4 Ways Predictive Maintenance Reduces Oil & Gas Downtime


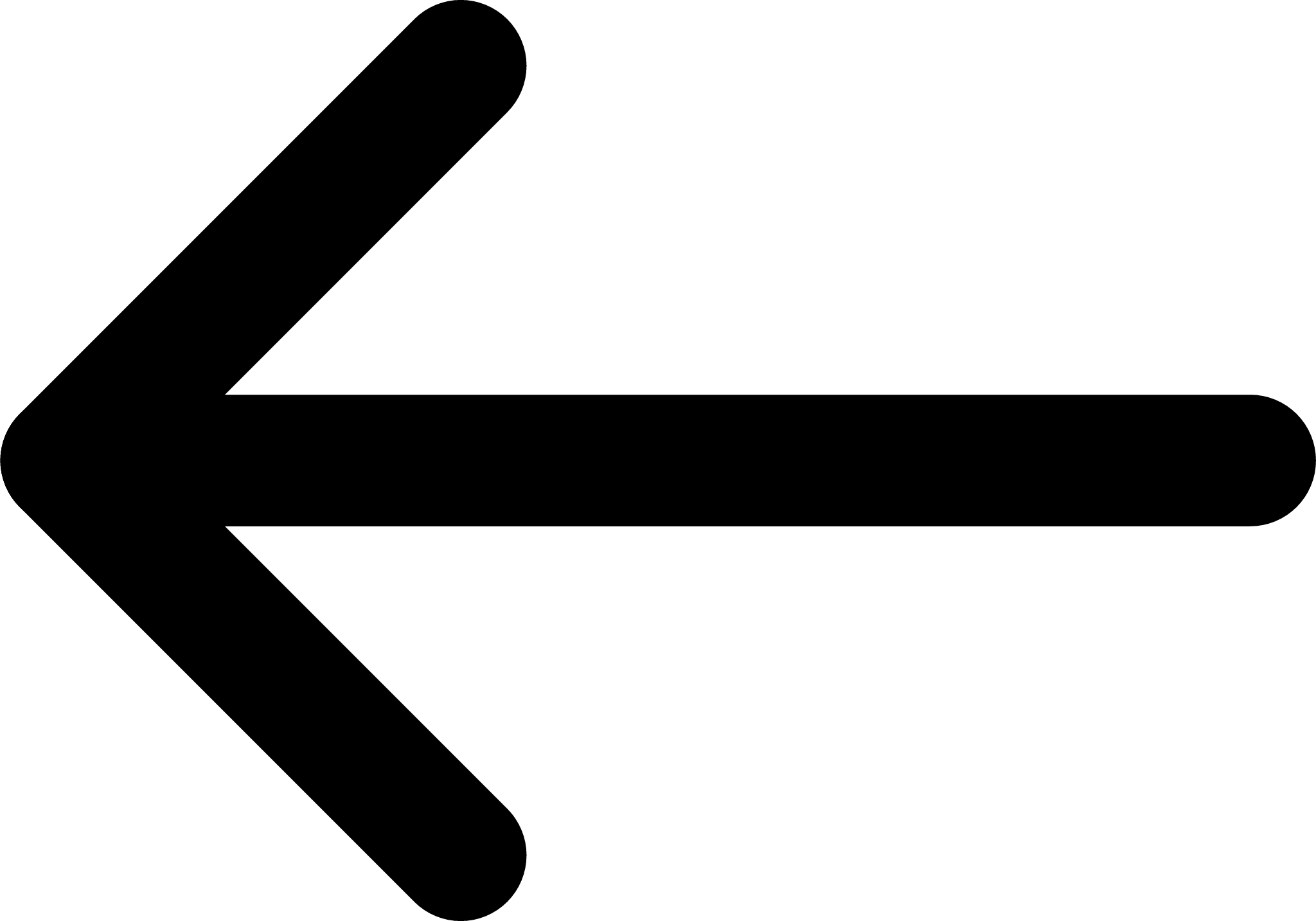
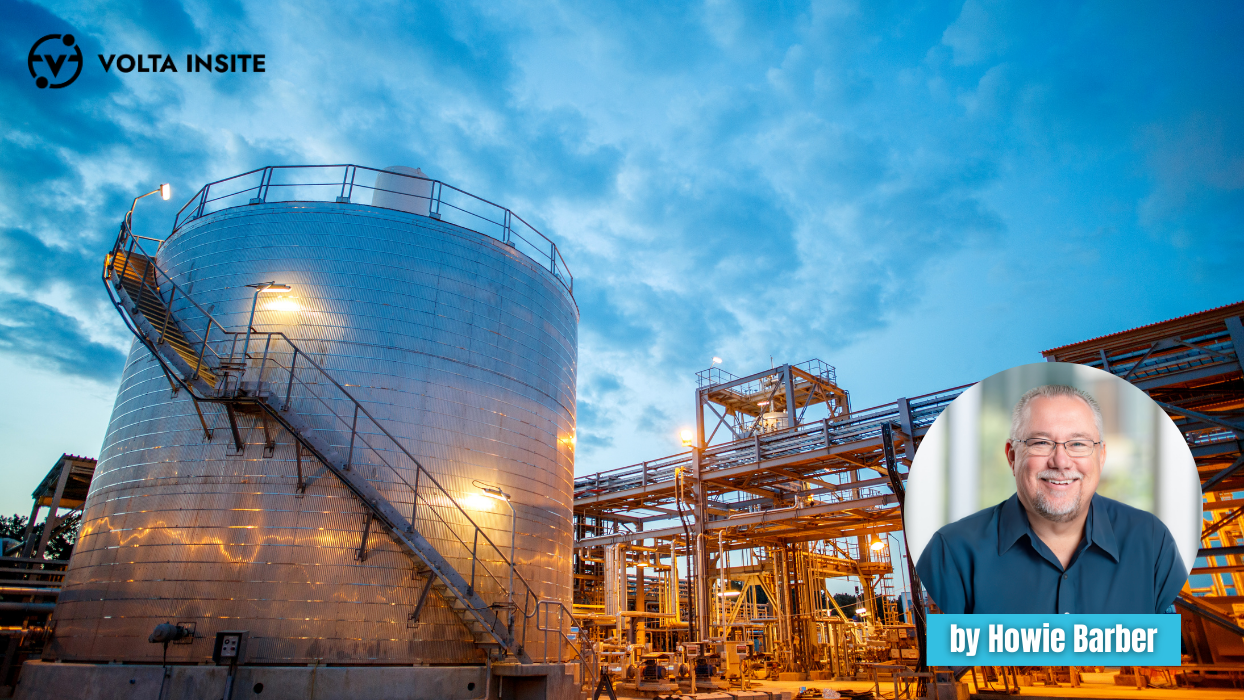
Maintenance programs in the oil and gas industry have evolved significantly since their early days. Advanced technologies like AI, machine learning, and the Internet of Things (IoT) are now central to predictive maintenance strategies.
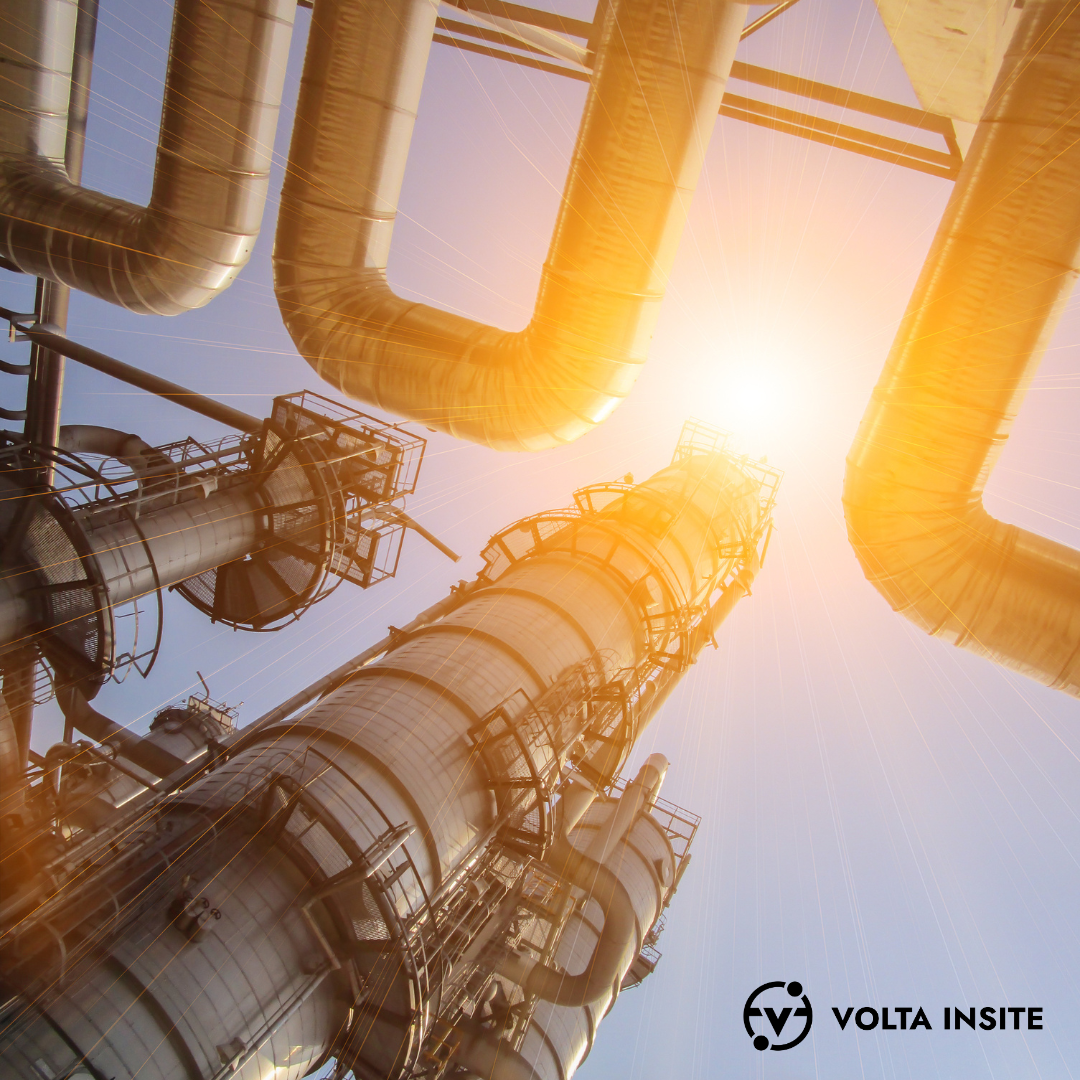
Predictive maintenance (PdM) for oil and gas companies focuses on optimizing asset performance, minimizing downtime, and reducing maintenance costs. Unlike reactive or preventive maintenance, PdM leverages advanced data analytics and condition monitoring to proactively predict equipment failures. This allows oil and gas organizations to forecast the needs of their dynamic operational environments with greater efficiency and accuracy.
Unplanned downtime in the oil and gas industry is costly. For instance, a production facility shut down for repairs can take days or weeks to resume normal operations. Predictive maintenance helps identify potential equipment failures before they occur, allowing companies to schedule repairs during planned maintenance windows and avoiding production losses. Additionally, PdM extends the operational life of equipment and infrastructure.
Volta Insite is a leader in this field, employing Continuous Waveform Capture and the power of InsiteAI's real-time monitoring to lead the way in predictive maintenance. This technology enables 24/7 surveillance of equipment conditions, providing instant alerts at the first sign of potential failure. With InsiteAI, decision-makers have the information they need, can schedule maintenance activities without disrupting normal operations, and assess whether machinery or infrastructure needs a substantial overhaul.
Volta Insite customers can see substantial ROI from the very first issue identified.
4 Ways to Reduce Downtime with Predictive Maintenance from Volta Insite
1. Reducing Unplanned Downtime and Maintenance Costs
Unscheduled downtime is a significant challenge in the oil & gas industry. Volta Insite alerts customers to potential problems before they arise, leading to a reduction in unplanned downtime. InsiteAI detects anomalies early, enabling immediate maintenance actions to minimize the extent and cost of downtime.
2. Optimizing Maintenance Scheduling and Staffing
By accurately predicting equipment failures, oil and gas companies can optimize maintenance schedules and allocate resources more efficiently. This ensures that maintenance activities are conducted only when necessary, minimizing idle time and optimizing workforce utilization.
3. Improving Asset Reliability and Availability
Organizations invest heavily in their assets. Enhancing the availability of these assets improves maintenance KPIs and maximizes the return on investment. Keeping critical equipment operational minimizes production disruptions and maximizes uptime, thereby optimizing overall asset performance.
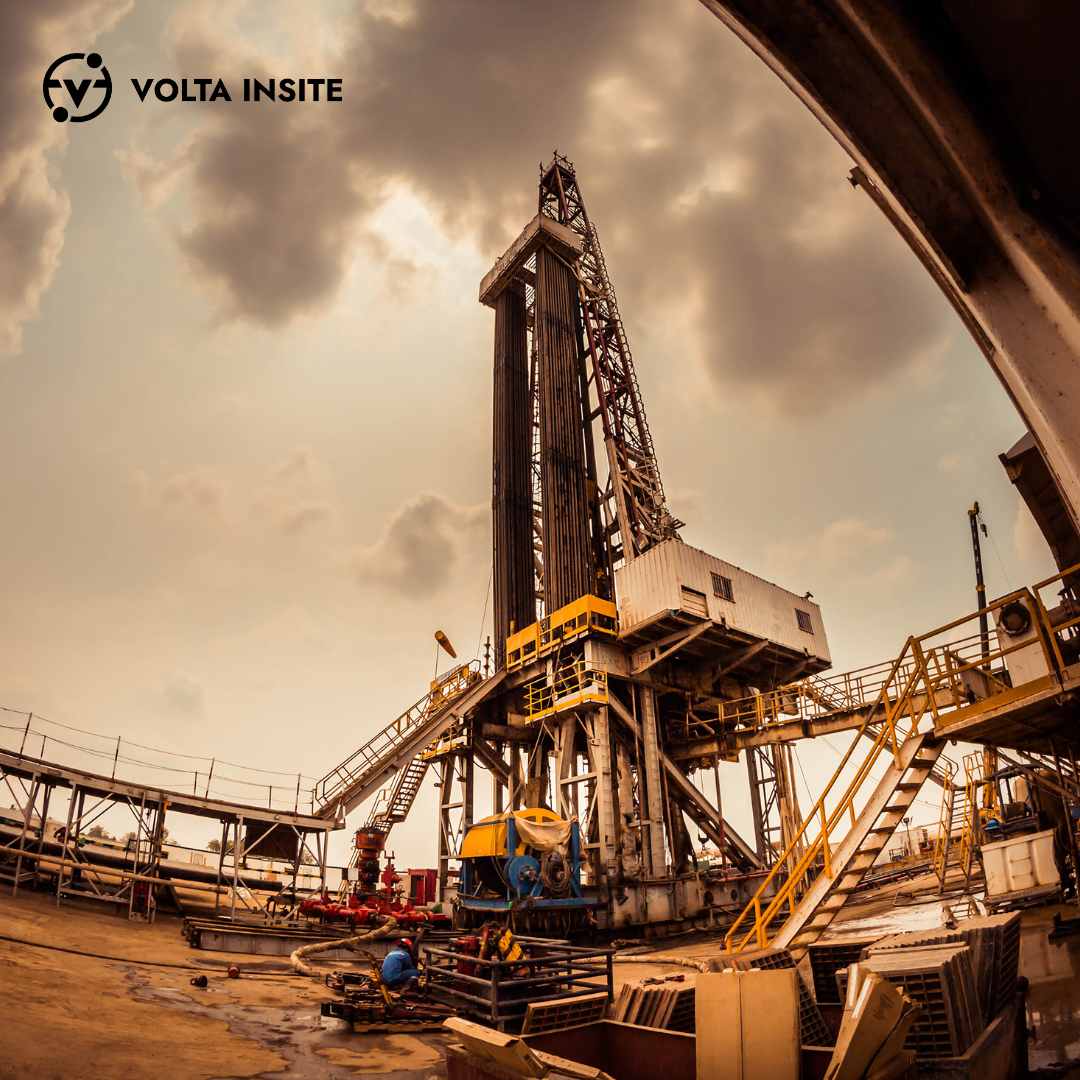
4. Extending Equipment Lifespan
By identifying optimal maintenance intervals and addressing issues early, Volta Insite helps extend the lifespan of assets. This maximizes ROI and defers capital expenditures for replacements. Proactive monitoring and timely intervention help reduce the frequency of equipment replacements, lowering long-term capital costs.
Companies with a robust approach to minimizing downtime and maximizing efficiency will outpace their competitors, and our goal at Volta Insite is to bring that advantage to customers across the gas and oil industry.
Aditional Resources
Predictive Maintenance & Condition Monitoring in Industrial Power Systems
Power Quality Insights: Use Your Analytics to Manage & Diagnose Immediately
How Volta Insite's Predictive Maintenance Software Can Help You