The Real Cost of Ignoring Maintenance in Your Facility


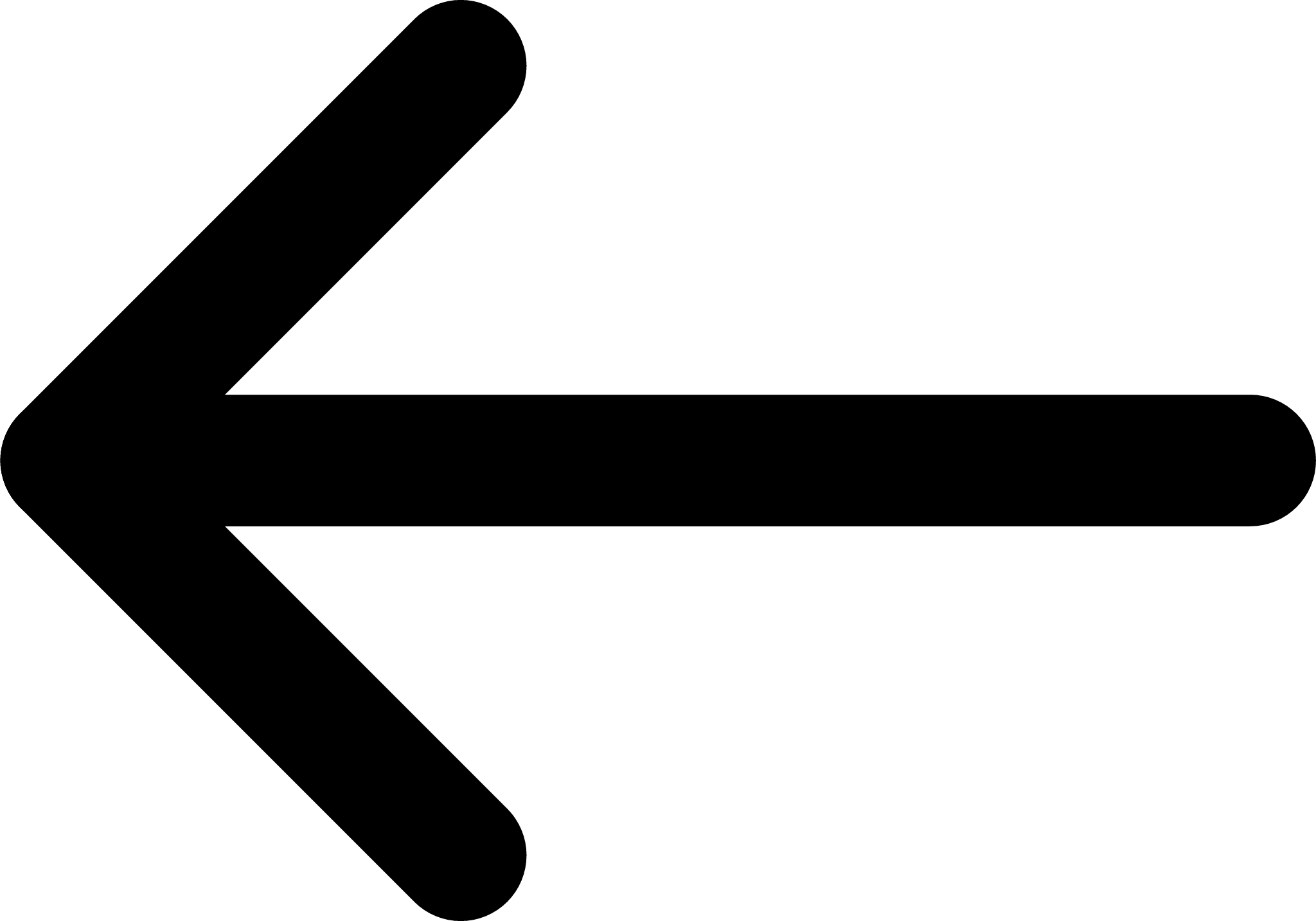
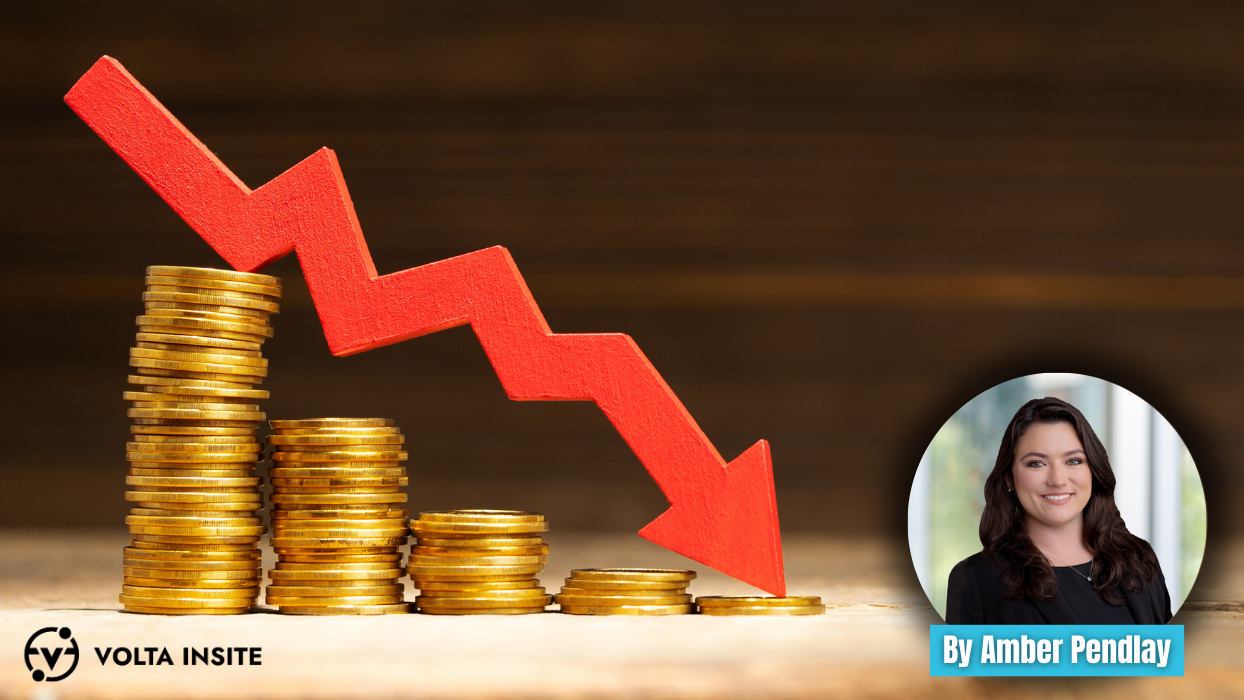
Why Equipment Downtime is a Hidden Cost
Neglecting regular maintenance might seem like a cost-saving measure, but it often results in significant financial and operational losses. On average, businesses experience up to 15 hours of unplanned downtime per week. These interruptions reduce efficiency and erode profits over time.
The Hidden Risks of Neglecting Maintenance
When equipment isn’t properly maintained, it becomes more susceptible to failure. Often, these failures can result in costly repairs, extended downtime, and decreased equipment lifespan.
Without preventative or predictive maintenance, you're likely to face unplanned outages caused by equipment failures that could have been prevented. These breakdowns can disrupt entire production lines, lead to safety hazards, and increase energy consumption. For instance, a single motor failure can halt production, and the repair process may involve expensive labor and parts, in addition to the loss of revenue from the halted operations.
On top of that, unscheduled maintenance often leads to premature wear and tear on equipment. This shortens the life of machinery and increases the frequency of expensive repairs or replacements. The cost of doing nothing is not simply the immediate expense but also the longer-term financial burden that accrues as a result of neglecting proper upkeep.
How Predictive Maintenance Can Save You Money
While preventative maintenance can catch issues before they become major problems - it’s the luck of the draw. Rather than scheduling downtime for maintenance regularly, you can implement predictive maintenance, you can catch issues before they escalate. With solutions like Volta Insite’s InsiteAI, businesses can reduce unexpected failures and minimize the need for expensive repairs—leading to a stronger return on investment (ROI). Predictive maintenance tools allow you to stay one step ahead of potential failures. By continuously monitoring the health of your electrical systems and machinery, predictive maintenance solutions can detect issues before they escalate into costly problems. For example, Volta Insite’s InsiteAI platform uses real-time data and advanced algorithms to monitor your equipment’s condition and predict when components are likely to fail. This enables you to perform targeted, timely interventions that prevent unscheduled downtimes.
The real power of predictive maintenance lies in its ability to prevent these failures from happening in the first place. By implementing such a system, facilities can save money by avoiding unplanned repairs and reducing equipment downtime. In fact, investing in predictive maintenance can lead to a clear return on investment (ROI). InsiteAI, for example, helps facility managers stay proactive by pinpointing specific areas where maintenance is needed, saving both time and money while maximizing equipment uptime.
The True Cost of Inaction
The cost of doing nothing in facility management is far higher than it seems. Unpredictable equipment failures and downtime can quickly add up, straining budgets and affecting productivity. Predictive maintenance is no longer a luxury; it’s a necessity. With solutions like Volta Insite’s InsiteAI, you can optimize operations, avoid costly breakdowns, and achieve a strong ROI by keeping your equipment running smoothly.