities. Their efficiency and scalability are key to upgrading traditional systems to smarter, interconnected networks.
-
IoT sensors can be placed in remote or hard-to-reach areas, broadening the scope of condition monitoring.
-
The scalable nature of IoT-based systems means they can grow with the facility, adding sensors as needed without significant reconfiguration.
-
They facilitate the collection of real-time data that is essential for the timely reaction to equipment health issues.
Connectivity With OPC UA
Open Platform Communications Unified Architecture (OPC UA) is a communication protocol that allows various industrial equipment to 'talk' to one another. It's integral for achieving the interconnectivity that modern condition monitoring systems require.
-
OPC UA enables secure data exchange among devices from different manufacturers, breaking down proprietary barriers.
-
It supports complex data types and elaborate information models necessary for detailed condition monitoring.
-
With OPC UA, systems can become truly intelligent, enabling predictive maintenance to become more proactive than ever.
Integration and Compatibility Issues
As with any sophisticated technology, condition monitoring systems face challenges related to integration and compatibility. It's crucial to address these hurdles when designing a system that must fit into an existing industrial landscape.
Online & Permanent Systems
Online and permanent monitoring systems are at the core of 24/7 operation. However, integrating them with legacy systems can be problematic.
-
Selecting a system that is flexible and compatible with current machinery is essential to avoid costly equipment changes.
-
The complexity of permanent systems often requires professional installation and calibration to ensure accurate data collection.
-
Seamless data flow between online systems and monitoring software is vital to prevent lapses in data collection that could miss critical alerts.
Integration Into 3rd-party Enterprise Software
Linking condition monitoring systems with third-party enterprise software can allow for a more comprehensive approach to asset management.
-
Data transparency is necessary across different platforms; therefore, ensuring compatible data formats and interfaces is a key concern.
-
Merging condition monitoring data with other business systems, such as ERP, can support more strategic, data-driven decision-making.
-
Potential software conflicts may arise, requiring dedicated support teams to ensure smooth operation and integration.
Industrial Communication Protocols
The variety of industrial communication protocols can make or break the integration of condition monitoring systems.
-
Adherence to universally adopted protocols, such as Modbus or Profibus, can foster easier integration with existing industrial controls.
-
Upgrading legacy systems to communicate with modern protocols may require additional investment but is often a necessary step for integration.
-
Ensuring cybersecurity within these protocols is also a pressing issue, as more devices connect and communicate over the network.
Tools and Software for Effective Condition Monitoring
Selecting the right tools and software is crucial for designing an effective condition monitoring system. The choice impacts not only data quality but also how insights are derived and acted upon.
Condition Monitoring Service & Expertise
Recruiting a condition monitoring service that matches a company’s needs can drastically improve outcomes. These services provide not just tools but also specialized expertise.
-
Experienced professionals can tailor monitoring strategies to match specific industry challenges.
-
Condition monitoring services usually keep abreast of the latest technologies and will have advanced tools and deep knowledge on hand.
-
Beyond the hardware, they offer insights into the data, making sense of complex signals and patterns.
Condition Monitoring Software
Software is the linchpin in the condition monitoring system, processing countless data points to detect anomalies and patterns.
-
It must be robust enough to handle large volumes of data while remaining user-friendly for those interpreting the results.
-
Integrating with existing systems across the facility ensures a streamlined workflow.
-
The right software can predict trends, transforming raw data into actionable maintenance strategies.
Continuous and Run-up / Coast-down Monitoring
Two types of toolsets are integral for monitoring: one for continuous operation and another specialized for transitional phases like run-up or coast-down.
-
Continuous monitoring tools keep an eye on the equipment during normal operation, catching issues as they develop in real-time.
-
Run-up and coast-down tools focus on the transitory periods that can stress equipment, often revealing issues not apparent during steady-state operation.
-
By balancing both methodologies, maintenance teams can achieve a comprehensive understanding of equipment health across all operational conditions.
Key Takeaways
-
Condition monitoring is pivotal to predictive maintenance, transforming maintenance planning from reactive to proactive and preventing costly unplanned downtime.
-
Vibrational analysis, oil analysis, thermography, and motor circuit analysis are advanced techniques that offer deep insights into machine health, predicting faults before they lead to failures.
-
Industries beyond manufacturing, such as healthcare and smart buildings, are increasingly benefiting from condition monitoring to secure equipment reliability and safety.
-
Leveraging modern technologies like machine learning, IoT, and communication protocols like OPC UA significantly enhances the predictive capabilities of condition monitoring systems.
-
While integrating condition monitoring systems presents challenges, careful compatibility and protocol consideration can facilitate a smooth transition from legacy systems.
-
Sound decision-making hinges on the effective use of condition monitoring tools and software, which should integrate continuous data acquisition and provide actionable insights for maintenance interventions.
FAQs for Condition Monitoring Solutions
What Is the Difference Between Online and Offline Condition Monitoring?
Online monitoring is a continuous, real-time process where data is consistently gathered while machinery runs. Offline monitoring occurs intermittently, perhaps during maintenance checks or at scheduled intervals.
-
Online monitoring offers immediate insights and alerts, ideal for critical equipment that operates constantly.
-
Offline monitoring serves as a snapshot, beneficial for less critical or intermittently used machinery.
-
The choice between the two often depends on cost, criticality, and operational continuity needs.
How Can Condition Monitoring Contribute to a Plant's ROI?
Condition monitoring can significantly increase a plant's return on investment (ROI) by enhancing equipment lifespan and performance, reducing maintenance costs, and avoiding expensive downtime.
-
Avoiding just one significant failure can save substantial amounts of money, potentially covering the cost of the entire monitoring system.
-
Improved equipment efficiency and reduced energy consumption are secondary benefits that contribute to ROI.
-
Data-driven maintenance scheduling helps in allocating resources more effectively, avoiding unnecessary servicing or downtime.
What Are the Common Misconceptions About Condition Monitoring?
There are several misconceptions about condition monitoring that can dilute its perceived value.
-
Misconception 1: It's too expensive. While upfront costs can be significant, the long-term savings often outweigh the initial investment.
-
Misconception 2: It's only useful for certain industries. In reality, any industry that relies on machinery can find value in condition monitoring.
-
Misconception 3: It can entirely replace human inspections. While condition monitoring can significantly reduce the need for manual checks, it complements rather than replaces human expertise.
Condition monitoring is an effective tool that, when understood and utilized correctly, can be a game-changer for industrial operations, offering improved safety, efficiency, and financial benefits.