Optimize Operations: Motor Current Signature Analysis


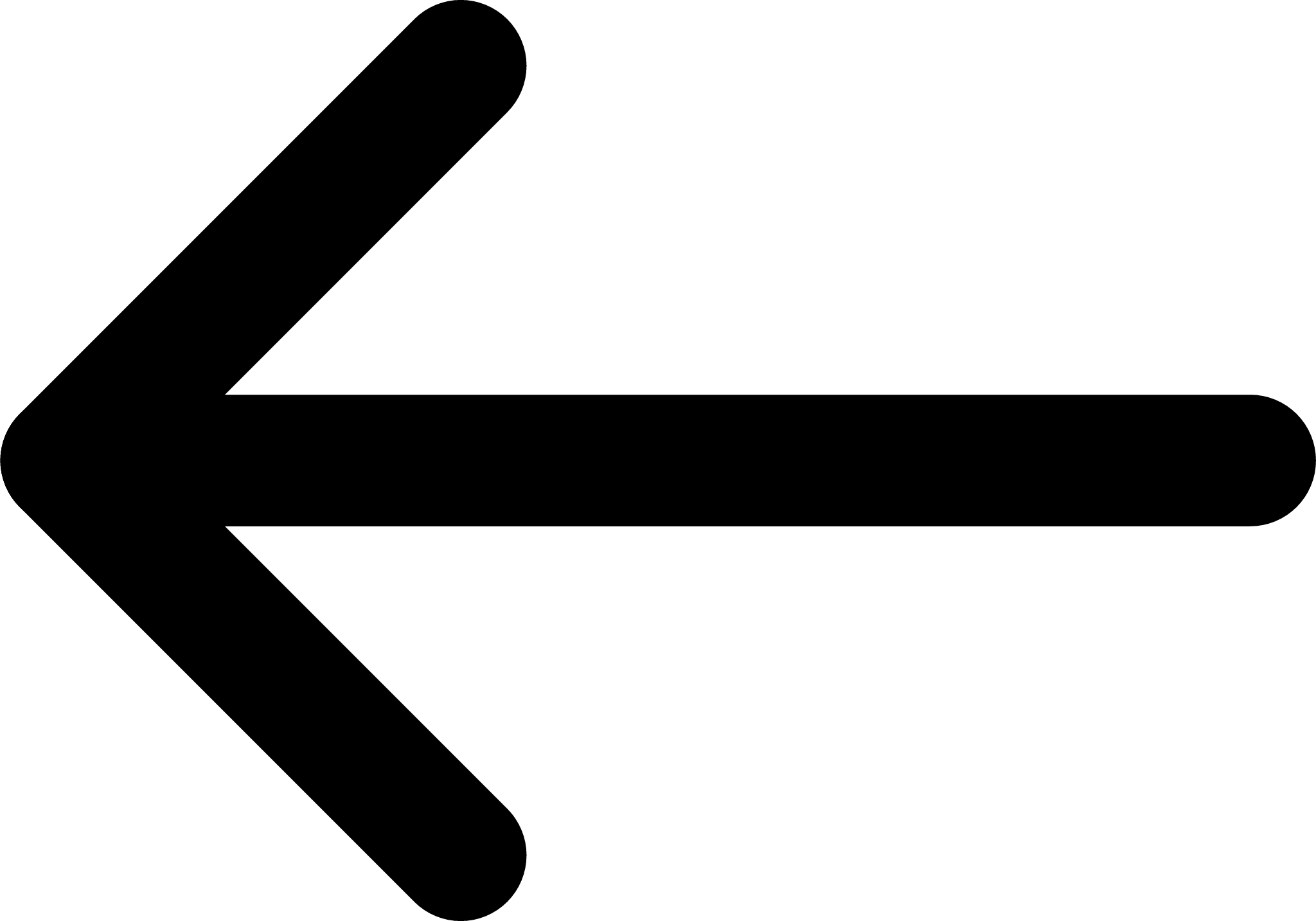
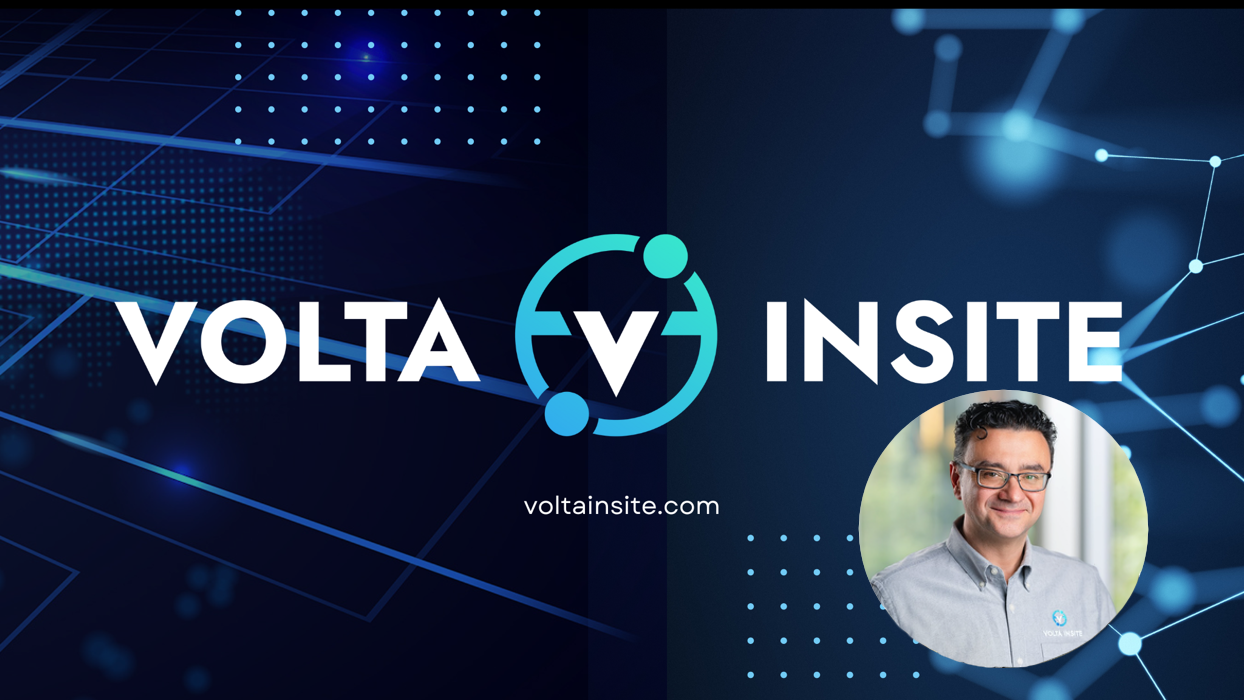
In a world where machine downtime means lost revenue, Motor Current Signature Analysis (MCSA) emerges as a crucial ally in predictive maintenance. This technique allows experts to decipher the health of motors by analyzing their electrical consumption patterns, helping to detect issues before they become costly problems. Read on to discover how MCSA is revolutionizing industrial maintenance, offering businesses a chance to stay ahead of breakdowns and optimize their operations.
What is Motor Current Signature Analysis?
Motor Current Signature Analysis (MCSA) is the powerhouse behind modern predictive maintenance strategies. It's a smart, sensitive technique to snoop on the health of motors by scrutinizing the complexities of their electricity consumption. Using this method, we can spot trouble in electrical machinery long before it throws a wrench in your operations.
Key Principles in Detecting and Analyzing Fault Frequencies
The key principles in detecting and analyzing fault frequencies with MCSA involve analyzing the motor's electrical signal frequency spectrum to identify patterns indicative of faults. This includes recognizing the specific disturbances caused by issues like bad bearings, broken rotor bars, or static eccentricity. By correlating these electrical anomalies with mechanical faults, MCSA acts as an early-warning system, enabling proactive maintenance and ensuring uninterrupted business operations.
The Significance of MCSA in Modern Industry
The electric pulse of industry beats to the rhythm of motors, and Motor Current Signature Analysis (MCSA) is becoming the EKG for industrial health. In an age where downtime equals lost dollars, MCSA is the vigilant guardian against costly surprises.
MCSA's Impact on Condition Monitoring and Predictive Maintenance
MCSA is revolutionizing the way we approach machinery upkeeping. By zeroing in on the electrical heartbeat of industrial motors, it detects the faintest whispers of an issue before they crescendo into a full-scale operational opera.
-
Early Detection: MCSA pinpoints flaws like unbalanced phases or bearing wear before they can escalate, providing precious time to act.
-
Scheduled Repairs: By predicting issues, MCSA coordinates with a facility’s cadence, turning what would have been an untimely breakdown into a planned pause.
-
Resource Optimization: Harnessing MCSA data, maintenance teams can prioritize their tasks based on actual motor condition, rather than a rote schedule.
-
Historical Analysis: MCSA's continuous monitoring creates a log of performance over time, granting insights into a component's lifecycle and easing future troubleshooting.
Deep Dive into Fault Detection Through MCSA
Diving headfirst into the data-rich pool of Motor Current Signature Analysis exposes the oft-concealed troubles lurking in electrical motors. It’s like a submarine exploration revealing treasures and shipwrecks; for an engineer, these are the signs of mechanical wear and impending failure.
Identifying Common Issues: Bearing Defects, Rotor Bar Problems, and Misalignment
The cry of a distressed motor is not heard, but rather seen, through the lens of MCSA. It can unmask the stealthy operatives of mechanical failure: bearing defects whispering in high-frequency bands, rotor bar problems mumbling through the stator currents, and the grumble of misalignment casting shadows on the current spectrum.
-
Bearing Defects: Tiny, frequent spikes in frequency signal bearings crying for attention.
-
Rotor Bar Anomalies: Consistent patterns in the spectrum can spell out issues with rotor bars.
-
Misalignment: Look for the telltale signs of phase imbalance and asymmetry indicating misalignment.
Extracting and Interpreting Spectral Metrics from Current Signatures
Within the heartbeat of a motor lies the code to its condition. MCSA deciphers this code not by some ancient art, but by the science of extracting concrete metrics from the ebb and flow of current signatures. It's about reading between the lines—or in this case, the peaks and troughs—to understand the motor's narrative.
-
Amplitude Analysis: Gauging the amplitudes of fault frequencies can reveal the severity and type of fault within a motor.
-
Phase Information: Characterizing phase inconsistencies provides insight into potential misalignment or eccentricity.
-
Waveform Comparison: Contrasting current waveform profiles against the norm flags up potential irregularities.
Fault Classification Systems in MCSA
The game of fault hunting in MCSA is elevated to an art form with classification systems—think of them as the curators of the motor fault gallery. These systems sort the myriad spectrums into neat categories, tagging each frequency spike, each harmonic, with its own place in the context of fault diagnosis.
-
Neural Networks: Pattern recognition through AI-driven neural networks to predict and classify faults effectively.
-
Automated Threshold Detection: Systems that trigger alerts when readings enter predefined territories of concern.
-
Algorithmic Analysis: Advanced algorithms that crunch numbers and sieve through data to tag potential faults.
Integration of MCSA with Advanced Drive System Testing
In the grand theater of modern engineering, Motor Current Signature Analysis (MCSA) is not a solo act. It combines with advanced drive systems to deliver a performance that ensures the safety and efficiency of complex machinery, akin to a duet between technology and industry.
MCSA in Conjunction with Variable Frequency Drives (VFDs)
MCSA works well with Variable Frequency Drives (VFDs) because VFDs control the speed and power of motors, allowing MCSA to accurately analyze and detect faults at different settings.
MCSA, meanwhile, attentively listens to the harmonics and rhythms this produces, providing a deep insight into the performance under these varied conditions. This insightful analysis fine-tunes VFDs for optimized energy consumption and forestalls faults.
Diagnostics for Synchronous and DC Motors
MCSA is a maestro, conducting diagnostics across an orchestra of machines, including the regal synchronous motors and the workhorse DC motors. It assesses the health of these vital components by sifting through their distinctive electrical signatures, spotlighting any abnormal flutters that could hint at mechanical or electrical distress.
-
Alternator Dynamic Eccentricity: Monitoring MCSA for signs of misalignment in motors, which can lead to damaging vibrations.
-
DC Motor Brush Health: Detecting brush wear in DC motors by analyzing the subtle changes in the current's waveform.
-
Excitation Diagnosis: Using MCSA to ensure the excitation systems in synchronous machines operate within their optimal conditions for reliability and service life.
Implementing MCSA in Predictive Maintenance Programs
Every industrial narrative is threading towards a climax where predictive maintenance programs, backed by MCSA, are the main characters. They play a pivotal role in scripting the success stories of factories, plants, and facilities, keeping them up and running without missing a beat.
How MCSA Contributes to Anomaly Detection and Machine Health
A vigilant sentinel, MCSA stands guard over machine health, its analytical prowess tuned to the faintest whispers of anomalies. It's the convergence of precision and preemptive strategy, where subtle electrical signals alert experts to mechanical maladies before they proliferate into production-stopping problems.
-
Early Warning System: MCSA excels in spotting irregularities long before they manifest as breakdowns, serving as a precognitive alert for maintenance teams.
-
Root Cause Revelation: With its ability to detect nuanced changes in motor function, MCSA often points maintenance professionals directly to the root cause of potential failures.
-
Trend Monitoring: MCSA allows for the observation of trends over time, heralding not just individual faults but also offering a panoramic view of machine wellness.
Incorporating MCSA into a Comprehensive Predictive Maintenance Strategy
Predictive maintenance is not just a checklist; it's a philosophy, a way of life for today’s industrial endeavors. MCSA becomes a cornerstone in this approach, harmonizing with other diagnostic tools and strategies to form a veritable symphony of foresight and finesse in maintenance.
-
Data-Driven Decisions: MCSA provides the empirical backbone for maintenance decisions, ushering in an era where guesswork becomes obsolete.
-
Cost Efficiency: Integrating MCSA into predictive maintenance models curtails downtime and extends equipment lifespan, translating to significant cost savings.
-
Holistic Approach: MCSA is a cog in the larger machinery of predictive maintenance, working alongside vibration analysis, thermal imaging, and other diagnostics to provide a well-rounded approach to machine health.
Key Takeaways
The journey through Motor Current Signature Analysis has been rich with insights and surprises. Let's recap the crucial points to remember as we harness MCSA's full potential in protecting industrial processes and enhancing predictive maintenance programs.
-
Versatility and Precision: MCSA's ability to detect a variety of faults in different motor types makes it an indispensable tool for modern industry, delivering meticulous diagnostics with precise anomaly detection.
-
Cost-Effectiveness: With its predictive capabilities, MCSA is not just a technical triumph but a financial one, reducing maintenance costs and practically eliminating unplanned downtime.
-
Advanced Integration: MCSA's synergistic relationship with technologies like VFDs and advanced diagnostic systems widens its spectrum of effectiveness and elevates its status in predictive maintenance.
-
Enhancements in Diagnostics: Innovations like demodulated current spectrum analysis and advanced fault classification systems contribute to deeper, more insightful motor analysis, solidifying MCSA as the cornerstone of condition monitoring.
-
Strategic Implementation: Incorporating MCSA into a comprehensive predictive maintenance strategy ensures that industry leaders can stay ahead of machine failures, optimizing maintenance schedules, and promoting longevity of equipment.
FAQs about Motor Current Signature Analysis
How Does MCSA Differentiate Between Mechanical and Electrical Faults?
MCSA differentiates between mechanical and electrical faults by analyzing the current's signature. Mechanical faults create unique signatures in specific frequency bands by altering the current's harmony, while electrical faults change the fundamental sine wave of the current. By examining these changes in the current's pattern, MCSA can determine whether a fault is mechanical or electrical in nature.
Can MCSA Be Applied to Any Motor Type, Including Servo and Gear Trains?
Yes, MCSA can be applied to any motor type, including both gear trains and servo motors, as it is adaptable to various motor dynamics, provided there is electrical current to analyze.
What Are the Limitations of Motor Current Signature Analysis in Detecting Faults?
The limitations of Motor Current Signature Analysis (MCSA) include its inability to detect very minor faults, susceptibility to interference in electrically noisy environments, the need for expert interpretation to avoid misdiagnosis, and its effectiveness being enhanced when used in conjunction with other diagnostic tools such as vibration sensors and thermal cameras.