How to Identify and Prevent Loose Belt Issues


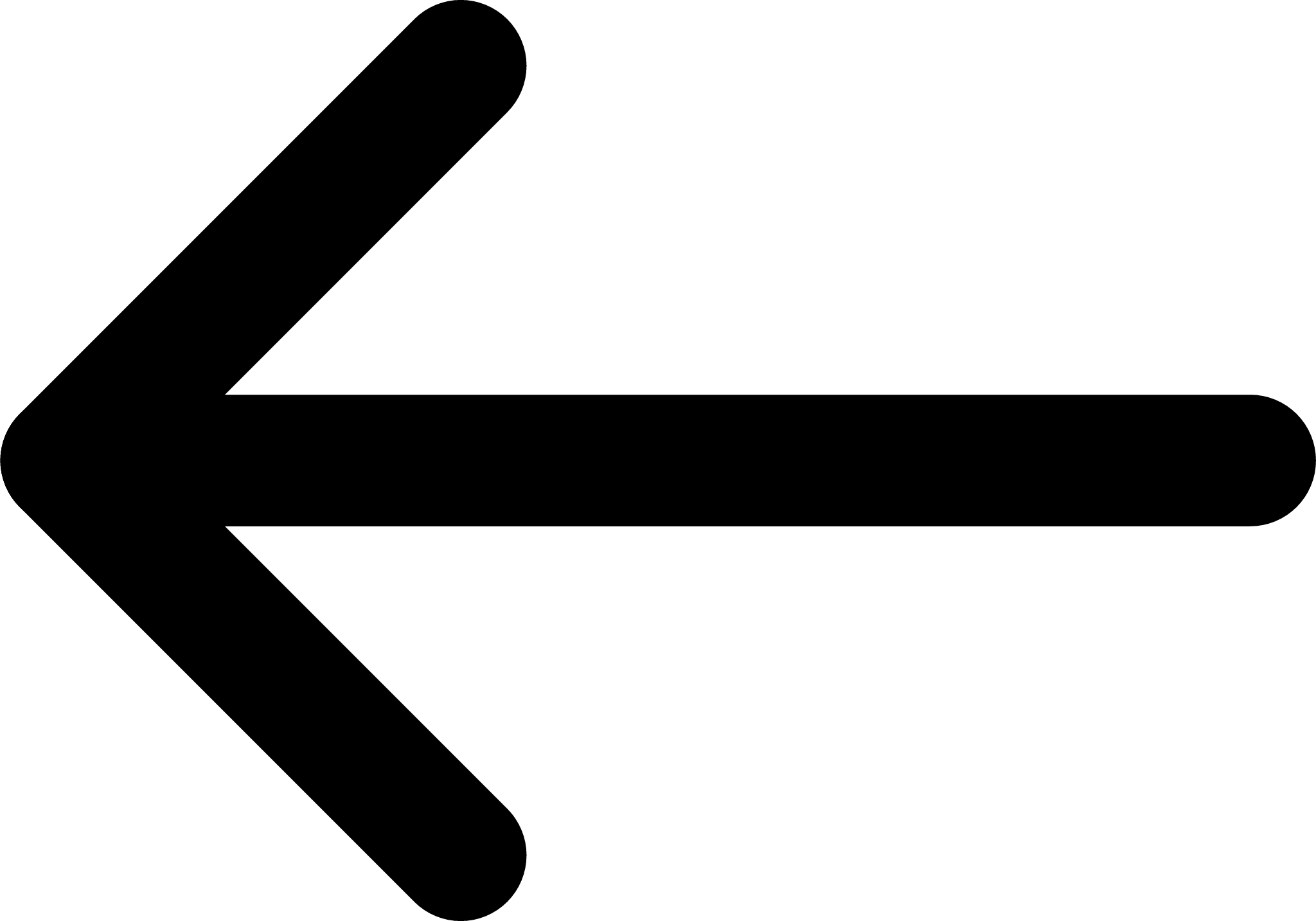
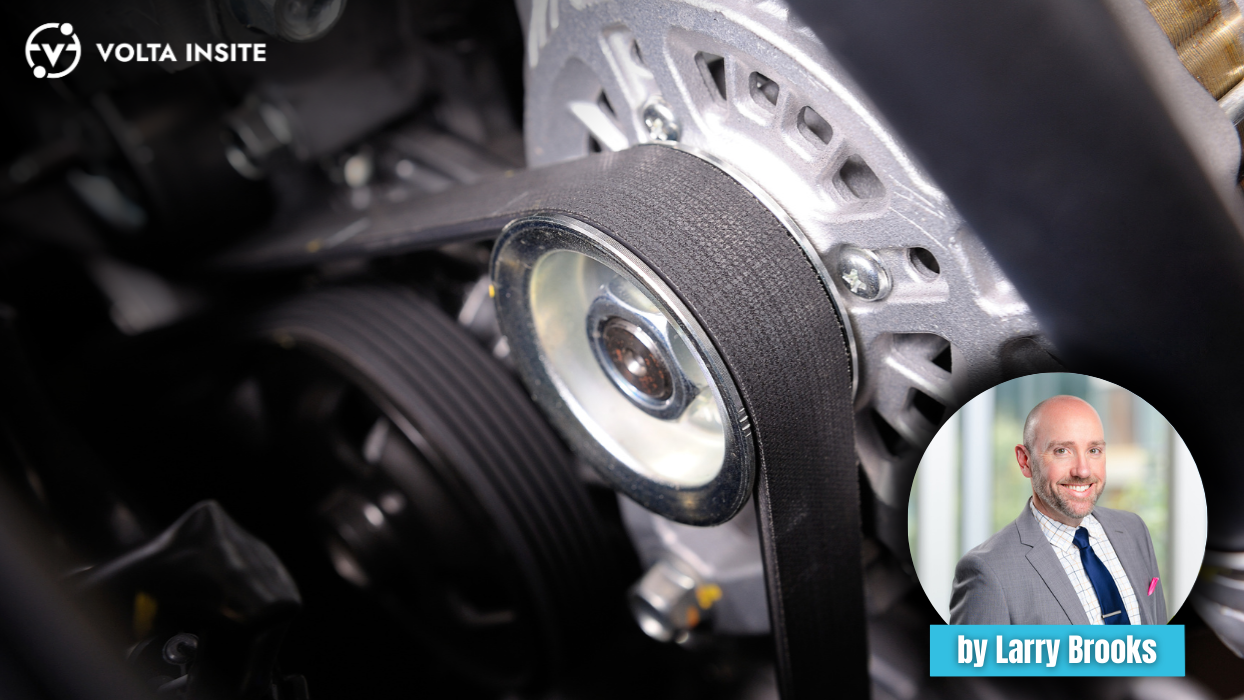
Unnoticed mechanical issues can lead to costly downtime and inefficiencies in facility operations. One common but often overlooked issue is a loose belt in machinery. Whether in HVAC systems, conveyors, or elevators, a loose belt can create significant operational challenges, including energy waste, system wear, and unexpected failures. Identifying and addressing a loose belt before it leads to equipment failure is critical for maintaining efficiency and preventing costly disruptions.
The Hidden Dangers of a Loose Belt
A loose belt may seem like a minor issue, but it can have far-reaching consequences:
Reduced Efficiency
A belt that isn’t properly tensioned can slip, leading to inefficient power transfer and increased energy consumption.
Increased Wear and Tear
Slipping belts cause excess friction, leading to premature wear on pulleys, bearings, and other components.
System Overheating
Loose belts create unnecessary strain on motors, which can lead to overheating and reduced lifespan.
Unexpected Downtime
If a belt fails completely, it can shutdown critical systems, causing unplanned maintenance and operational disruptions.
How to Identify a Loose Belt Before Failure
In traditional maintenance practices, belts are checked manually for cracks, abrasions, separation or other damage during scheduled inspections. However, this method often fails to detect gradual loosening or early warning signs of failure. By the time visible signs appear—such as squealing noises, vibration, or performance drops—damage may already be occurring.
How InsiteAI Detects Loose Belts Before They Cause Downtime
Volta Insite’s InsiteAI solution provides real-time monitoring and predictive analytics to detect loose belts early—before they lead to costly failures.
Tracking Harmonics to Identify Belt Issues
When a Variable Frequency Drive (VFD) operates at multiple speeds, it generates specific harmonic signatures based on the gearing of the system. For example, in an elevator system, a loose belt harmonic typically appears at 71% of the line frequency.
With InsiteAI, facility managers can:
-
Trend harmonics over time to detect gradual belt loosening.
-
Receive automated alerts when the system detects abnormal trends, enabling proactive maintenance.
-
Avoid costly downtime by scheduling repairs before failures occur.
Real-World Example: Proactive Loose Belt Detection
In April 2021, a facility using InsiteAI established a baseline for its elevator system’s harmonic trends. Over time, the system detected a gradual increase in the 71% line frequency harmonic, signaling a potential loose belt issue.
Upon receiving an alert, facility staff inspected the equipment and confirmed the belt was loosening. After performing maintenance, the harmonic levels returned to baseline—preventing a potential failure and costly downtime.
Improve Reliability with InsiteAI
Loose belts don’t have to disrupt your operations. With InsiteAI’s predictive analytics, you gain the ability to:
-
Detect early signs of mechanical wear.
-
Reduce emergency repairs and unplanned downtime.
-
Extend the lifespan of critical equipment.
-
Optimize facility efficiency and reliability.
Enhance your peace of mind with proactive maintenance. Contact Volta Insite today to learn how InsiteAI can help you identify and prevent loose belt issues before they impact your operations.