Condition-Based Maintenance Explained: A Data-Driven Approach


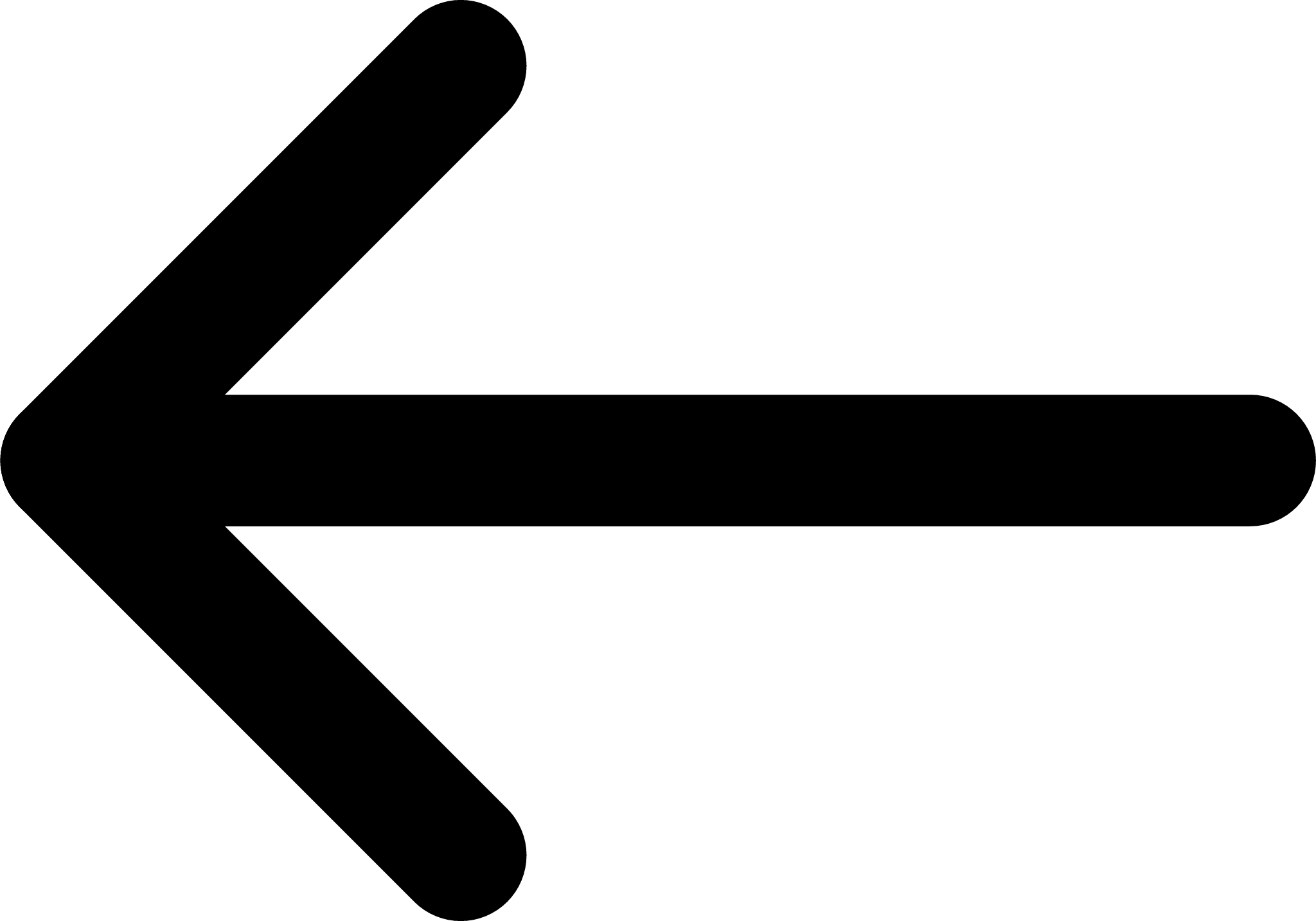
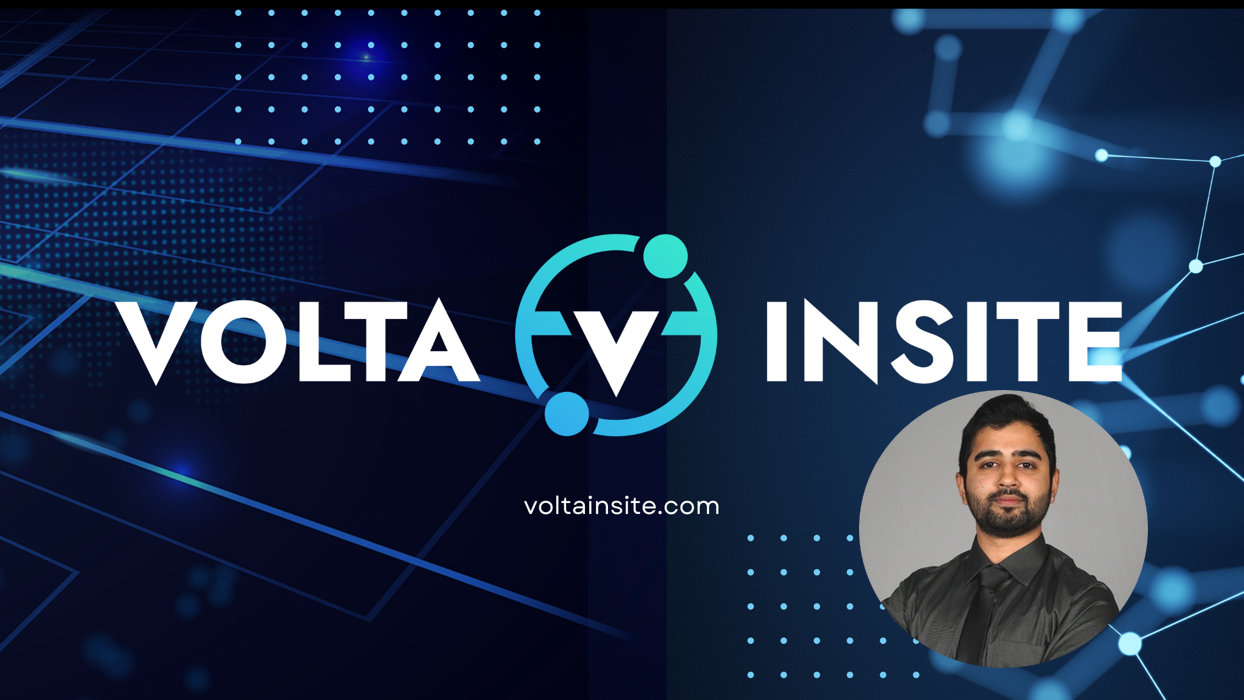
In the complex world of industrial maintenance, a shift is occurring. This shift moves us from reactive strategies, which often involve costly emergency repairs, to proactive ones that promise increased reliability and substantial cost savings. At the heart of this shift is Condition-Based Maintenance (CBM), an approach that is redefining how facilities manage and maintain their critical production assets.
What Is Condition-Based Maintenance?
Condition-Based Maintenance (CBM) is a savvy maintenance strategy predicated on monitoring the actual condition of assets to decide on the most opportune moment for maintenance actions. It's the art of predicting problems before they become expensive repairs. In essence, maintenance teams use sensors to collect real-time or periodic measurements, like vibration levels, temperature, and pressure, to track the health of equipment.
With CBM, machinery tells you its needs. Instead of sticking to a schedule or waiting for a machine to break down, maintenance personnel inspect, monitor, and maintain equipment aligning actions to the machine's condition. The result? A harmonious balance of optimum performance and minimal disruption.
Differences Between Condition-Based Maintenance, Predictive, and Preventive Maintenance
While CBM focuses on real-time conditions, predictive maintenance hinges on using historical and real-time data to predict future failures. Patterns are analyzed, often with advanced data analysis techniques like machine learning algorithms, to foresee potential issues. Unlike CBM, which alerts maintenance staff immediately about issues, predictive strategies plot out when a component might fail in the future.
Preventive maintenance is the old-school method—think of it as maintenance by the calendar. It's work done based on time or usage, like a dentist's appointment every six months. These actions occur whether the machine needs it or not, running the risk of unnecessary maintenance or, conversely, not catching issues before they bloom into major problems.
Goals Behind Adopting CBM in Industry
The CBM philosophy is mission-critical in modern industry. It tailors maintenance activities to the specific signals of distress a machine exhibits. This bespoke approach aims to:
-
Predict and prevent complete equipment failures.
-
Enhance equipment reliability and sustainment.
-
Optimize resources and save on maintenance costs.
-
Improve safety by reducing the risk of machinery mishaps.
-
Extend the life and performance of assets.
By adopting a CBM program, companies leverage the power of condition-monitoring techniques to keep their assets in optimal health, proactively addressing possible failure modes and optimizing maintenance operations for better efficiency and cost savings.
How Condition-Based Maintenance Enhances System Reliability and Cost Savings
Condition-Based Maintenance excels in keeping systems reliable. It transforms maintenance from a cost center to a value-added activity, optimizing maintenance effectiveness and costs. Vibration analysis, temperature scans, and pressure checks are collection techniques ensuring that every dollar spent on maintenance is a dollar towards preventing unplanned downtime.
Through real-time alerts and deep analysis, a CBM program can help maintenance personnel to:
-
Diagnose and evaluate the severity of a condition before it escalates.
-
Plan maintenance activities to reduce downtime.
-
Integrate CBM data with enterprise asset management systems for better decision-making.
-
Schedule maintenance to avoid interrupting production, thereby saving time and money.
Ultimately, CBM empowers organizations to make informed decisions about maintenance actions, enabling a proactive approach that offers clear advantages in reliability and financial efficiency. It's an investment in technology, expertise, and processes that pay off handsomely by preserving assets and ensuring they are maintained only when necessary, thus dodging the bullet of unexpected equipment drama that hampers operations and punctures budgets.
Advantages and Disadvantages of Condition-Based Maintenance
The path to effective asset management is nuanced, with every method bringing a blend of strengths and limitations. Condition-based maintenance vigilantly monitors the heartbeat of machinery, attacking two of the biggest enemies in production: risk and downtime. Here’s how CBM stands guard:
-
Pros:
-
Optimized Maintenance Scheduling: Maintenance only when necessary, not by arbitrary dates.
-
Prolonged Equipment Lifetime: Regular monitoring can translate to fewer stressors on equipment, lengthening lifespan.
-
Cost-Effectiveness: While initial costs may be higher, the focus on actionable data typically leads to overall savings.
-
-
Cons:
-
Complexity: The intricate dance of sensors, data, and analysis can be overwhelming.
-
Initial Investment: Upfront costs for sophisticated monitoring tools and training staff may stretch budgets.
-
Maintenance Skillset: Requires a team with the technical know-how to interpret data and take proper action.
-
While CBM enables a well-oiled machine of industry, it demands attention, resources, and strategic planning to thrive. Addressing these with a carefully tailored maintenance strategy paves the way for reaping the benefits of this advanced approach.
Implementing Condition-Based Maintenance
Embarking on the journey of implementing Condition-Based Maintenance requires strategy and precision. Each step, taken with forethought and expertise, can lead to a harmonious confluence of cost savings and enhanced equipment reliability. Here are the critical milestones for a successful CBM journey.
The compass for CBM implementation is a criticality assessment, which steers the course of action. It gauges the importance of individual assets to overall production, focusing resources where they matter the most:
-
Prioritize based on impact: Select assets based on their role in production and the magnitude of distress their downtime would cause.
-
Rank and categorize: Assign a criticality rank to guide maintenance efforts effectively.
-
Assess and reassess: Periodically revisit the assessment to align with changes in production or asset lineup.
Choosing the Right Condition Monitoring Equipment and Software
The hardware and software chosen are the scouts and interpreters in the CBM domain:
-
Select versatile, robust equipment: Opt for monitoring tools designed for the harsh realities of industrial environments.
-
Platform agility: Choose software that offers seamless integration with existing systems and the flexibility to scale.
-
User-centric design: Ensure the system is intuitive, allowing maintenance personnel to act swiftly and decisively on its revelations.
Implementing CBM requires a calculated blend of critical assessments, predictive intelligence, relentless data collection, and sophisticated yet user-friendly technology. With these components harmonized, the CBM symphony can reach its crescendo, creating a proactive maintenance environment that sings with efficiency.
Building a Successful Condition-Based Maintenance Plan
Stitching together a successful Condition-Based Maintenance (CBM) plan is akin to charting a map through uncharted machinery malfunctions – it's about creating a detailed guide that marries business goals with the technical language of equipment health. Logic and foresight become the co-pilots on this journey.
A CBM plan is not merely an assembly of maintenance tasks; it's a strategic framework molded to fit the curves of an organization:
-
Start with the end in mind: Define the business objectives, such as reducing downtimes or extending asset lifespan, and let them guide your CBM strategy.
-
Inventory resources: Assess both the tools at hand and the training needs of your staff to ensure you can fully leverage CBM's capabilities.
-
Adapt and scale: Enable the plan to grow and flex with business changes, ensuring it stays harmonized with evolving operational priorities.
Successfully navigating the maze of challenges associated with CBM and building a robust plan is a testament to an organization's commitment to embracing proactive maintenance strategies. When done right, the benefits extend from the factory floor to the bottom line, epitomizing the synergy between diligent planning and operational acumen.
Software and Tools That Enable Effective Condition-Based Maintenance
The backbone of Condition-Based Maintenance lies in its ability to harness the right tools and software. These digital armaments are vital, providing the clarity and foresight to steer maintenance operations clear of guesswork and towards data-driven precision.
Evaluating CBM Software: Key Features and Selection Criteria
When scouting for CBM software, your selection process should focus on these criteria:
-
Real-time data processing: Seek platforms that deliver immediate insights, allowing for swift action.
-
Customization: The best CBM software adapts to your specific industrial context and objectives.
-
User-friendly interface: Complex data needs to be user-accessible; simplicity in design is crucial.
-
Integration capacity: Ensure it can dovetail with existing systems to streamline processes.
-
Support and training: A vendor invested in your success will provide training and robust support.
Empowering Maintenance Teams With Advanced Analytics and Predictive Tools
Armed with advanced analytics and predictive tools, maintenance teams transform into proactive forces:
-
Predictive analytics convert data into predictive forecasts, spotlighting troublesome trends.
-
Machine learning elevates maintenance from reactive to predictive by learning from each maintenance event.
-
Dashboard visualizations empower teams to grasp complex data at a glance, fostering informed decision-making.
The Integration of CMMS Software in Condition-Based Maintenance
Computerized Maintenance Management System (CMMS) software is the keystone in the arch of CBM:
-
It acts as the central repository, recording and tracking every inspection, maintenance activity, and outcome.
-
Integration with CBM systems creates a feedback loop, wherein data collected helps refine maintenance schedules in the CMMS.
-
The synergy between CMMS and CBM tools lays the groundwork for an upkeep ecosystem that is both resilient and adaptive.
Embracing the right software and tools can catalyze a Condition-Based Maintenance program from a concept to a concrete, cost-saving reality. It's not just a choice; it's an elevation of the maintenance paradigm to its most intelligent and perceptive form.
The Role of Personnel in Transitioning to a Condition-Based Maintenance Strategy
For a condition-based maintenance strategy to breathe and thrive, it demands more than tools—it requires the touch of adept personnel. These individuals are the life force driving the strategy forward, interpreting data, and turning insights into action. Understanding their role underscores the human element in technological triumphs.
Cultivating the Right Organizational Culture for CBM Success
The transition to CBM is not just a mechanical shift but a cultural revolution within an organization:
-
Encourage curiosity and continuous learning, as CBM is an ongoing voyage of discovery.
-
Foster open communication, where maintenance teams can share insights and developments.
-
Emphasize adaptability, as CBM requires a nimble mindset that can manage change effectively.
-
Reward innovation, recognizing those who contribute to CBM success with effective solutions and improvements.
Training and Support for Maintenance Teams Embracing CBM
The pivot to CBM is a shared journey:
-
Provide thorough training on the CBM tools and software, ensuring teams feel confident and equipped.
-
Offer continuous support, both from internal leaders and external vendors, to address challenges as they arise.
-
Create a knowledge-sharing environment where personnel can exchange experiences and best practices.
-
Develop a comprehensive onboarding process for new hires to align them quickly with the CBM methodologies in use.
By investing in their personnel, organizations not only enhance the efficacy of their CBM strategy but also underscore their commitment to the well-being and development of their team. It illustrates a clear understanding that behind every successful maintenance operation, there's a skilled, informed, and motivated crew steering the ship.
Real-World Applications of Condition-Based Maintenance
The principles of Condition-Based Maintenance (CBM) are best illustrated not in theory, but through practical application. Its success stories are diverse, spreading across various sectors from precision-demanding pharmaceuticals to heavy-duty manufacturing, each offering a different facet of CBM's versatility and effectiveness.
Impact of CBM on Single- and Multi-Component Systems
CBM plays a distinct role, whether in isolated equipment or complex, interconnected systems:
-
Single-component applications, such as a standalone conveyor belt, benefit from focused monitoring of wear elements, extending their lifespans significantly.
-
In multi-component systems like HVAC, CBM ensures that a fault in one unit doesn't cascade into a system-wide breakdown, maintaining operational harmony and efficiency.
Insights from Industries: How Different Sectors Utilize CBM
CBM's adaptability allows it to morph to the needs of diverse industries:
-
In energy generation, CBM's predictive power prevents costly interruptions, with pressure sensors forecasting turbine issues.
-
The transportation infrastructure sector utilizes ultrasonic analysis to validate the integrity of critical structures, keeping safety as the North Star.
-
Manufacturers deploy infrared thermography to ward off electrical fires, thus safeguarding both personnel and capital.
In illustrating the practical benefits of CBM, the study by V. M. Kalra et al. on mining haul trucks showcases how condition-based maintenance significantly enhances performance indicators such as downtime reduction and asset preservation. Their findings reveal the pivotal role of CBM in improving equipment productivity and efficiency, thereby supporting the broader implications of CBM in industrial maintenance.
Each industry molds CBM to suit its unique landscape, but the common thread is a strategic foresight that preserves the heartbeat of production – because when equipment thrives, so does business.
Key Takeaways
As we draw the curtain on the explorative journey through Condition-Based Maintenance, let's crystallize the essence of what CBM brings to the industrial stage:
-
Strategic Monitoring: CBM is the art of predictive foresight enabling maintenance staff to act on conditions, not calendars, optimizing machine life and productivity.
-
Informed Investment: While it may require an initial investment in technology and training, CBM's return on investment materializes through extended asset life spans and reduced maintenance costs.
-
Balancing Act: Successfully implementing CBM involves harmonizing the rigors of technology with the fluidity of human expertise and adaptability.
-
Cultural Shift: Transitioning to CBM isn't merely a procedural change—it's a cultural shift that invites organizations to value continuous learning and proactive maintenance strategies.
-
Empowerment through Technology: The right software and tools empower maintenance teams, turning complex data into actionable maintenance decisions and setting the stage for long-term operational success.
FAQs of Condition Based Maintenance
How Does CBM Differ From Non-Destructive Testing?
While they share the goal of asset integrity, CBM and Non-Destructive Testing (NDT) diverge in approach:'
-
NDT is a snapshot, an inspection method that checks for faults without harming the asset. It's typically employed at scheduled intervals or to investigate specific concerns.
-
CBM is a continuous narrative, a proactive scheme that regularly monitors the health of equipment to predict and prevent issues before they arise, rather than checking at intervals.
What Are the Requirements for Implementing an Effective CBM Strategy?
Rolling out a CBM strategy is systematic—it requires:
-
A suite of appropriate condition monitoring tools and sensors to track equipment health.
-
Integration of monitoring tools with a robust data analytics platform to interpret the real-time health of assets.
-
Personnel training to ensure teams can effectively use CBM tools and understand the data they generate.
-
A cultural commitment to ongoing maintenance improvement and a willingness to act on the insights gleaned from CBM data.
Can CBM Be Automated, and How Does This Affect the Maintenance Team?
Yes, CBM can be automated to various degrees:
-
Automation in CBM involves using sensors and software that continually monitor and analyze equipment condition, triggering maintenance actions without human intervention.
-
Far from replacing the maintenance team, automation augments their capabilities, allowing them to focus on higher-level tasks such as strategic planning and complex problem-solving. It shifts their role from reactive to proactive, enhancing overall maintenance operations.