Predictive Maintenance of Pumps Using Condition Monitoring


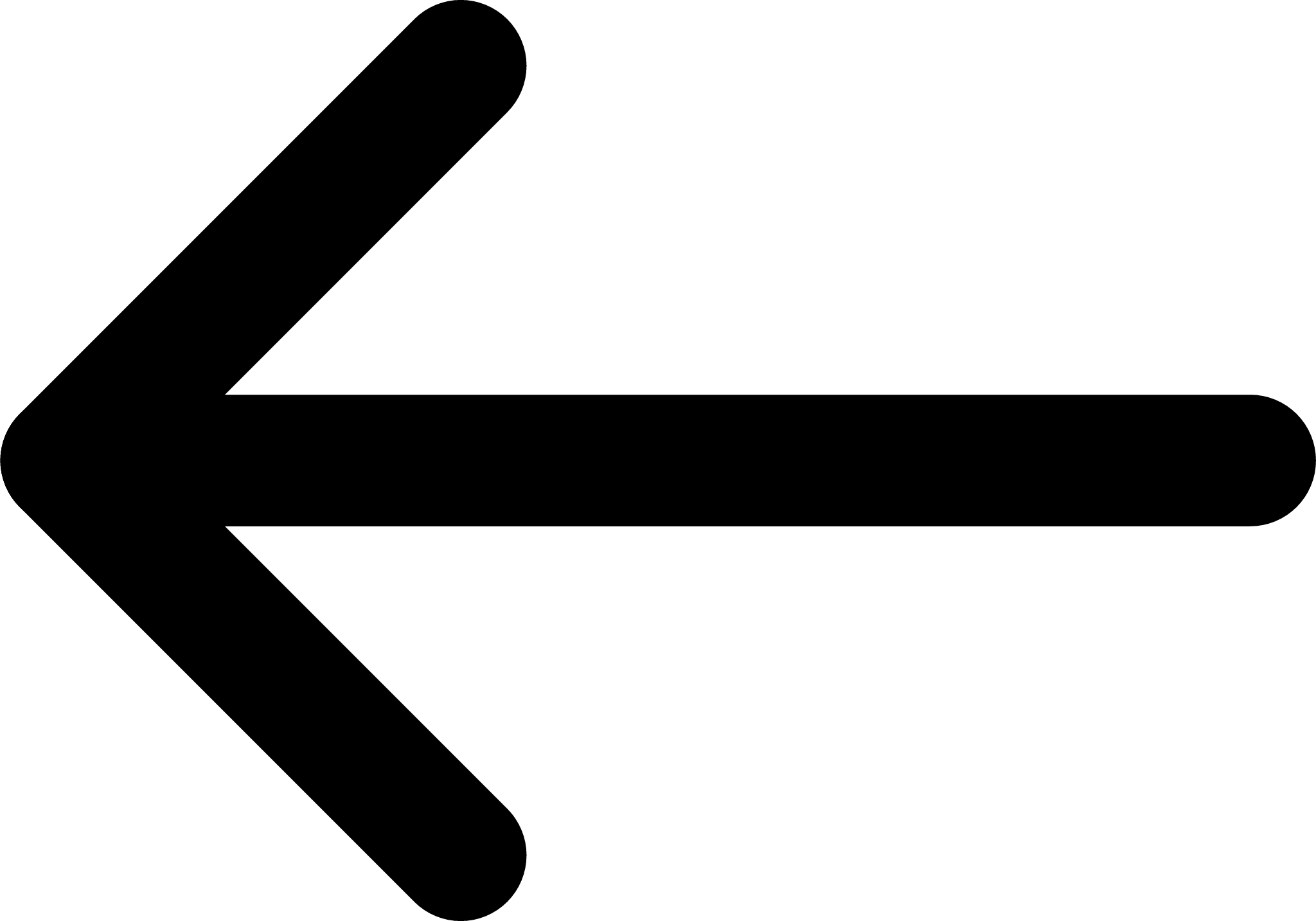
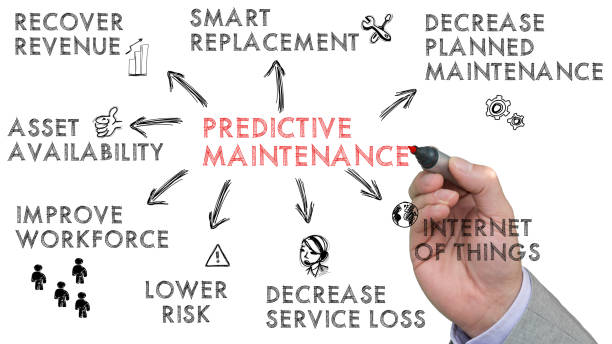
When every second of operational uptime counts, the concept of predictive maintenance for pumps with condition monitoring emerges as a game-changer. Predictive Maintenance is far more than just a fancy term, it's a strategy that employs cutting-edge sensors and analytics to foresee and fix potential pump problems before they escalate into costly shutdowns. Let's delve into the nuts and bolts of this innovative approach, shedding light on why understanding and implementing it could be the key to keeping your operations smooth and uninterrupted.
What Is Predictive Maintenance for Pumps Using Condition Monitoring?
Predictive maintenance for pumps using condition monitoring involves using sensors and data analytics to track the real-time performance of pumps, such as vibration patterns, temperature changes, and electronic signatures. This approach allows for smart, timely maintenance decisions to prevent unexpected failures and downtime. Volta Insite's InsiteAI™ Automated intelligence enhances this process by learning from the data collected across multiple pumps, making it easier to identify and address potential issues before they escalate.
Distinguishing Predictive Maintenance From Reactive and Preventive Maintenance
Predictive maintenance distinguishes itself from reactive and preventive maintenance by its proactive approach. Instead of waiting for equipment to fail (reactive) or scheduling maintenance at fixed intervals regardless of actual need (preventive), predictive maintenance uses intelligent sensors to monitor equipment in real-time. This allows for the early detection of potential issues, often days or months in advance, enabling maintenance actions to be taken just in time to prevent failure. This strategy relies on data analysis and sensor technology to optimize the maintenance of assets, ensuring they receive attention only when necessary.
Key Components and Technologies in Predictive Pump Maintenance
Dive into the world of predictive maintenance and you'll find a bunch of high-tech players. We're talking sensors that track everything from vibration to temperature, and wireless communication solutions that send that data flying to the places it needs to go. Then there's the Volta Insite side of things --- Electrical Signature Analysis (ESA), algorithms and automated intelligence that dig into that data and pull out insights that can tell you if your pump's heading for a problem. Using InsiteAI is like having a crystal ball for your pumps, telling you what part might fail next and when to act to keep things running smoothly.
The Role of Condition Monitoring in Predictive Maintenance
Condition monitoring is the heart of predictive maintenance. Imagine tying a sensor to every part of the pump that could tell you how it's feeling. It's like giving your pump a way to speak up when it's not feeling great. This system keeps an eye on how the pump is doing at all times, alerting you to the most miniscule changes that could mean trouble is brewing. It leverages machine learning to turn mountains of data into practical advice for maintaining your pumps, ensuring they're in optimal condition and ready to keep on pumping without costly interruptions.
Common Pump Failures and the Importance of Early Detection
You might think pumps fail without warning, but they're actually quite chatty before giving up. Knowing the whispers of a failing pump can save you from a loud, costly breakdown. A pump in distress might cling to life for a bit, but left unchecked it's a disaster waiting to happen. This is where detecting the early cries for help becomes crucial and can be the difference between a quick fix and a full-on production stop. InsiteAI collects data on a granular level to detect the problems before they become downtime problems.
Mechanical Failure Symptoms in Pumps
Mechanical failure symptoms in pumps include noticeable vibrations, rattling from loose components, and leaks, which signify potential problems. Additionally, worn-out bearings may produce grumbling noises, and a failing pump seal may result in drips, indicating the need for maintenance. Recognizing these symptoms early can prevent operational disruptions and costly repairs.
Fluid Dynamics Issues Leading to Pump Failure
Fluid dynamics issues, such as cavitation caused by a pump working too hard, can lead to pump failure. Cavitation occurs when vapor bubbles form and collapse inside the pump, causing damage similar to being struck by tiny hammers. Incorrect flow rates, either too high or too low, can also strain the pump excessively. These issues are akin to forcing a swimmer to race with weights attached, ultimately leading to failure. Proper management of fluid dynamics is crucial to prevent overstraining and ensure the longevity of pump systems.
Early Indicators of Failure in Pump Systems
Early indicators of failure in pump systems include unusual noises such as rumbling, whining, or screeching, and elevated temperatures, similar to a fever indicating underlying issues. Recognizing these signs early can prevent significant damage, acting like smoke alarms for pump health and allowing for timely intervention to avoid more severe problems.
Selecting the Optimal Condition Monitoring Tools for Pump Maintenance
Choosing the right tools to monitor pumps is like picking the best guardians for your equipment. They need to be sharp, vigilant, and versatile enough to cope with the unexpected. There's a maze of options out there, and finding tools that can crisp up the faintest signs of a pump's cry for help will set you on the path to maintenance and operation nirvana.
Vibration Monitoring Technologies for Pump Health
When you want to catch a pump crying wolf before there's a real problem, vibration monitoring tech is your go-to detective. Imagine having a sensor so sensitive, it picks up on the secretive chatter of misalignment or a bearing planning its farewell. These devices measure the shakes and shudders that might spell trouble, allowing you to leap into action. It's all about transforming vibrations into valuable data that whisper the secrets of a pump's inner life.
How Advanced Sensors and IMUs Play a Role in Condition Monitoring
Advanced sensors and Inertial Measurement Units (IMUs) are the spies in the world of pump maintenance. They take on the sneakiest of tasks---capturing the unseen twitches and turns of machinery. With absolute accuracy, these gadgets measure the tilt and thrust of pumps, revealing secrets even the most reliable eyes might miss. They're the special agents that track every move, ensuring nothing goes unnoticed and that every potential issue is flagged long before it becomes a mission-critical fiasco.
Volta Insite offers Real-Time Monitoring for Comprehensive Pump Assessment
Stepping up to InsiteAI's real-time monitoring is like going from a snapshot to a full-length documentary about your pumps' lives. It gives you the narrative of their operation, drama included, as it happens. Real-time monitoring doesn't just reveal what's up; it shows you the movie of your pumps' health, playing 24/7 on your command.
The Advantages of Wireless Vibration Sensors in Pump Monitoring
Wireless vibration sensors are the ninjas of pump monitoring. They slip into tight spaces, stick to their posts without a fuss, and send intel back without a single wire in sight. With their stealth, they are revolutionizing pump monitoring by allowing flexibility in placement and real-time data transmission. They shrink downtime by providing immediate alerts, and since they're so easy to install, you can have an army of them guarding every potential weak spot in your pump systems.
The Significance of Edge Processing in Monitoring Systems
Edge processing acts like the smart reflexes of monitoring systems. By processing data right where it's collected, there's no lag time---no need for the data to travel to a central nervous system before making a decision. This means the monitoring system can react instantly to anomalies, triggering swift, localized responses that can potentially stop faults in their tracks. Edge processing keeps data flowing smoothly and smartly, making sure that not a single tremor of trouble slips through unnoticed.
InsiteAI gives 24/7 Visibility of Pump Health Through Continuous Monitoring
Continuous monitoring keeps your eyes on the prize: uninterrupted operation. It's the round-the-clock surveillance that gives you the peace of mind that Big Brother could only envy. Pumps wear capes in modern industry, and giving them 24/7 visibility means you can swoop in at the first sign of distress. The magic in continuous monitoring is in its relentless vigilance, offering a never-blinking gaze that catches issues whenever they dare to surface. It means getting ahead of problems that used to play hide and seek, and maintaining performance at its peak.
Utilizing Data and Analytics for Intelligent Pump Maintenance
Harnessing the power of data and analytics transforms pump maintenance from a guessing game into a science. This isn't just number-crunching for the sake of it---this is about turning streams of data into a fountain of knowledge. With the support of Volta Insite's engineering team , your complex pump systems become an open book, revealing insights that help keep them running smoothly and smartly.
Anomaly Detection and the Use of AutomatedIntelligence
Anomaly detection is like having an always-on, ever-learning detective in your system. By using InsiteAI, it spots deviations from the norm, the tiny hiccups that spell trouble, which human monitoring might overlook. AI isn't just good -- it's uncanny in its ability to learn what 'normal' looks like and then flag anomaly patterns. It's proactive, it's precise, and it means catching minor issues before they grow into costly catastrophes.
Using Algorithms and Deploying Them in Operation
Algorithms are the secret sauce in your maintenance strategy. They make sense of the jumble of data, picking out what's important and what's just noise. These smart math-based tools can predict which pump part might call it quits next or when to schedule a check-up---all with a level of precision that's like a laser-guided system for your maintenance operations. Deploying algorithms means being one step ahead, always. Once an anomaly is detected an alert is generated allowing you precious time to prevent the impending downtime.
Interpreting Monitoring Data and Diagnostic Testing
Diagnostic testing is the MRI for your pumps---it gets down to the nitty-gritty of internals without needing to take anything apart. But getting the data is only half the battle. It's the interpretation that turns it into actionable insights. This is where experience waltzes with technology, crafting a maintenance plan that's both informed and intuitive. With this, every monitoring signal, each temperature readout, and every vibration pattern becomes a meaningful cue to optimal pump health and function.
Key Takeaways
-
Smart Maintenance: Predictive maintenance reshapes the approach to pump care, turning maintenance schedules from calendar-based to condition-based with the help of smart sensors and InsiteAI.
-
Early Detection: Catching anomalies through continuous, real-time monitoring with advanced edge processing is critical to preventing pump failures and expensive downtime.
-
Advanced Analytics: Data-driven strategies facilitated by anomaly detecting InsiteAI, insightful algorithms, and practiced interpretation of diagnostics are key for intelligent pump maintenance.
-
Strategic Implementation: Transitioning to modern monitoring tools and starting with a Volta Insite pilot program pave the way for implementing effective condition monitoring across operations.
-
Inspiring Confidence: Success stories highlight the value of predictive maintenance in avoiding unplanned downtime, while adaptation to new failure modes ensures ongoing operational resilience.
FAQs of Predictive Maintenance of Pumps with Condition Monitoring
What Makes Condition Monitoring Essential in Predictive Maintenance Strategies?
Volta Insite's condition monitoring is essential in predictive maintenance strategies because it acts as a continuous health check for equipment, identifying issues early. This allows for planned repairs before failures happen and maintenance schedules to be optimized based on real needs instead of guesswork. This approach not only saves time and money but also enhances efficiency and extends the lifespan of equipment.
How Can Real-Time Data Analysis Extend Pump Lifespan and Efficiency?
Insite AI's real-time data analysis extends pump lifespan and efficiency by continuously monitoring pump performance and identifying potential issues early. This allows for timely interventions to prevent minor problems from escalating into major ones, reducing wear and tear and keeping pumps operating at optimal levels. Consequently, this proactive approach leads to longer pump life and enhanced operational efficiency.
Which Industries Benefit Most From Predictive Maintenance of Pumps?
Industries that benefit most from predictive maintenance of pumps include water treatment and municipal services, oil and gas, power generation, manufacturing, medical facilities, pharmaceuticals, and food processing. These sectors depend heavily on the continuous operation of pumps for their daily activities, where interruptions can lead to significant costs, production losses, and safety risks. Predictive maintenance serves as a crucial safeguard, ensuring that pumps remain operational, thereby maintaining industry efficiency and safety.