How Pump Failure Affects Water Treatment Facilities


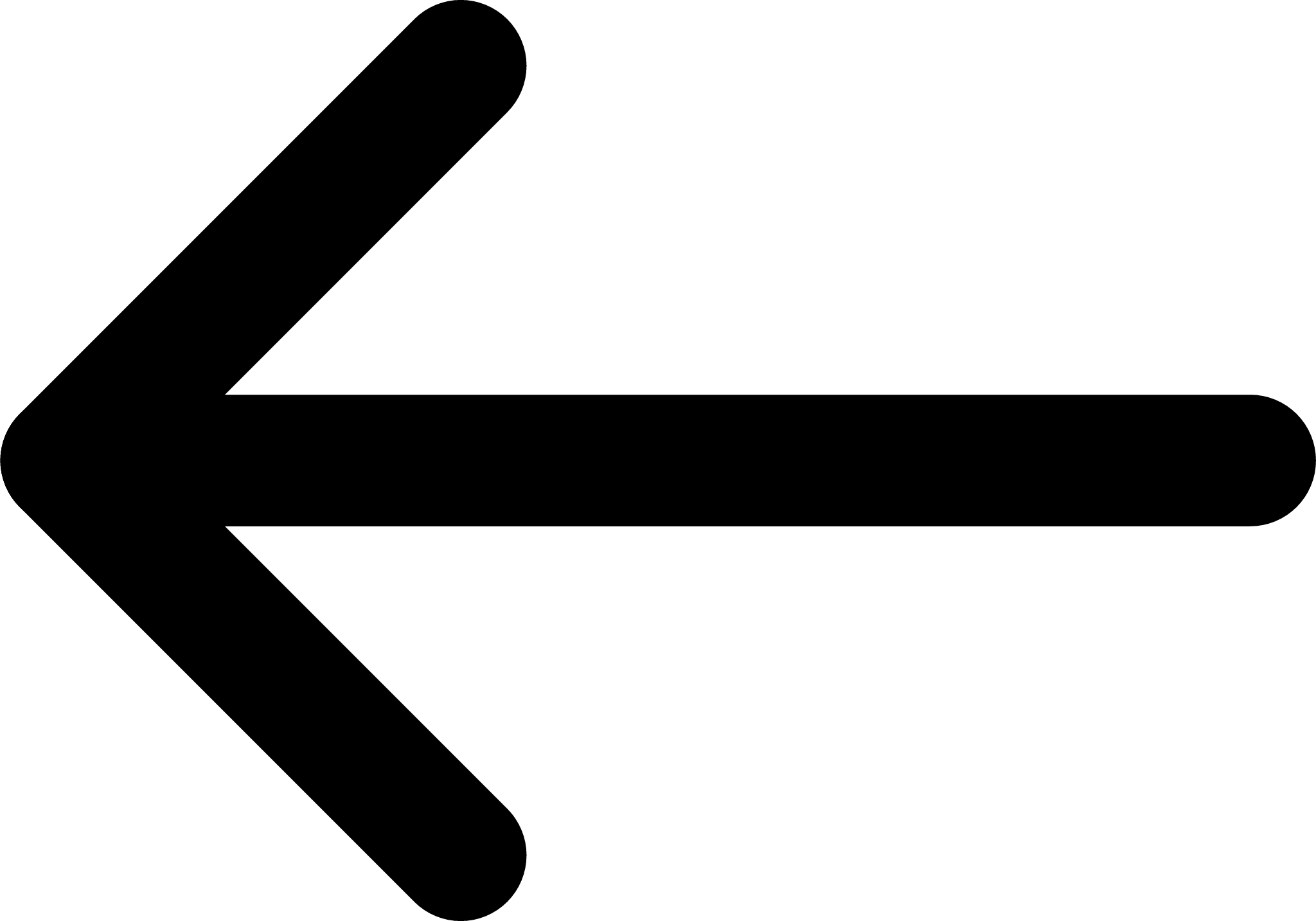
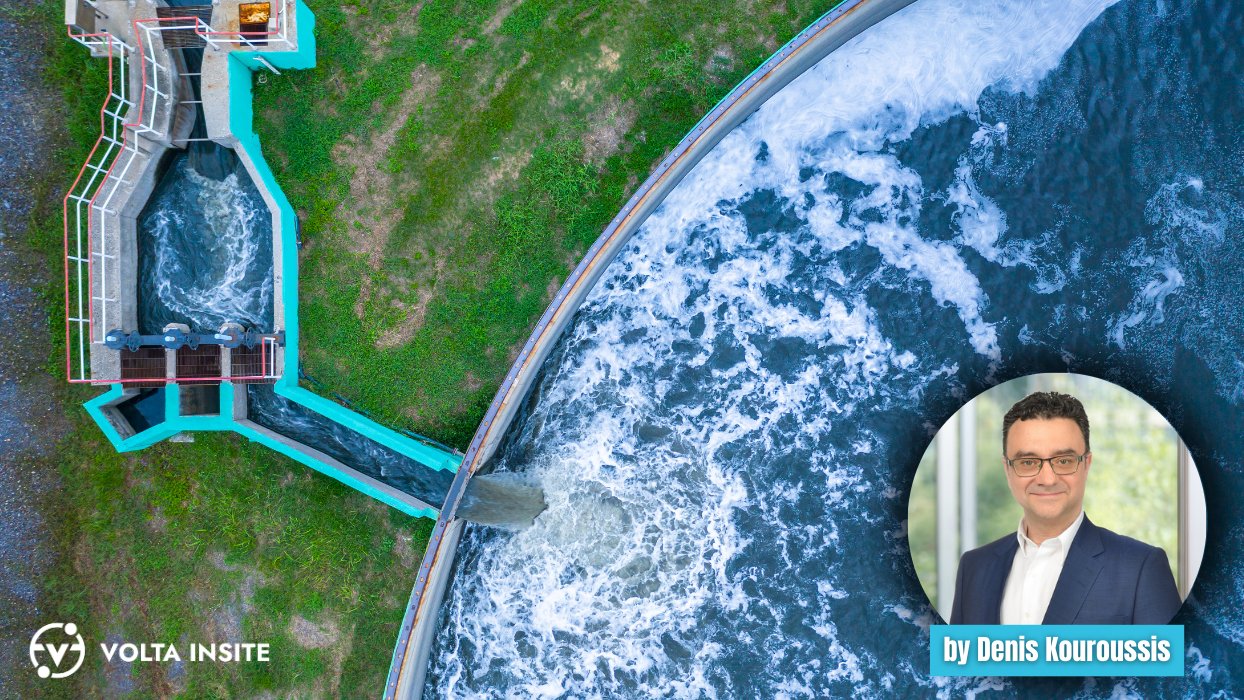
Water treatment facilities play a critical role in providing clean, safe water for communities and industries. At the heart of these facilities are pumps, which are essential for moving water through the various stages of treatment. However, these pumps are subject to wear and tear, and when they fail, the consequences can be far-reaching. Pump failure in water treatment facilities can lead to significant operational inefficiencies, costly repairs and potential regulatory fines. Even worse, the quality of the treated water can suffer, which poses health risks to the public and damages the facility’s reputation.
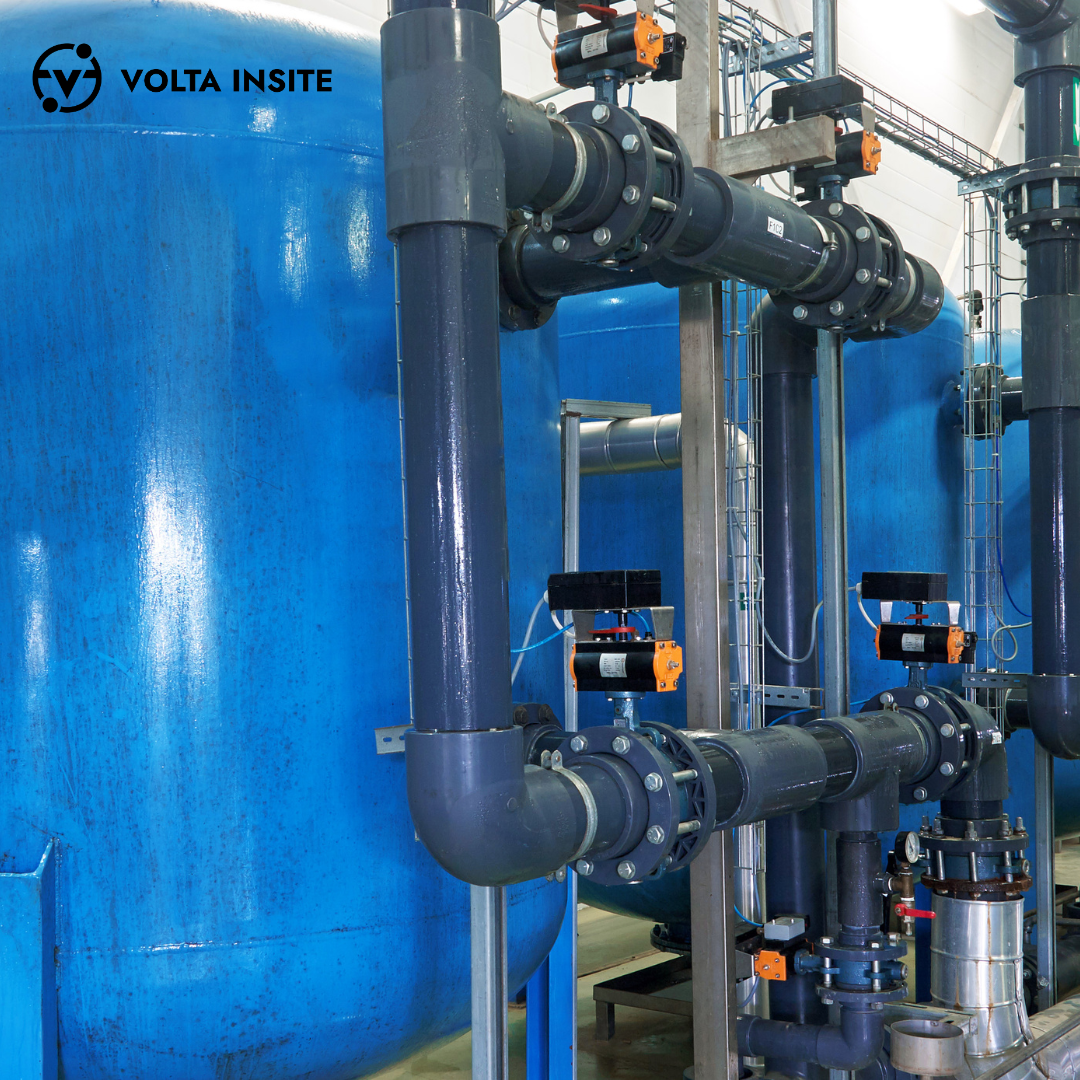
Consequences of Pump Failures in Water Treatment
When pumps fail, the entire water treatment process is compromised. A pump breakdown can interrupt the flow of water causing imbalances in the treatment process. This can result in untreated or partially treated water being released, which can violate environmental regulations and public health standards. Additionally, pump failure can cause equipment upstream and downstream to work harder, leading to increased energy consumption and faster deterioration of other machinery.
The financial costs associated with pump failure can be staggering. Beyond the immediate expense of repairing or replacing the faulty equipment, there are additional costs such as lost productivity, increased energy usage, and potential penalties for non-compliance with environmental regulations. Water treatment facilities, which are often operating on tight budgets, can find themselves overwhelmed by the costs of repeated reactive maintenance efforts.
Downtime and Its Hidden Costs
Unexpected downtime is one of the biggest risks posed by pump failure. When pumps go offline, the entire system can be brought to a halt, resulting in significant delays in water treatment and supply. In a facility where time is of the essence, downtime means wasted resources, delayed operations and potential impacts on the availability of clean water to the surrounding community.
Moreover, downtime caused by pump failure can lead to water quality issues. Inconsistent water flow through treatment processes can result in incomplete chemical reactions or sedimentation leading to untreated or substandard water being distributed. This not only affects public health but can also lead to regulatory penalties, as water quality standards must be strictly adhered to.
Pump failure may also damage other critical components in the system. Valves, filters and other equipment that rely on constant pressure and flow may be put under stress during a pump failure, accelerating their wear and increasing the likelihood of more extensive system damage. In the worst cases, pump failure can lead to complete facility shutdowns which cause disruptions that take days or even weeks to resolve.
A Proactive Approach Using Predictive Maintenance
To mitigate the risks associated with pump failure, many water treatment facilities have begun to adopt predictive maintenance strategies. Traditional reactive maintenance – waiting for something to break and then fixing it – is being replaced by proactive maintenance that relies on real-time data and advanced analytics to predict when equipment is likely to fail.
Predictive maintenance allows water treatment facility managers to address potential issues before they become critical problems. By using sensors, data collection systems and sophisticated algorithms, predictive maintenance identifies early warning signs of equipment degradation. This approach helps ensure that repairs can be scheduled during planned downtime, avoiding the expensive disruptions caused by emergency repairs and system failures.
Predictive maintenance also extends the lifespan of pumps and other equipment by preventing unnecessary wear and tear. Instead of running pumps until they fail, predictive maintenance enables facilities to maintain them at optimal efficiency. This reduces the overall cost of ownership and improves the return on investment for expensive water treatment equipment.
How InsiteAI from Volta Insite Can Help Water Treatment Facilities
At the forefront of predictive maintenance solutions is Volta Insite’s InsiteAI, a cutting-edge tool designed to revolutionize how water treatment facilities manage their pumps and other critical equipment. InsiteAI uses advanced analytics and machine learning algorithms to monitor the performance of pumps in real time, detecting even the smallest anomalies before they can lead to a breakdown.
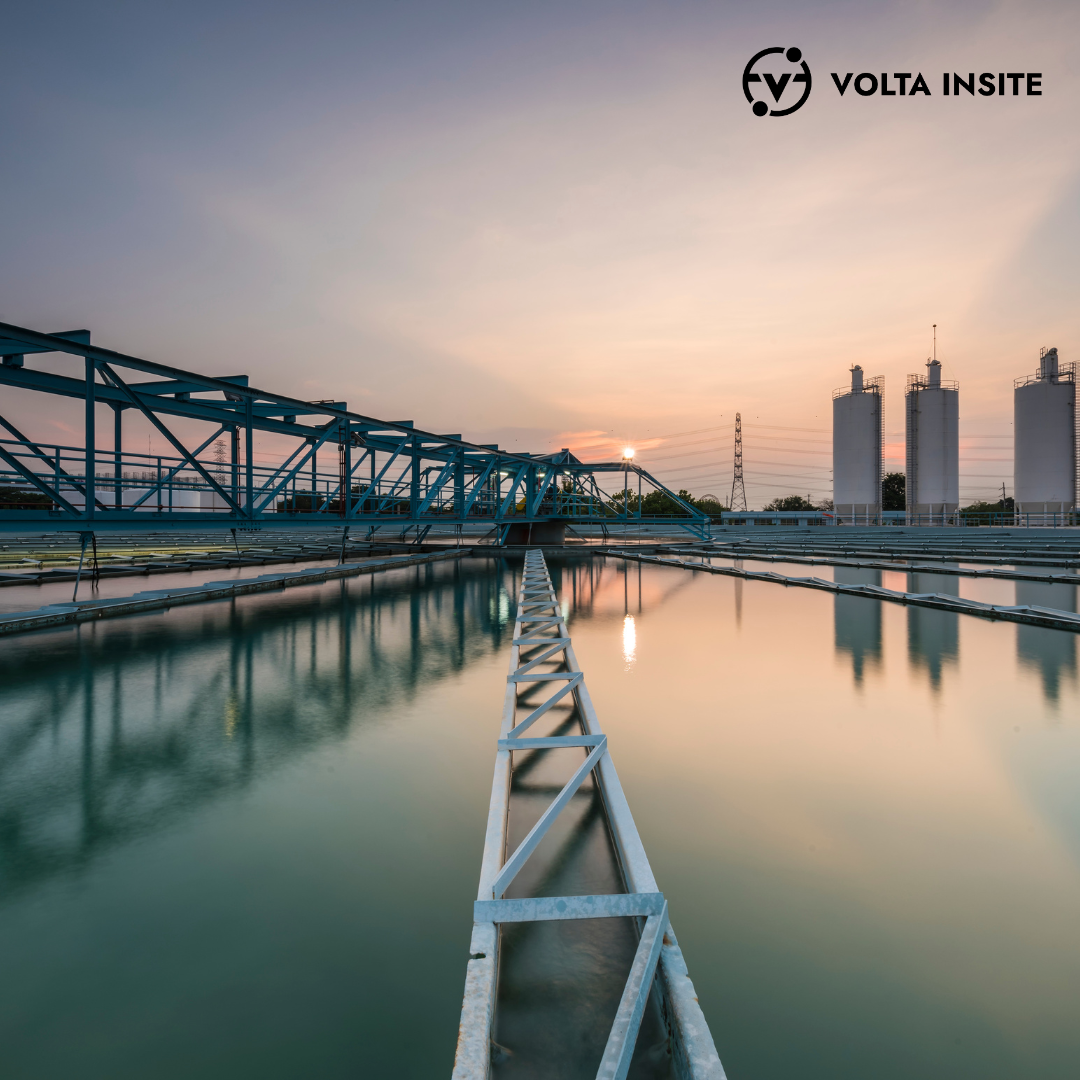
InsiteAI’s dynamic dashboard provides facility managers with invaluable insights into the health of their pumps and the overall system. By continuously analyzing data from sensors, InsiteAI identifies patterns and trends that indicate potential failures. Real-time alerts are sent to operators when pump performance deviates from normal allowing for immediate intervention and preventing unplanned downtime.
With InsiteAI, you can set up customized alerts for specific parameters, such as temperature, vibration, and pressure, which are key indicators of pump health. This means you can proactively address issues before they escalate into costly breakdowns. The system also helps optimize the performance of pumps, reducing energy consumption and improving overall efficiency.
Contact Volta Insite Today!
By investing in predictive maintenance solutions like InsiteAI, water treatment facilities can avoid the pitfalls of reactive maintenance, reduce downtime, and ensure a continuous supply of high-quality water. The combination of real-time monitoring, predictive analytics, and advanced alerts means that you’ll never be caught off guard by a pump failure again. InsiteAI offers a smarter, more efficient way to manage your facility’s most critical assets, maximizing both uptime and equipment lifespan.