Power Quality and ESA in Predictive Maintenance


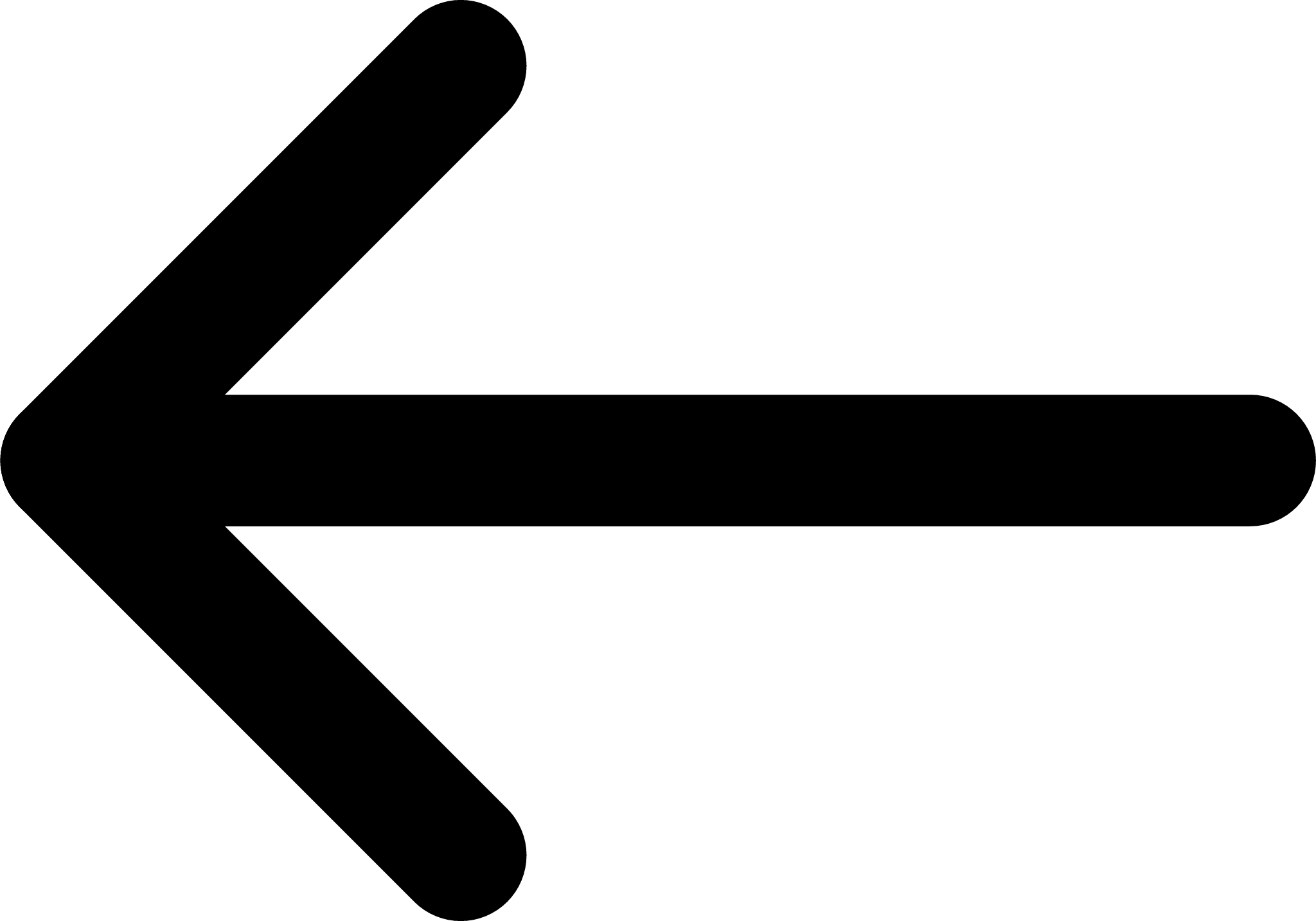
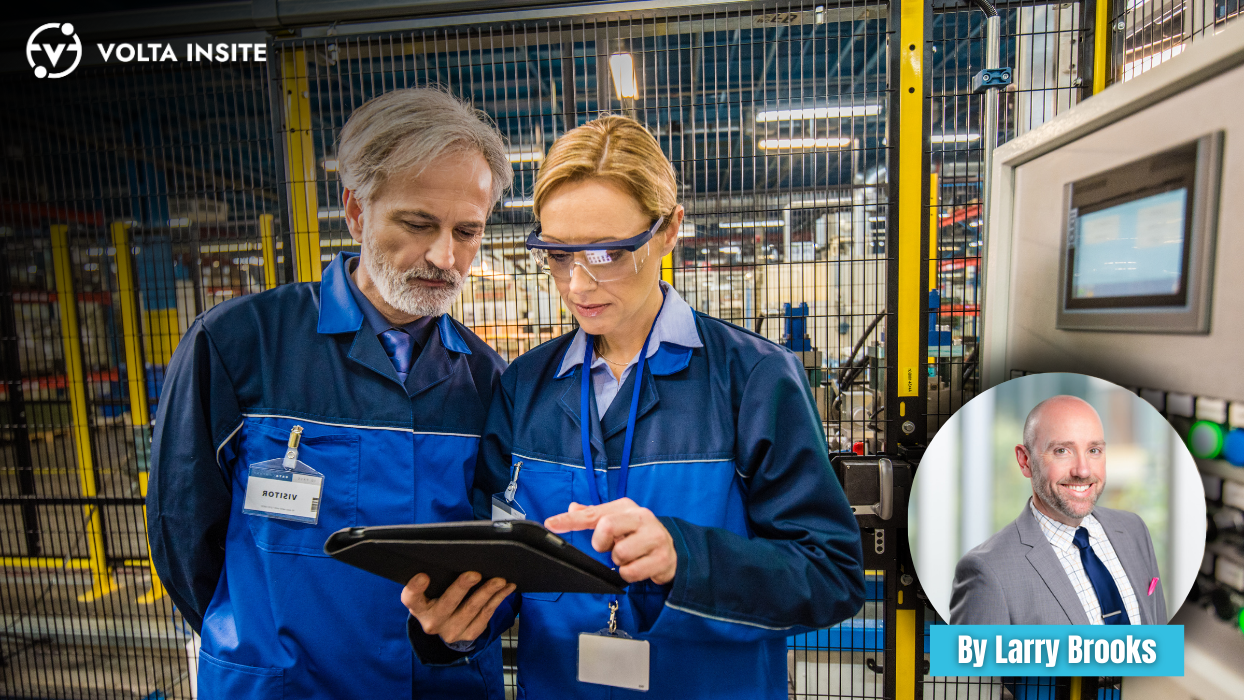
Equipment downtime can result in significant revenue loss, safety risks, and operational inefficiencies in industrial and manufacturing environments. Power quality and Electrical Signature Analysis (ESA) are two critical components of predictive maintenance strategies designed to minimize disruptions and optimize the performance of electrical systems. By proactively monitoring and analyzing these factors, facilities can address potential issues before they escalate, safeguarding both productivity and profitability.
The Importance of Power Quality
Power quality directly impacts the efficiency and lifespan of equipment. Ideally, a power supply should maintain steady voltage levels, minimal harmonic distortion, balanced phases, and a consistent frequency of 50 or 60 Hz. However, "dirty power"—characterized by voltage sags, swells, transients, and harmonic distortions—can cause electrical components to malfunction or fail altogether.
Voltage transients, for instance, can lead to abrupt current spikes, damaging critical control systems or motors. Harmonic distortion caused by variable frequency drives (VFDs) can ripple through a facility, stressing transformers and other equipment downstream. Left unaddressed, these issues can result in costly downtime, with disruptions in sectors like manufacturing and energy costing anywhere from $250,000 to $2.5 million per hour.
Power Quality Monitoring
To ensure voltage stability, facilities must implement robust monitoring systems. Volta Insite's advanced hardware and software solutions, such as the VI module, provide continuous power quality monitoring with high-resolution data sampling. This technology offers insights into the root causes of power instability, whether stemming from utility variations or internal distribution issues.
For example, synchronized monitoring across multiple nodes can pinpoint whether a transient issue originates at the utility level or within a specific piece of internal equipment. Such visibility enables rapid diagnosis and targeted corrective actions, reducing downtime and improving equipment reliability.
Electrical Signature Analysis (ESA)
While power quality addresses the stability of electrical inputs, ESA focuses on the condition of electromechanical systems, such as motors, compressors, and fans. By analyzing the current waveform, ESA can detect specific faults—like loose belts, unbalanced blades, or gearbox issues—without the need for physical sensors on the equipment.
Using Volta Insite's technology, facilities can track harmonic signatures that correlate with specific mechanical problems. For example, a rising harmonic frequency might indicate belt degradation, while irregular vibrations could suggest debris buildup on fan blades. Maintenance teams can act on these insights, performing repairs or replacements before failures occur.
Predictive Maintenance in Action
The value of combining power quality monitoring with ESA lies in its ability to transform reactive maintenance into proactive strategies. One notable example involves a fan with imbalanced blades due to debris accumulation. Volta Insite's InsiteAI detected the issue through harmonic analysis, prompting the maintenance team to clean and rebalance the fan blades. This proactive approach reduced vibrations and restored system efficiency.
Similarly, voltage monitoring has helped facilities identify and mitigate voltage transients caused by failing contactors or utility variations. With such tools, downtime is minimized, and operational safety is enhanced.
Partner with Volta Insite Today!
Power quality and ESA are foundational to predictive maintenance programs that prioritize efficiency and reliability. By leveraging advanced monitoring solutions like those offered by Volta Insite, facilities can reduce downtime, prevent costly failures, and extend the lifespan of critical equipment. The result? A smarter, more resilient operational framework that ensures long-term success.