The Cost of Downtime and How to Minimize Losses at Your Facility


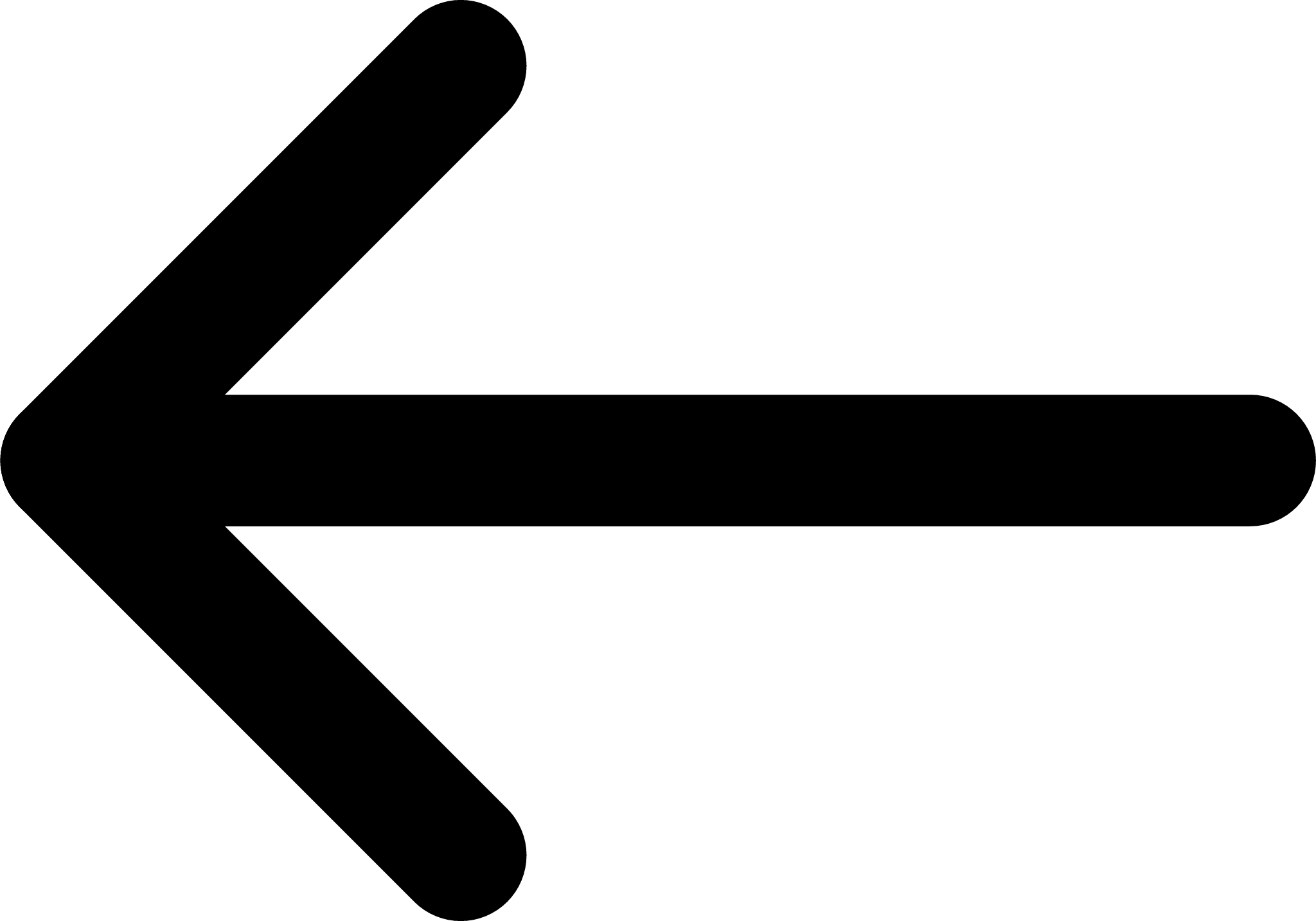
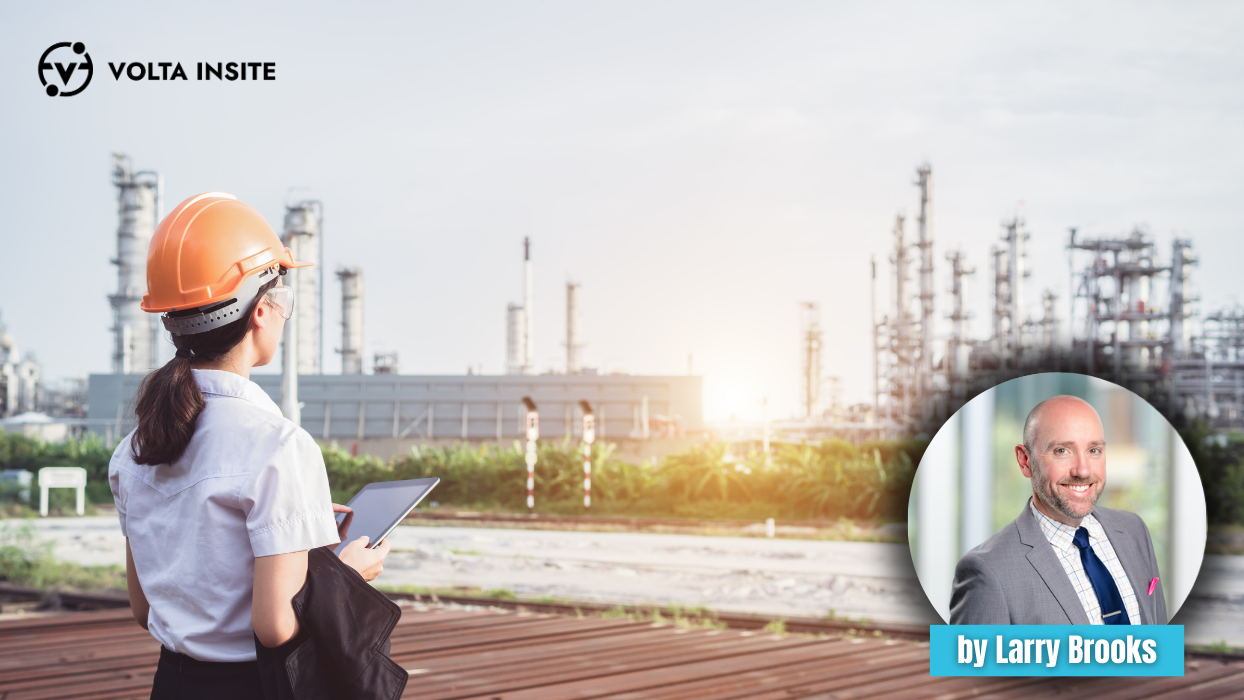
Due to highly automated and interconnected facility environments, downtime can have devastating financial impacts. The cost of downtime varies significantly across industries, and understanding the criticality of equipment is essential to mitigating these losses.
For light manufacturing, downtime can cost around $250,000 per hour. This can quickly scale up depending on the complexity of the production line and the number of processes involved. For industries like energy, the costs are even more staggering. A single hour of downtime in the energy sector could result in losses up to $2.5 million. These figures highlight just how critical it is to keep equipment functioning smoothly and avoid costly disruptions.
Why Equipment Criticality Matters
The criticality of a component isn't just about its direct value but about its role within the larger operational system. For example, a motor or pump may seem like just one small part of an industrial process. However, if that motor drives a crucial conveyor or production line, a failure could halt the entire operation. This is particularly true in facilities where processes are tightly integrated—one weak link in the chain can bring the entire production floor to a standstill.
In contrast, non-critical equipment, while still important, may not result in a full shutdown if it fails. Understanding the difference between critical and non-critical equipment helps facility managers prioritize maintenance and allocate resources effectively.

How to Identify Critical Equipment in Your Facility
To prevent downtime, it’s vital to assess which equipment is most critical to your operations. Here are a few steps to help identify critical equipment:
Assess Process Flow
Map out how each component contributes to the overall production process. Identify which pieces of equipment are integral to maintaining operational continuity.
Consider Redundancy
Determine whether certain equipment has redundancy built into the system. If a motor fails, can another system take over, or does the entire operation halt?
Evaluate Repair Time and Costs
Equipment that takes longer to repair or costs more to replace is often deemed more critical. Knowing how long it would take to bring the system back online after a failure can help you understand the urgency of maintaining specific components.
Safety and Compliance
Some equipment, such as those tied to environmental compliance or worker safety, can be critical not just for operations but also for regulatory reasons. Failure in these areas can lead to costly fines and legal liabilities on top of downtime costs.
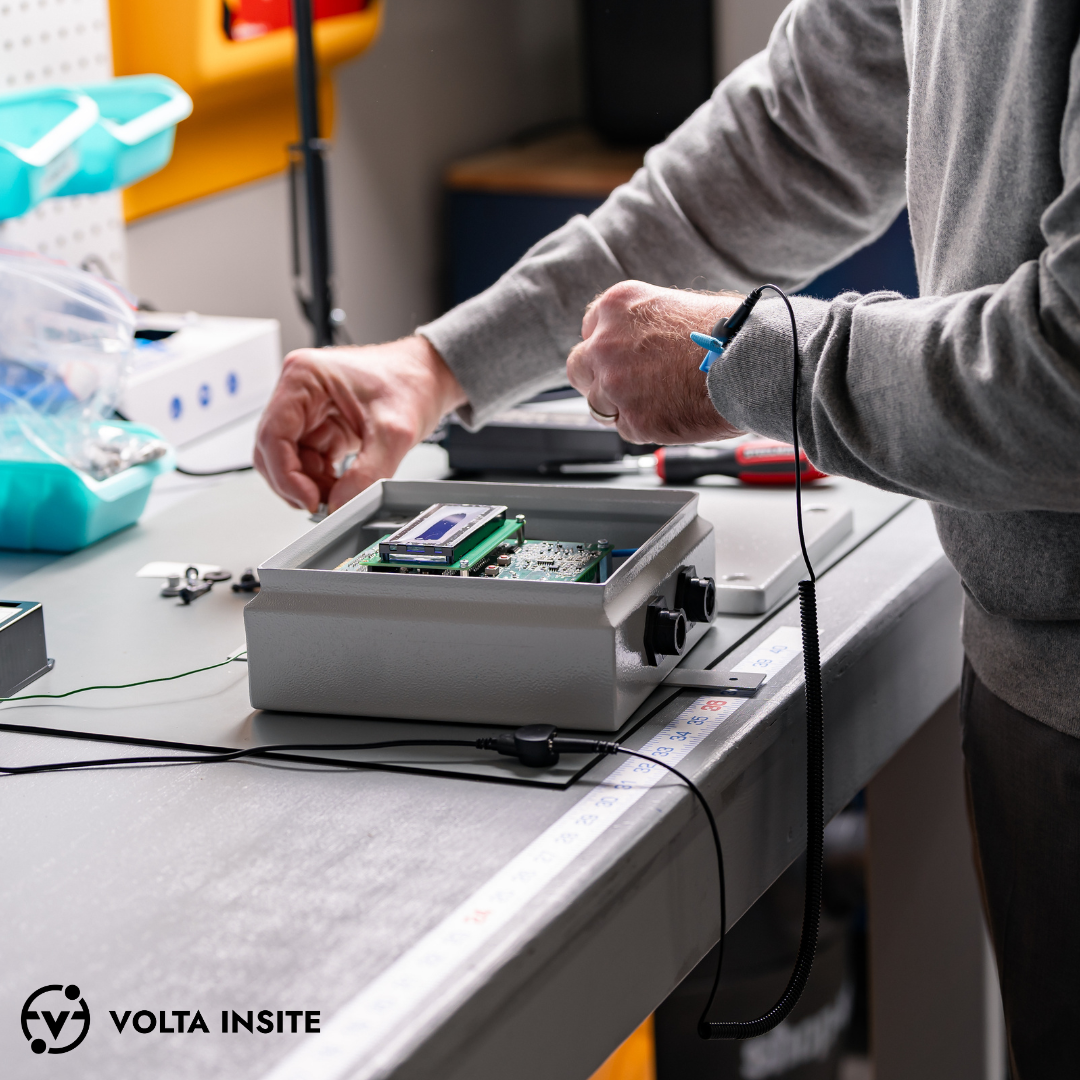
By understanding what equipment is critical to your facility, you can better plan for maintenance, repairs, and contingencies to ensure minimal impact on operations.
How Volta Insite Can Prevent Downtime with InsiteAI
Volta Insite offers advanced solutions designed to help you prevent costly downtime at your facility. With InsiteAI, you can monitor the health of critical electrical assets in real-time, predict failures before they happen and prioritize maintenance tasks based on actionable data. This AI-driven platform ensures that your facility operates at peak efficiency, reducing the risk of unexpected breakdowns and costly interruptions. Trust Volta Insite to keep your operations running smoothly and prevent downtime from taking a toll on your bottom line.
Resources:
4 Ways to Reduce Downtime in the Oil & Gas Industry with Predictive Maintenance